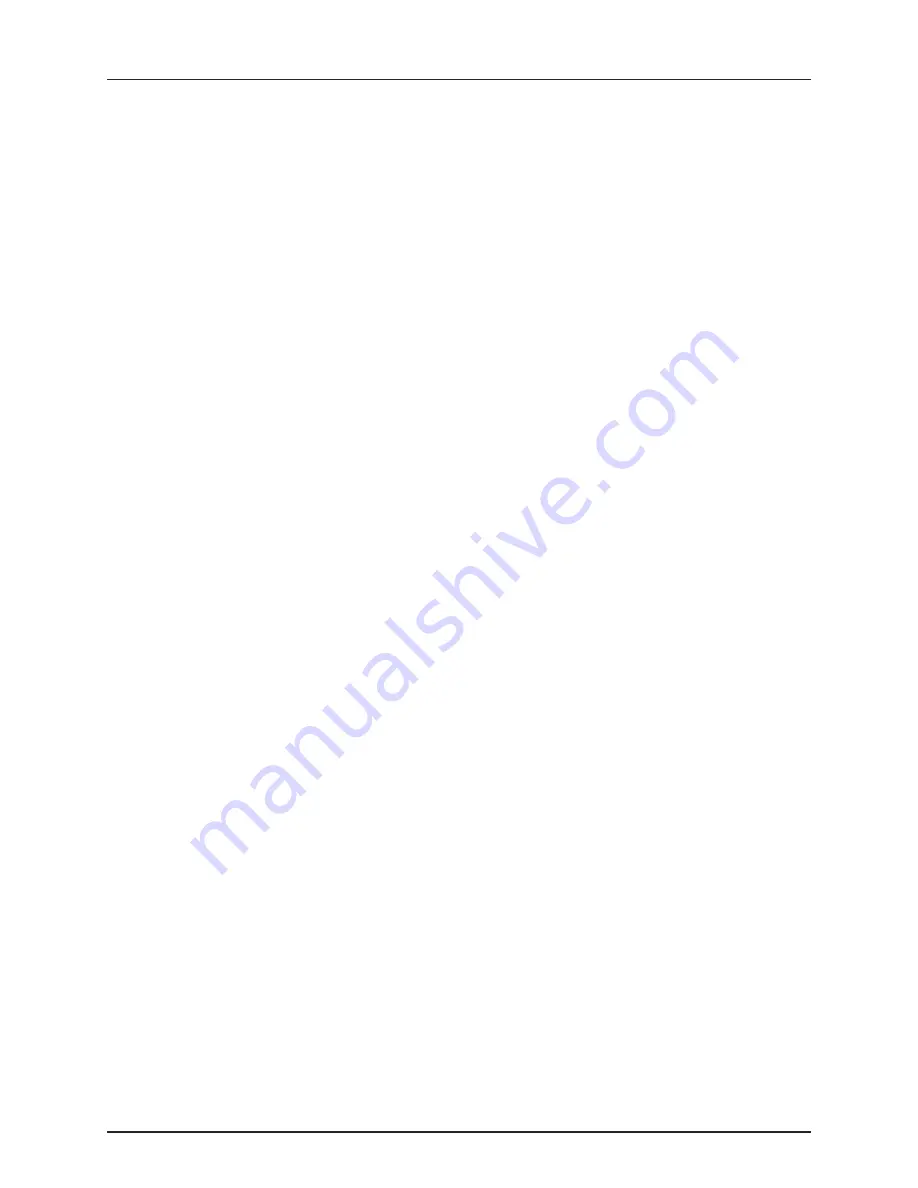
5 - Operation
92
D. Full Internal Cleaning (Soak Wash)
ATTENTION! This cleaning procedure is always used when one or more of these situations occur:
•
The next crop to be sprayed is at risk of being damaged by the chemical just used.
•
The sprayer is not going to be used right away for the same chemical or crop.
•
Before any repair or maintenance job is going to be carried out on the sprayer.
ATTENTION! Washing the sprayer between jobs with incompatible crops must be done according to instructions
from the chemical manufacturer. Use a commonly used cleaning agent. If your chemical prescribes a different
cleaning agent and/or another cleaning procedure, you must follow that.
Procedure for Washing with a Cleaning Agent
1.
Rinse the sprayer in the field (see the section “A. Full Internal Rinsing” on page 89).
2.
Drive to the filling location.
3.
Prepare sprayer for cleaning. Fill water in the main tank to 10% of its capacity. Fill the rinsing tank completely. This water
is later used for rinsing.
4.
Add the cleaning agent to the main tank by using the TurboFiller. Follow instructions on the label of the cleaning agent.
5.
Set suction SmartValve for “Main tank” and pressure SmartValve for “Spraying” (with all nozzles shut off by the main
ON/OFF switch on the grip). Set agitation valve for “Full agitation”.
6.
Engage and set the pump speed at approximately 560 rpm. Engage auxiliary pump (FlexCapacity pump).
7.
Allow the liquid to circulate the system for 3 minutes with the nozzles shut to clean the return lines from boom to tank.
8.
Close the agitation valve and turn the pressure SmartValve to “TurboFiller” for at least 10 seconds without activating
the TurboFiller in order to burst and flush the safety valve.
9.
Open the TurboFiller transfer valve and the deflector valve. Allow the liquid to circulate for 3 minutes.
10.
Close the lid and activate the container rinsing valve to clean the hopper inside.
11.
Shut all three valves on the TurboFiller again.
12.
Set the pressure SmartValve for “Spraying”.
13.
Allow the liquid in the main tank to circulate for minimum 3 minutes with the nozzles shut. This is done to clean the
return lines from boom to tank.
14.
Set the pressure SmartValve for “Internal tank rinsing”. Allow the liquid to circulate for 3 minutes.
15.
Spray out water with cleaning agent and chemical residue. Set the spray pressure at 45-75 psi (3-5 bar). Note that the
washing water still contains active chemical and choose an appropriate area to spray this out. Alternatively, the
washings can be dumped at the filling/washing location and retained in an appropriate receptacle (e.g. slurry tank or
similar) - see “Filling/Washing Location Requirements” on page 76. Spot contamination and accumulation must be
prevented. Continue to spray until all liquid has exited from the boom pipes and nozzles.
16.
Shut off all nozzles with the main ON/OFF switch.
17.
Rinse the sprayer again with clean water to rinse out all remaining cleaning agent. See “A. Full Internal Rinsing” on
page 89. This prevents the cleaning agent remaining in the fluid system from damaging the next spray chemical filled
into the main tank.
18.
Include rinsing of the TurboFiller in step 18. Operate all 3 valves during this process.
19.
Dismantle all filters (suction, pressure, in-line and nozzle filters) and clean the filter screens using clean water, detergent
and a brush.
±
WARNING! It is the responsibility of the sprayer operator or owner that the sprayer is cleaned sufficiently to prevent
contamination of the environment, crop damages and health and safety hazards to the operator and the public.
HARDI® cannot be held responsible for any damages or incidents related to insufficient cleaning.
ATTENTION! The rinsing nozzles cannot always guarantee a 100% cleaning of the tank. Clean manually with a high
pressure cleaner afterwards, especially if the next crop is sensitive to the chemical just sprayed!
Содержание COMMANDER 4500
Страница 2: ......
Страница 4: ......
Страница 10: ...Table of Contents 8...
Страница 12: ...1 Welcome 10...
Страница 48: ...3 Description 46...
Страница 96: ...5 Operation 94...
Страница 99: ...6 Maintenance 97 Lubrication and Oiling Plan Boom Width 80 100 10 10 10 C 500 C 50 C 50 10...
Страница 100: ...6 Maintenance 98 Lubrication and Oiling Plan Boom Width 120 10 C 500 C 50 10...
Страница 129: ...6 Maintenance 127 At the same time adjust the two stop bolts to align the boom sections...
Страница 142: ...6 Maintenance 140...
Страница 162: ...8 Technical Specifications 160...
Страница 168: ...Index 166...
Страница 169: ......