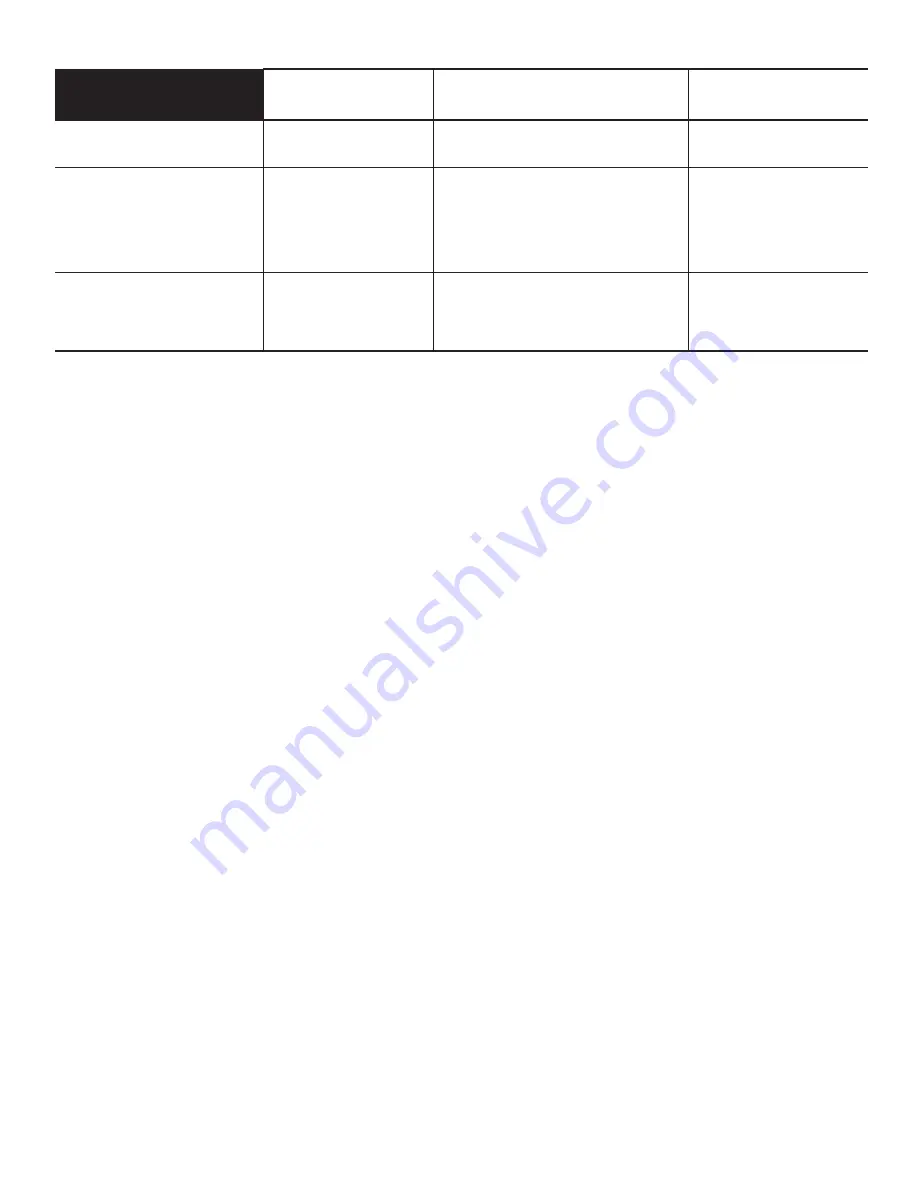
11
Inspection Steps
1. Inspect for misaligned, bent, cracked, distorted, worn,
malfunctioning or damaged parts; loose fasteners or
missing parts/components; deterioration; corrosion; or any
other indications of damage/problems that may affect the
integrity and operation of the product. Also inspect any
accessory components and parts (i.e., rescue rope grab,
rope anchor, etc.) for the same.
2. Inspect the entire length of rope lifeline (as well as the
rope anchor, if applicable) for cuts, burns, severely abraded
areas, and excessive wear. The lifeline must freely pull
through the device in both directions.
3. nspect carabiners for damage, distortion, corrosion, or
pitted surfaces. The carabiner gate should seat into the
nose without binding and should not be distorted or
obstructed. The gate locking mechanism must prevent the
gate from opening when closed.
4. Inspect all other system components (i.e, harness, rescue
lanyard, anchorage connector, etc.) according to the
manufacturer's instructions.
If inspection reveals a defect in condition or operation,
or if the device has been used in an emergency rescue situation,
it must be removed from service immediately!
Cleaning and Storage
Basic care of all Miller equipment will prolong the life of the
unit and will contribute toward the performance of its vital
safety function. Periodically clean the device and lifeline with
water and a mild detergent. The device should be positioned
so that all excess water drains out. The lifeline must be allowed
to naturally air dry. Do not force dry with heat sources. The
unit should be stored in a dry, cool and clean environment and
protected against UV irradiation. Storage areas should be free
of exposure to fumes, acids, corrosive elements, oils and heat
sources.
Servicing
Servicing must only be carried out by Miller Fall Protection or
a service center authorized, in writing, by the manufacturer. A
record log of all servicing and inspection dates for this system
must be maintained. Only original Miller Fall Protection
replacement parts are approved for use in this system. Non-
repairable devices must be disposed of in a manner to prevent
inadvertent further use. Contact Miller Technical Services at
800.873.5242 if you have any questions.
SafEscape ELITE
Rescue/Descent Device
Inspection Crite
ria
Inspection
Required
by User
Inspection
Required by
Competent Person
Factory
Recertification
Required
For a Properly Stored, Unused
Unit ...
Before each use
At least annually
Every 7 years
For a Unit Used in Non-Emergency
Conditions, Training, and Regular
Use ...
Before each use
At least annually AND
after every 3,280 ft (1000 m)
of descent distance
for a user weighing
220 lbs (100 kg)
After 9,842 ft (3000 m)
of descent distance
for a user weighing
220 lbs (100 kg)
For a Unit Used in an Emergency
Rescue Situation ...
REMOVE
FROM SERVICE
IMMEDIATELY
FOR FACTORY
RECERTIFICATION
REMOVE
FROM SERVICE
IMMEDIATELY
FOR FACTORY
RECERTIFICATION
Must be returned
immediately for
factory recertification
NOTE: Extreme weather conditions or heavier descent loads require more frequent inspections.