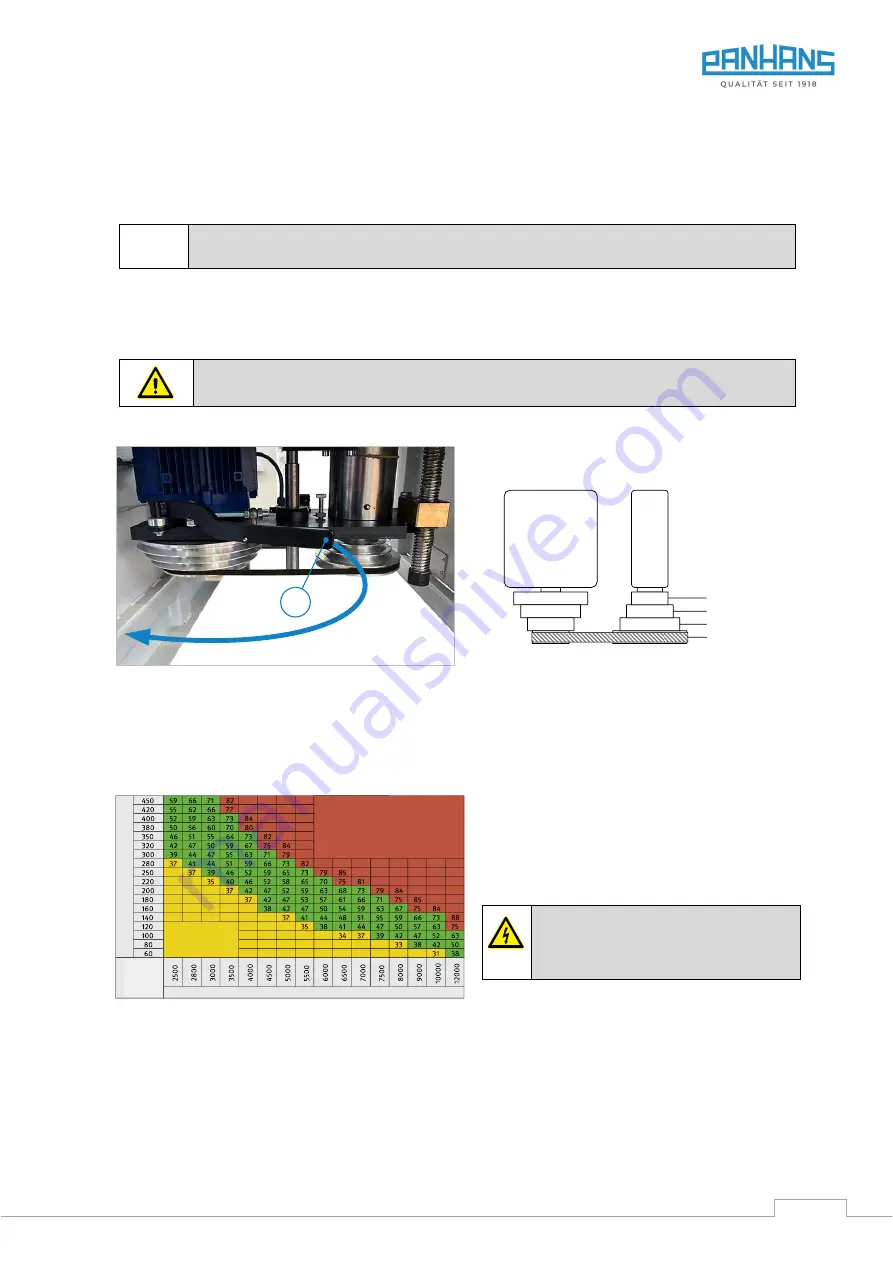
BA_PH_245-20_EN_15-22.docx
33
10.2
Emergency Stop Function
In case of danger or malfunctions during operation, the machine can be stopped quickly and reliably by pressing
the emergency stop button (
4
) on the control panel (see
Before restarting the machine, the emergency stop button must be unlocked again.
The braking time of the motor to a standstill can be up to 10 seconds.
11
Speed Setting
With the 245|20 spindle moulder, the speed is adjusted by shifting the V-belt.
Switch off the machine during speed adjustment and secure it against unexpected restarting.
Lock the main switch with a padlock!
After switching off and locking the main switch, open the front service door and proceed as follows:
Figure 13: Lever to release the V-belt
•
Swivel lever (
E
) according to
•
Set the loosened belt to the desired speed:
•
To tension, swing lever (
E
) back again.
•
After the adjustment, set the brake release switch back to the right-hand position (normal operation).
Please also read the chapter
“Change and Tighten the Drive Belt”.
11.1
Cutting Speed Chart
Figure 14: Cutting Speed Chart
There is a cutting speed chart on the right-hand side
of the machine.
•
Select the speed for the cutter used according to
the chart and be sure to avoid settings within the
danger zones marked in yellow and red.
Increased risk of kickback, breakage
and/or noise pollution when choosing a
non-recommended setting!
E
Motor
6000 rpm
9000 rpm
3000 rpm
4500 rpm
Risk of breakage,
increased noise pollution
Increased
risk of kickback
To
o
l d
ia
m
et
er
(
m
m
)
Milling arbor speed (
min
-1
)