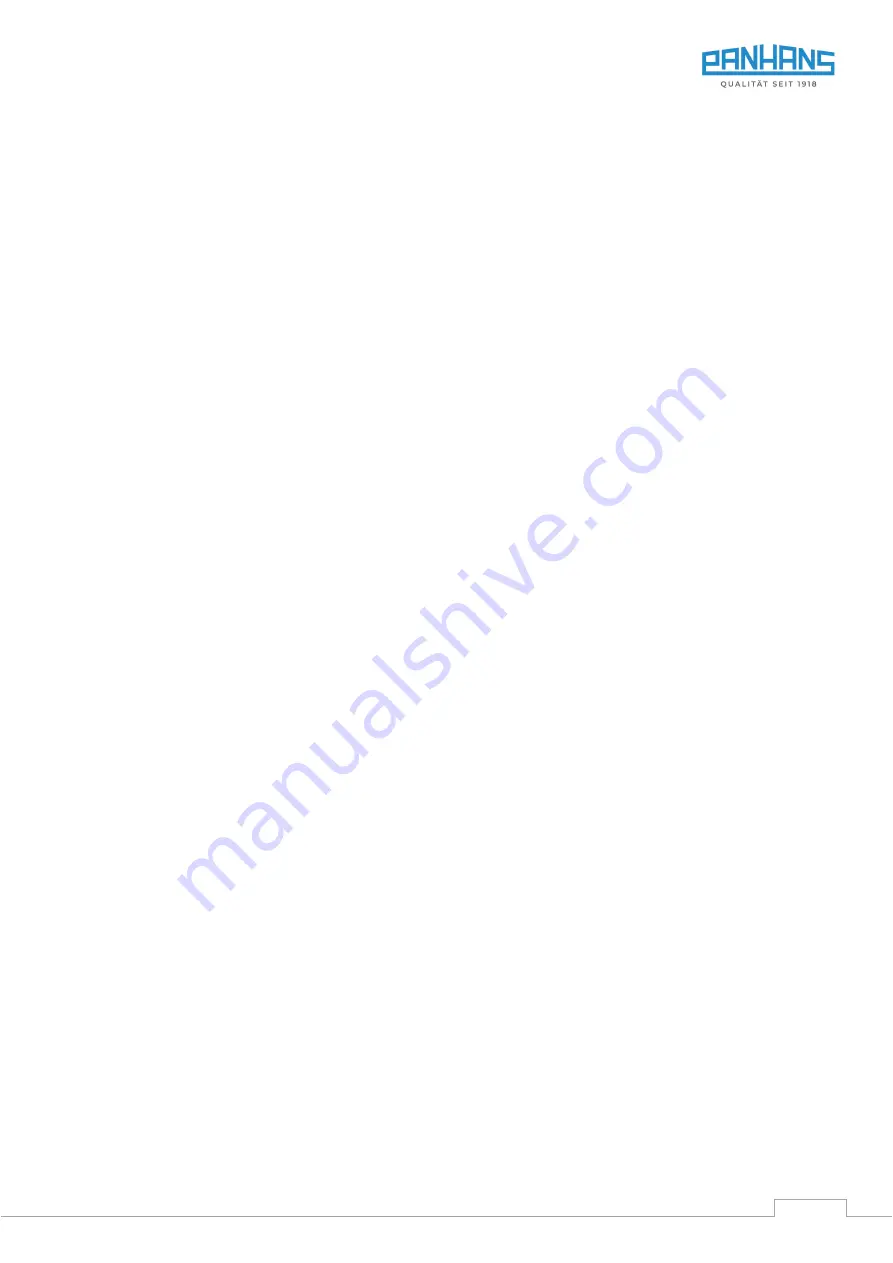
BA_PH_245-20_EN_15-22.docx
20
4.4.9.1
Milling at the fence, where the machining extends over the full workpiece length
With workpieces that usually have a right-angled cross-section over their entire length, this machining operation
is carried out by using a milling fence. Since the fence rulers are at a 90° angle to the table top, the workpiece
can be guided at right angles along the fence rulers.
Since the opening between the fence rulers on a table milling machine must be wide enough for the tool to pass
through, unnecessary danger areas are created on the knives, on the tool body and on the spindle. The gap
between the two fence rulers must be closed as much as possible. Otherwise there is a risk that the workpiece
leading edge will catch on the edge of the take-off ruler. These hazards are avoided by the use of an auxiliary
fence or suitable fence bridges, protective inserts, etc.
The manufacture of an auxiliary fence must be carried out with care. It is recommended that the knives are
passed through by fine adjustment of the fence and not by pushing the fence into the tool by hand.
4.4.9.2
Insert Milling
Insert milling is milling at the fence, whereby the workpiece is not machined over its entire length. Instead of
starting the cut at the beginning of the workpiece, the knives must plunge into the solid material and (depending
on the requirement) plunge out again before reaching the end of the workpiece.
The splinter tabs must be placed
as close as possible to the cutter.
If the workpiece cannot be held safely by hand due to its small dimensions, a tenoning clamp or another work-
piece holding device, together with a suitable guard (which secures the tool as far as possible) must be used. The
tenoning clamp must allow fast and accurate insertion of the workpiece and ensure firm clamping.
A securely fastened front cross fence as well as a kickback guard (e.g. type 1648, see section
16.10) must also
be used. For very long workpieces, use an auxiliary fence if necessary.
Quick clamps, acting either via toggle levers or eccentrics, ensure fast and convenient workpiece clamping. Quick
clamps, acting either via toggle levers or eccentrics, ensure fast and convenient workpiece clamping. Rear and/or
front cross fences attached to the fence or on the table ensure more accurate work with the tenoning clamp. In
addition, extension and retraction bars should be provided on the tenoning clamp.
4.4.9.3
Curved Milling
For shaping the workpiece to be machined, a clamping template must always be used for curve milling. The shape
of the workpiece is achieved by pressing the template against the ring fence guard (see section
14.4.2), while
the knives are simultaneously passing by.
A clamping template cannot be used if the operation makes this impossible, e.g. if
•
the workpiece is so large that the use of the template makes the work impracticable or
•
the workpiece is so small or so shaped that a secure fixture in the template is not possible.
4.4.9.4
Inclined Milling
A special clamping device or inclinable stop rulers must be used to ensure a secure support during inclined mill-
ing. Push sticks must be used at the end of the milling process.
4.4.9.5
Climb Milling
Climb milling is a very dangerous operation as the operator is not able to stop the sudden forward movement of
the workpiece when it is caught by the knives. In addition, the workpiece can be dangerously ejected. Climb
milling should generally be avoided, even if a clamping device or a workpiece holding device is used. If the "Climb
Milling" button is pressed on the control panel, a warning message appears on the touchscreen of the control.
The process must be confirmed by the machine operator.
4.4.9.6
Other Work
If other work is carried out on the machine, suitable clamping devices or workpiece holding devices must be used
to reduce the risk of accident.