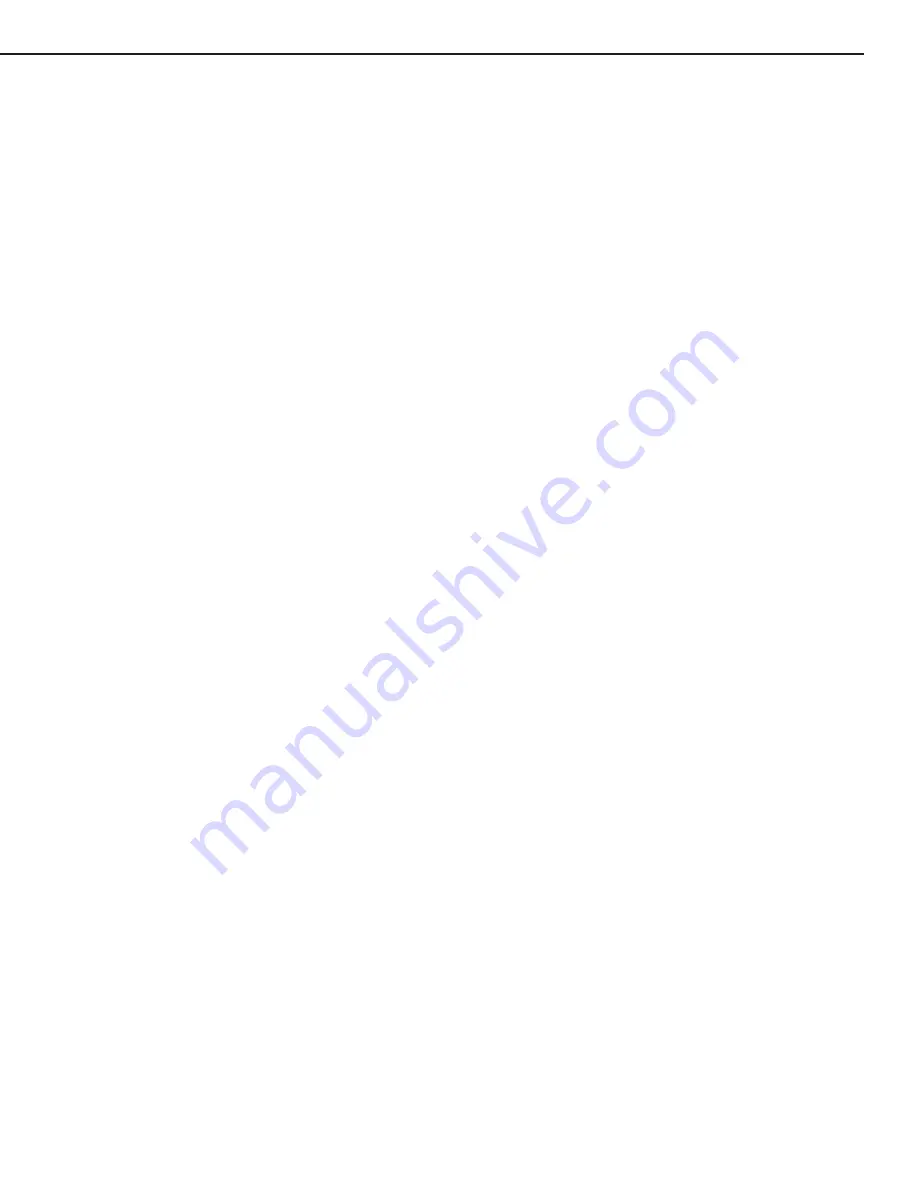
50
AdaptaPAK® Maintenance and Troubleshooting
Other Checks
All electrical connections (including those at the compressor terminals) should be periodically checked for tightness.
Loose connections contribute to low-voltage conditions that may cause motor failure.
Refrigerant connections should be inspected to insure that they have not loosened. Whenever it is necessary to add
refrigerant, a careful leak check of all refrigerant connections should be made.
The oil level in the compressor crankcase should be at the specified level in the sight glass at all times. If the oil
level is low, more oil should not be added until the cause of the oil migration is corrected. Check the expansion valve
adjustment, the size of the risers and traps and the head pressure control valve settings.
If the oil level continues to remain low, pump the system down a few times to see if it will bring the oil back. On hot
gas systems, put a few cases in defrost. Check the evaporator coils and make sure none are iced up. Check the oil
in the oil reservoir, and if there is plenty of oil in the reservoir but a compressor that is low, adjust the oil float on that
compressor. Make sure oil is not pumping out of the compressor through a bad valve plate or bad cylinder.
Dirty, discolored oil may indicate one of two things:
•
Contaminants such as moisture, air, etc., trapped in the system. If the discoloration is not severe, a new
liquid line filter-drier and 1 or 2 oil filters are usually enough to remove contamination and clean the oil. If
the discoloration is severe and caused by contamination alone, the oil should be replaced and a new liquid
line filter-drier and oil filter installed as many times as necessary to eliminate the contamination.
•
Excessive system pressure drop or improper control settings. Compressors that operate in a vacuum result
in oil discoloration due to motor overheating. The resulting inadequate suction cooling causes overheating
of the motors.
Preventive Maintenance
Preventive maintenance, as the name suggests, is intended to stop problems before they happen. Preventive
maintenance, when performed at the intervals specified below, reduces problems and keeps the system running
smoothly.
Preventive maintenance should, in particular, be performed on unit coolers, air-cooled condensers, and fluid coolers
that are connected to the AdaptaPAK® systems.
Unit Coolers
At every six month interval, or sooner if local conditions cause clogging or fouling of air passages through the finned
surface, the following items should be checked:
1. Visually inspect unit
a. Look for signs of corrosion on fins, cabinet, copper tubing and solder joints.
b. Look for excessive or unusual vibration for fan blades or sheet metal panels when in operation. Identify fans
causing vibration and carefully check motor and blade.
Содержание Adaptapak ADP-M0000-L0032
Страница 4: ...4 AdaptaPAK Parallel Refrigeration System ...
Страница 20: ...20 AdaptaPAK Parallel Refrigeration System ...
Страница 26: ...26 multiMAX Controller for AdaptaPAK Hillphoenix AdaptaPAK multiMAX Controller Input Output Schedule left side ...
Страница 28: ...28 multiMAX Controller for AdaptaPAK ...
Страница 66: ......