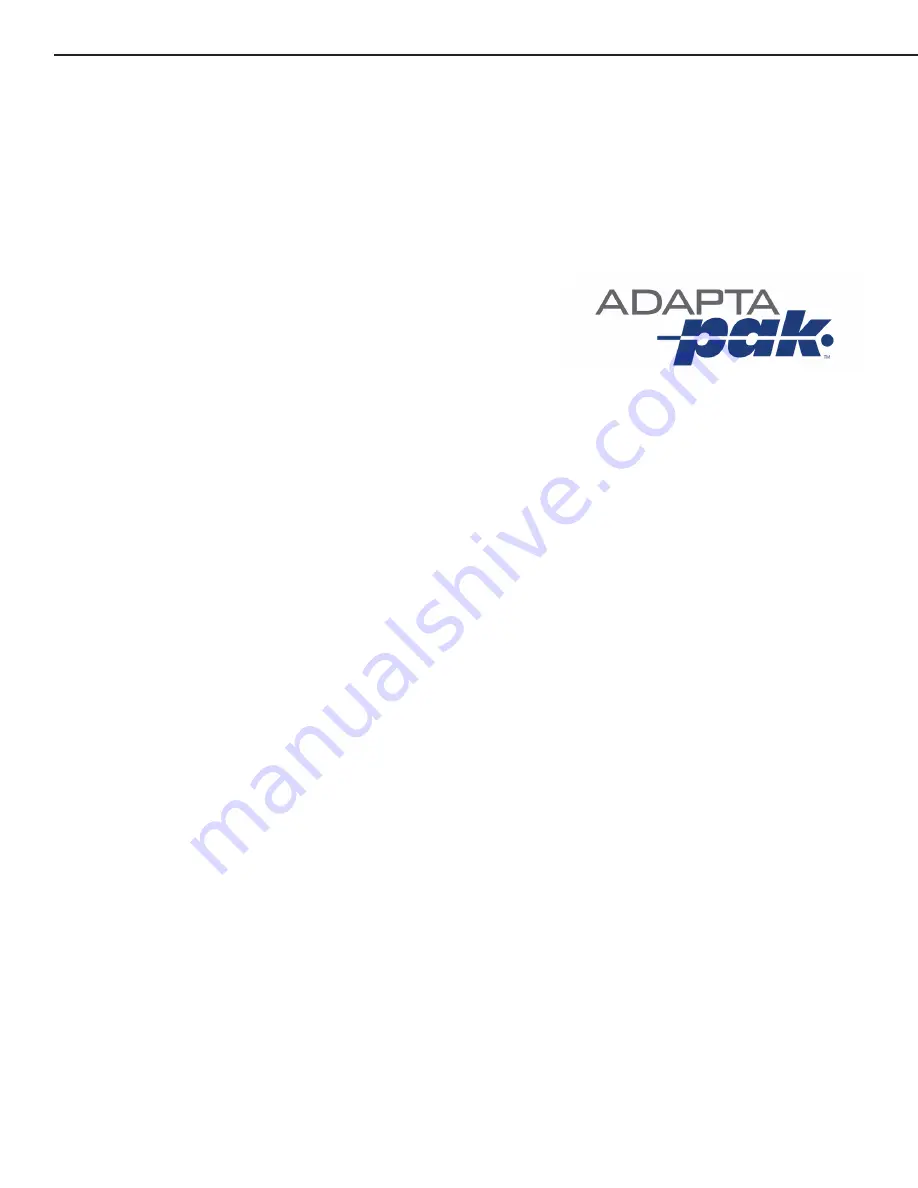
45
AdaptaPAK® Maintenance and Troubleshooting
Section 5:
AdaptaPAK
®
Maintenance and
Troubleshooting Procedures
Supermarket refrigeration systems like the AdaptaPAK® system
are complex arrangements of equipment and machinery involving
numerous components spread among a variety of subsystems that
provide refrigeration to the store’s different circuits and loops. In order
to keep all that equipment and machinery running safely and efficiently,
regularly scheduled maintenance must be performed. However, regardless of how well maintained the equipment is,
problems will occur from time to time. Like any other kind of machinery, and especially like other complex systems,
something will eventually fail to work as designed. In those cases, there are troubleshooting procedures that aid in
determining the causes of various problems. This section presents the maintenance and troubelshooting procedures
for Hillphoenix AdaptaPAK® refrigeration systems.
Maintenance Procedures
Refrigeration equipment has been noted to account for approximately 50% of the total electrical power consumption
of the typical supermarket. In DX systems the compressors generally consume the greatest portion. As such, there is
considerable potential for conservation measures to have a huge impact on the store’s operating costs through the
application of proper maintenance procedures.
Foremost among the maintenance procedures for DX systems is checking the system’s safety and operating
controls. The checks to be performed also include verification that the original settings are maintained.
Operating Strategies — Maintaining Compressor Efficiency
One means of reducing a compressor’s electrical consumption (and a store’s resulting operating costs) is to lower
the discharge (head) pressure. The head pressure will be at its highest during the heat of summer, when the ambient
temperature is close to design conditions. This is also when the compressor motor amperage will be at its highest.
Because more work is required to compress a vapor to a higher pressure, it logically follows that more electrical
energy is required to accomplish this. There is a proportional relationship between head pressure and compressor
motor current draw. When head pressure is either raised or lowered, the motor current draw will increase or
decrease in proportion. For example, one manufacturer’s 20 HP compressor, using R-404A, and operating at
-25ºF SST (13 psig) and 110ºF SCT (272 psig), with 5ºF liquid subcooling, and a 50ºF return gas temperature, will
deliver 61,389 Btu/h. Under these conditions the compressor motor’s current draw is 40 amps. A 30ºF reduction
in condensing temperature (110ºF to 80ºF) will reduce the current draw to 37.3 amps. While a 6.75% reduction is
significant, it is only part of the story.
Содержание Adaptapak ADP-M0000-L0032
Страница 4: ...4 AdaptaPAK Parallel Refrigeration System ...
Страница 20: ...20 AdaptaPAK Parallel Refrigeration System ...
Страница 26: ...26 multiMAX Controller for AdaptaPAK Hillphoenix AdaptaPAK multiMAX Controller Input Output Schedule left side ...
Страница 28: ...28 multiMAX Controller for AdaptaPAK ...
Страница 66: ......