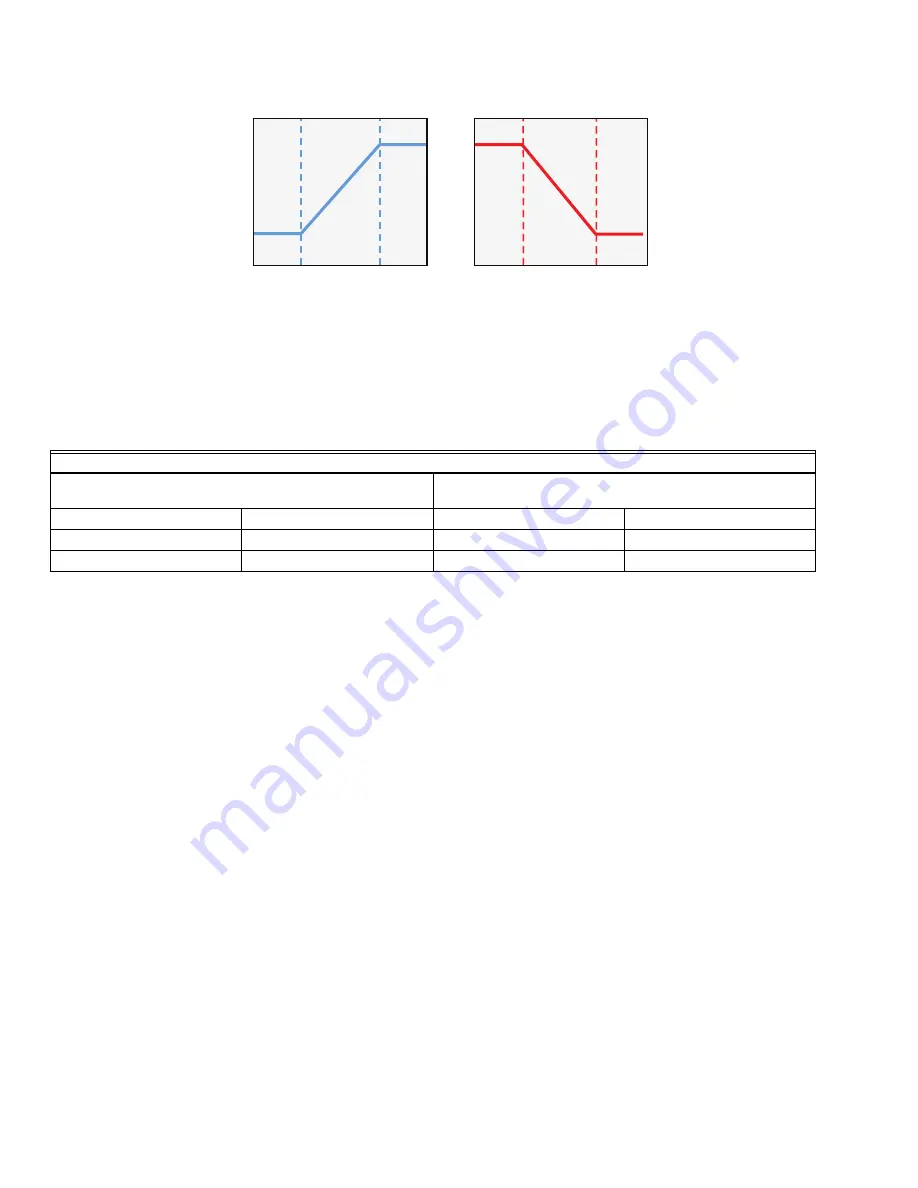
LCBS CONNECT SOLUTION
31-00118EFS—01
14
Fig. 4.
A direct acting control loop is one where the output increases as the input sensor value rises above the set point.
A reverse
acting control loop is one where the output increases as the input falls below the set point. Direct or reverse acting should
be selected based on the application requirements with the consideration that set point is the "no load" value of the
measured variable and with 0% output the energy input should be the closed or off. The physical outputs can be
configured to match the controlled devices (normally open, normally closed, energized on, energized off, etc.).
The proportional calculation determines proportional error (Ep). Proportional error is the deviation from set point of the
sensed medium (input sensor) divided by the throttling range expressed in units of the input sensor. The set point is the
value of the input sensor at which the control loop is satisfied. When the input sensor value is at set point there is no
proportional error and the output is 0%. The throttling range is the amount of change in the sensed medium required to
drive the output from 0 to 100%. By definition, in proportional control the input value must deviate from set point to
initiate a change in the output.
Selected Throttling Range must be narrow enough to provide good control without becoming unstable. The throttling
range is determined by a number of factors such as the control application, the response time to the equipment being
controlled, and the control algorithm being used. The narrower (smaller) the throttling range, the more precise the control
and the wider (larger) the throttling range, the more stable the control. The objective is setting the throttling range to
achieve the optimum balance between precision and stability.
Set point and Differential Refresher - On Off, Digital Control
The following is a refresher course for you and describes the relationship between set point and differential for heating
and cooling. These settings are typically programmed for each control loop and each on off output.
In heating mode, the differential is below the set point. The output relay de-energizes when the temperature rises to the
set point. As the temperature drops to the set point minus the differential, the relay energizes. You will also see this
referred to as "direct acting," where increased control action is in direct relationship to increased temperature value.
APPLICATION EXAMPLES
DIRECT ACTING. CONTROL DEVICE INCREASES AS
MEASURED VALUE INCREASES
REVERSE ACTING. CONTROLLED DEVICE DECREASES
AND MEASURED VALUE INCREASES
COOLING
STATIC PRESSURE
HEATING
LIGHTING
DEHUMIDIFICATION
CHILLED WATER PUMP
HUMIDIFICATION
STATIC PRESSURE
MIXED AIR
CONDENSER WATER PUMP HOT WATER PUMP
70°F
72°F
74°F 76°F
78°F
SENSOR INPUT VALUE
EXAMPLE: COOLING – DIRECT ACTING
SETPOINT 72°F THROTTLING RANGE 4°F
CONTROLLER OUTPUT %
100%
80%
60%
40%
20%
0%
THROTTLING
RANGE
SENSOR INPUT VALUE
EXAMPLE: HEATING – REVERSE ACTING
SETPOINT 76°F THROTTLING RANGE 4°F
CONTROLLER OUTPUT %
100%
80%
60%
40%
20%
0%
THROTTLING
RANGE
70°F
72°F
74°F 76°F
78°F
MCR36698
Содержание LCBS Connect
Страница 43: ...LCBS CONNECT SOLUTION 43 31 00118EFS 01 ...