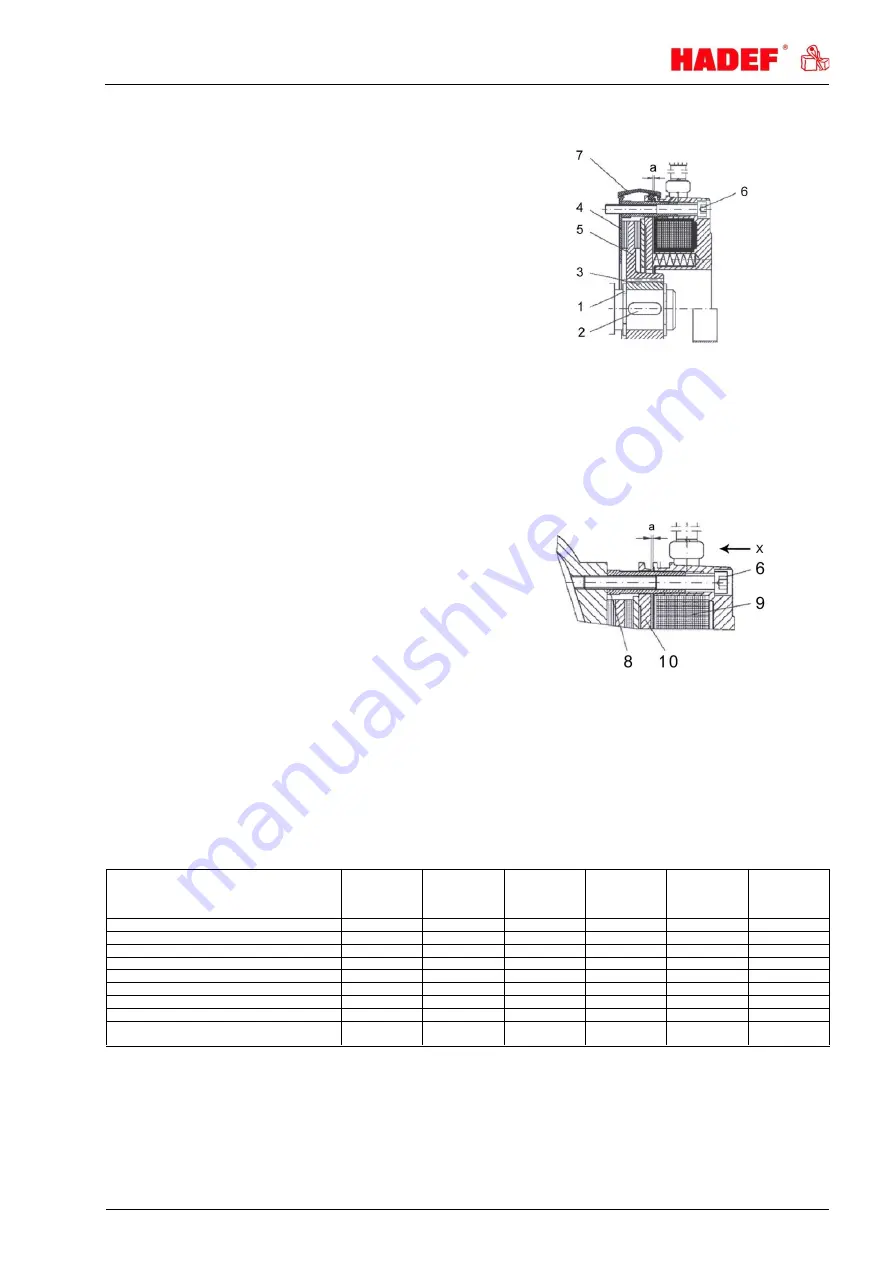
5.52.693.00.01.00
13
12.3.1
Assembling the brake
1 Insert the retaining ring (1) into the shaft slot.
2 Insert the feather key (2) into the motor shaft.
3 Fix hub (3) with retaining ring (1).
4 Assemble the friction plate (4) if existent.
5 Push the rotor (5) onto the hub (3).
6 Lock the magnet body with the 3 fastening
screws (6).
7
Set air gap “a” (refer to “adjusting the air gap”)
8 Assemble the dust-protection ring (7) if
existent.
9Electric connection
Illustration 9
12.3.2
Disassembly of the brake
Disassembly is performed in reverse order to the assembly.
12.3.3
Adjusting the air gap
View "X" on the brake.
1 Loosen the locking screws (6) by half a turn.
2 Turn the cap screws (8) into the magnetic body
(9) anti-clockwise.
3 By turning the locking screws (6) clockwise,
move the magnetic body (9) towards the
anchor plate (10) using a feeler gauge until
nominal air gap “a” is reached (see table).
4 Unscrew the cap screws (8) from the magnetic
body clockwise.
5 Tighten the locking screws (6).
6 Check the air gap again and re-adjust if
necessary.
Illustration 10
13
Inspection
13.1
Periodic checks
Independently from the regulations of the individual countries, lifting devices must be checked at least yearly
by a qualified person or licensed qualified person regarding its functional safety.
at
commissioning
daily
checks
1st maintenance
after
3 months
Inspection
Maintenance
every
3 months
Inspection
Maintenance
every
12 months
check screw connections
X
X
check the bearings
X
check the trolley wheels
X
check lubrication of the driving pinion
X
X
buffers - check correct position and wear
X
X
electric motor* - check the brake lining
X
electric motor* - check the brake
X
X
pneumatic motor*
X
X
X
Have the equipment checked by an expert
(periodic inspection)
X
*as far as applicable
14
Service
14.1
Electric motor
For the motor it is sufficient to keep the cooling airways clean and monitor the roller bearing and its
lubrication status.
A high temperature fat must be used if the roller bearing is replaced.