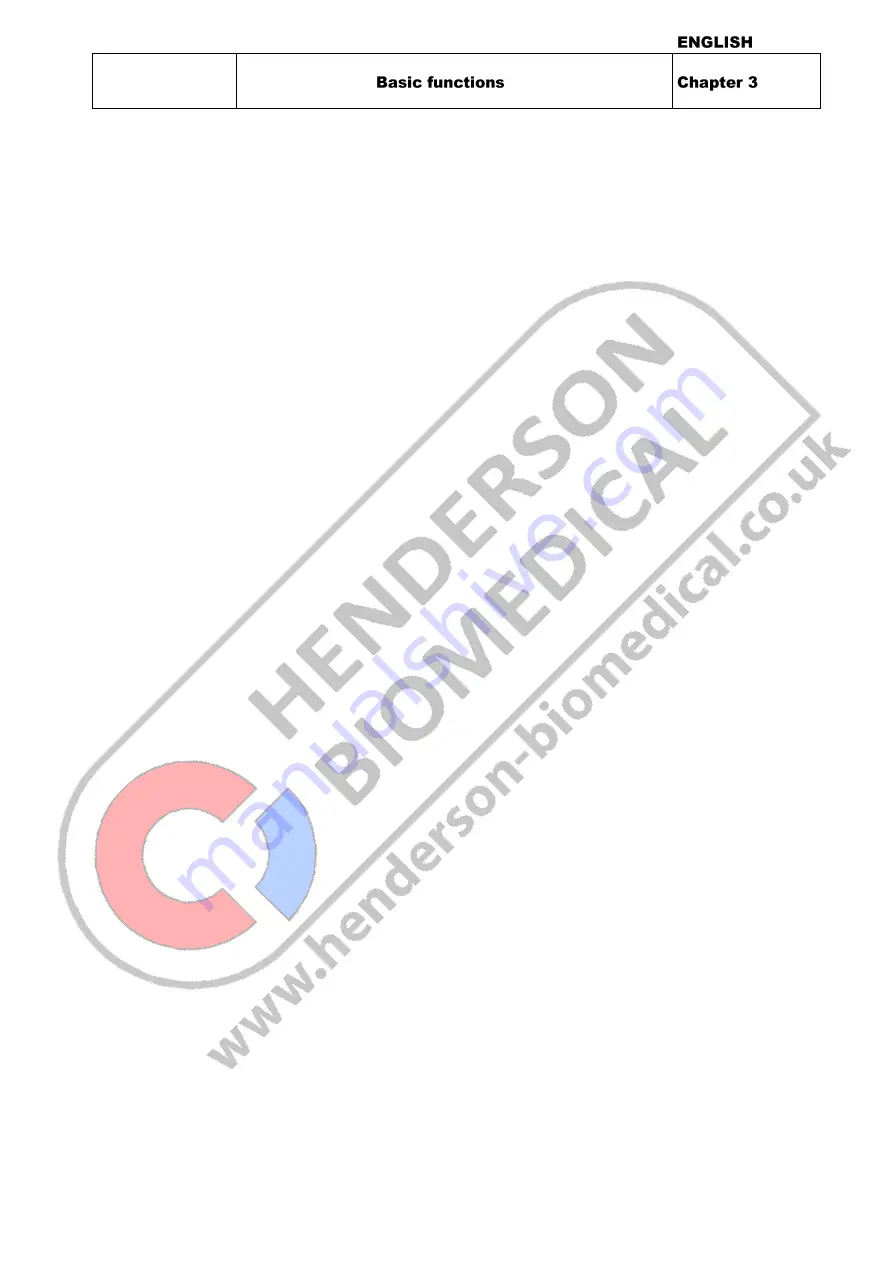
hd 680 DEI-V
ValiDoc Pro
Page GB 39
9.693.018
Version 1.06
3.8 Manufacturer recommendation for routine checks
3.8.1 Routine checking of sealing seam quality criteria
Ideally this can be carried out using the hawo ink test or the hawo SEAL CHECK test.
It is recommended that the test is carried out daily before starting work and that the results be
recorded in the documentation table in Appendix 1 of these operating instructions .
3.8.2 Annual sealing seam strength checks
This takes place by means of a peel test according to EN 868-5, Appendix E: "Method for
determining the peel characteristics of paper/plastic laminate products":
Introduce reel section into the sealing device and seal on peel side.
a) Expose the sealed reel section to a sterilisation cycle.
b) Slowly and carefully peel the sealing seams apart by hand.
c) Visually check that the sealing seam extends along the total width and length. There
must be no splitting of the paper more than 10 mm from the sealing seams. The results
must be recorded.
3.8.3 Routine checks of critical process parameters
Your sealing device is equipped with a temperature and pressure sensor. The critical process
parameters are automatically controlled with each sealing seam. Deviations will be displayed
as error messages (see 4.3.2). It is recommended that the critical process parameter values
are retrieved daily before starting work and that these are recorded in the documentation table
in Appendix 1 of these operating instructions.
Set temperature on the display
Contact pressure and sealing time - see section 3.3.5