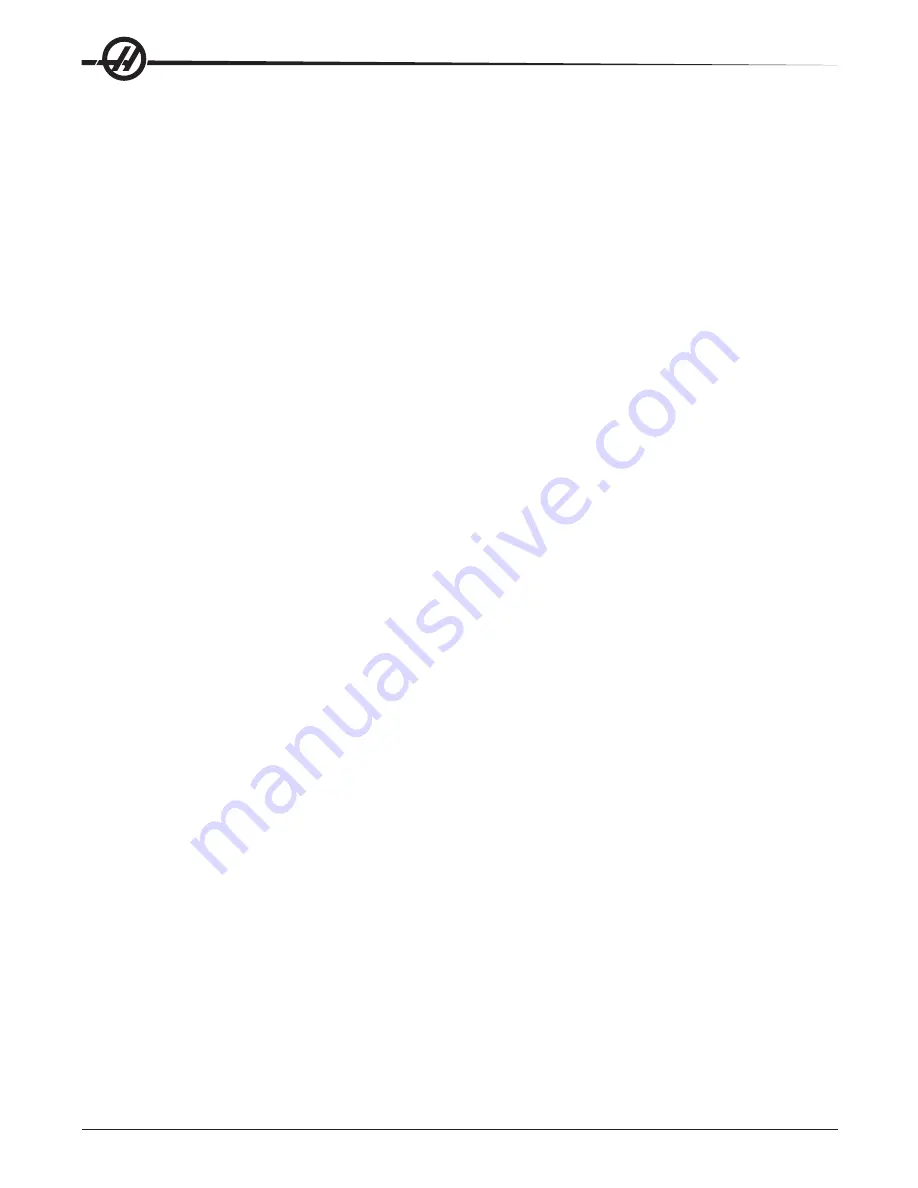
14
96-5047 rev L June 2005
The RS-232 interface sends and receives seven data bits, even parity, and two stop bits. The data rate can
be between 110 and 19200 bits per second. When using RS-232, it is important to make sure that Parameters
26 (RS-232 Speed) and 33 (X-on/X-off Enable) are set to the same value in the controller and PC. Parameter 12
must be set to 3 in order to coordinate mill and controller motion. This will prevent Aux. axis position mismatch
alarm (355) when in handle jog mode.
If Parameter 33 is set to on, the controller uses X-on and X-off codes to control reception, so be sure your
computer is able to process these. It also drops CTS (pin 5) at the same time it sends X-off and restores CTS
when is sends X-on. The RTS line (pin 4) can be used to start/stop transmission by the controller or the X-on/X-
off codes can be used. The DSR line (pin 6) is activated at power-on of the controller and the DTR line (pin 20
from the PC) is not used. If Parameter 33 is 0, the CTS line can still be used to synchronize output.
When more than one HAAS controller is daisy-chained, data sent from the PC goes to all of the controllers at
the same time. That is why an axis selection code (Parameter 21) is required. Data sent back to the PC from
the controllers is OR’ed together so that, if more than one box is transmitting, the data will be garbled. Be-
cause of this, the axis selection code must be unique for each controller.
The serial interface may be used in either a remote command mode or as just an Upload/Download path.
RS-232 Remote Command Mode
Parameter 21 must be non-zero for the remote command mode to operate, as the controller looks for an axis
select code defined by this parameter. The controller must also be in RUN mode to respond to the interface.
Since the controller powers-on in RUN mode, unattended remote operation is possible.
Commands are sent to the controller in ASCII code and terminated by a carriage return (CR). All commands,
except for the B command, must be preceded by the axis select code (U,V,W,X,Y,Z). The B command does
not require the select code, as it is used to activate all axes simultaneously. The ASCII codes used to com-
mand the controller are shown below.
RS-232 Commands
The following are the RS-232 commands, where X is the selected axis:
xSnn.nn
Specify step size or absolute position.
xFnn.nn
Specify feed rate in units/second.
xGnn
Specify G code.
xLnnn
Specify loop count.
xP
Specify servo status or position.
(This command causes the addressed controller to respond with the servo position if
normal operation is possible or otherwise with the servo status.)
xB
Begin programmed step on X-axis.
B
Begin programmed step on all axes at once.
xH
Return to HOME position or use home offset.
xC
Clear servo position to zero and establish zero.
xO
Turn servo on.
xE
Turn servo off.
Содержание HRT 160
Страница 9: ...8 96 5047 rev L June 2005 HRT210SHS MACHINE DIMENSIONS ...
Страница 55: ...54 96 5047 rev L June 2005 9 HRT ASSEMBLY DRAWINGS ...
Страница 58: ...57 96 5047 rev L June 2005 ...
Страница 59: ...58 96 5047 rev L June 2005 ...
Страница 61: ...60 96 5047 rev L June 2005 ...
Страница 62: ...61 96 5047 rev L June 2005 ...
Страница 63: ...62 96 5047 rev L June 2005 ...
Страница 64: ...63 96 5047 rev L June 2005 ...