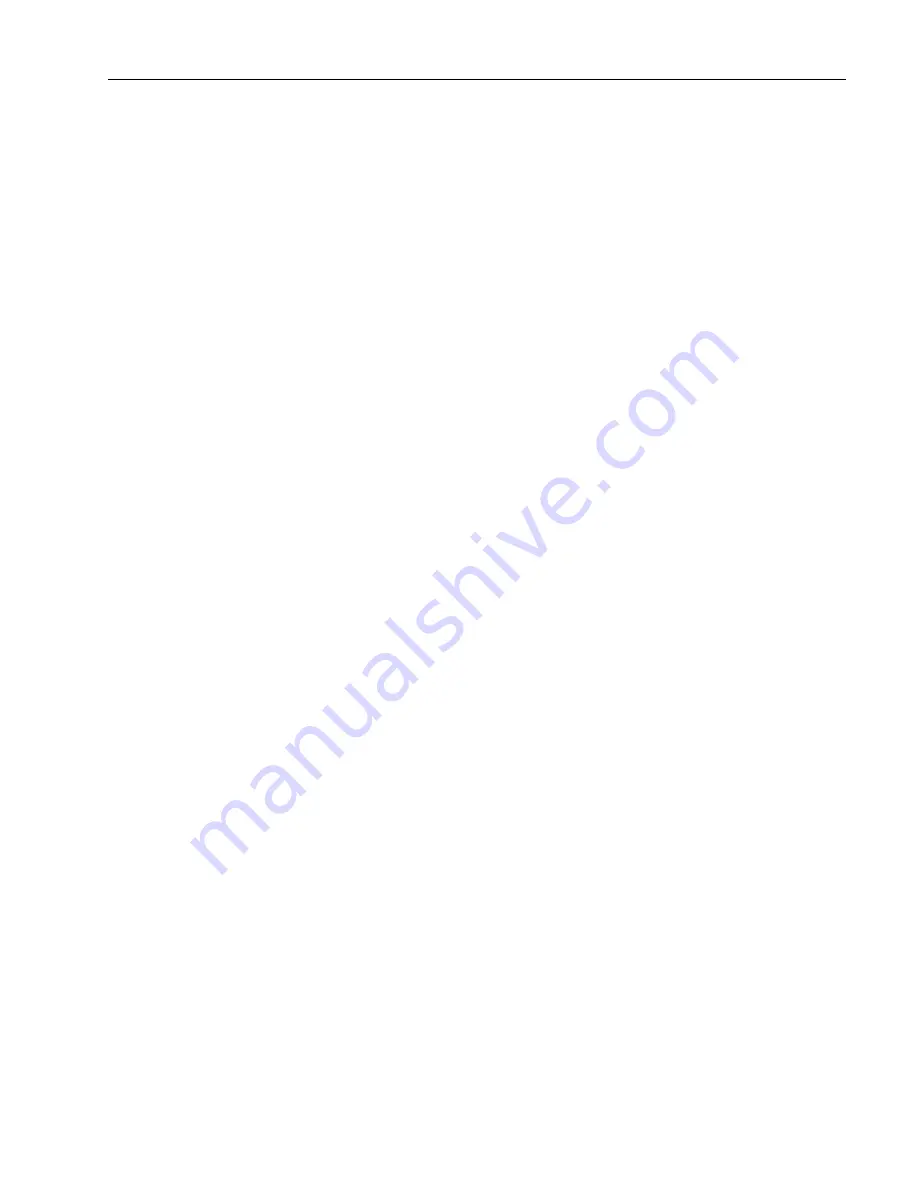
55
Barnstead|Thermolyne Corporation
warrants that if a product manufactured by
Barnstead|Thermolyne
and sold by it within the continental United States or Canada
proves to be defective in material or construction, it will provide you, without charge, for a
period of ninety (90) days, the labor, and a period of two (2) years, the parts, necessary to
remedy any such defect. Outside the continental United States and Canada, the warranty
provides, for two (2) years, the parts necessary to remedy any such defect. The warranty
period shall commence either six (6) months following the date the product is sold by
Barnstead|Thermolyne
or on the date it is purchased by the original retail consumer,
whichever date occurs first.
Use only HARVEY VAPO-STERIL solution in this sterilizer. DO NOT dilute, alter or
otherwise change VAPO-STERIL solution in any way. Do not use water in the
CHEMICLAVE sterilizer. Only VAPO-STERIL solution is proven an effective sterilant with
this sterilizer. Use of other solutions may cause mechanical damage to components of your
CHEMICLAVE sterilizer and may result in unsterile loads. Use of such solutions will void the
warranty.
All warranty inspections and repairs must be performed by and parts obtained from an
authorized
Barnstead|Thermolyne
dealer or
Barnstead|Thermolyne
(at its own
discretion). Heating elements, however, because of their susceptibility to overheating and
contamination, must be returned to our factory, and if, upon inspection, it is concluded that
failure is not due to excessive high temperature or contamination, warranty replacement will
be provided by
Barnstead|Thermolyne
. The name of the authorized
Barnstead|Thermolyne
dealer nearest you may be obtained by calling or writing to:
Alfa Medical
265 Post Ave Westbury, NY 11590
1-800-801-9934 Fax 516-977-7434
Barnstead|Thermolyne’s
sole obligation with respect to its product shall be to repair or
(at its own discretion) replace the product. Under no circumstances shall it be liable for
incidental or consequential damage.
THE WARRANTY STATED HEREIN IS THE SOLE WARRANTY APPLICABLE TO
Barnstead|Thermolyne
PRODUCTS.
Barnstead|Thermolyne
EXPRESSLY DISCLAIMS
ANY AND ALL OTHER WARRANTIES, EXPRESSED OR IMPLIED, INCLUDING
WARRANTIES OF MERCHANTABILITY OR FITNESS FOR USE.
Two Year Limited Warranty
Содержание Chemiclave EC5500
Страница 15: ...15 Figure 4 Metering Valve Function PRINCIPLES OF OPERATION ...
Страница 16: ...16 Figure 7 Pressurization PRINCIPLES OF OPERATION Figure 6 Ready Load Figure 5 Warm Up ...
Страница 17: ...17 Figure 8 EC5500 EC6000 Operation PRINCIPLES OF OPERATION ...
Страница 18: ...18 Figure 11 End Unload Figure 10 Purge Figure 9 Exposure PRINCIPLES OF OPERATION ...
Страница 20: ...20 Figure 13 Piping Schematic PRINCIPLES OF OPERATION ...
Страница 21: ...21 Figure 14 Cycle Phase Diagram PRINCIPLES OF OPERATION ...
Страница 22: ...22 Door Gasket Figure 15 Exploded View Top Cover and Door PRINCIPLES OF OPERATION ...
Страница 32: ...32 MAINTENANCE AND SERVICING Figure 17 Metering Valve need new drawing ...
Страница 39: ...39 MAINTENANCE AND SERVICING Figure 22 Power Supply Printed Circuit Board ...
Страница 56: ...56 ...