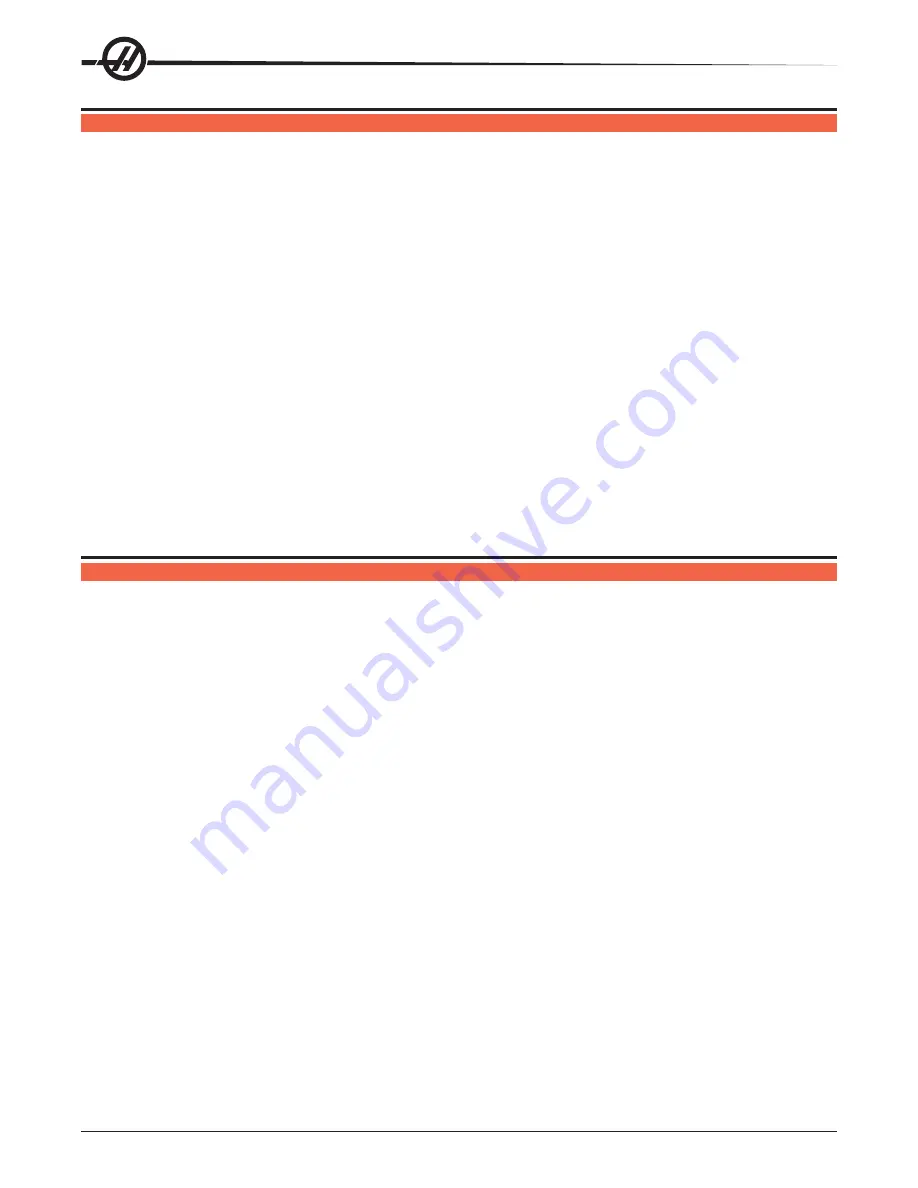
42
96-5047 rev L June 2005
6.2 G
EAR
C
OMPENSATION
The control has the ability to store a compensation table to correct for small errors in the worm gear. The gear
compensation tables are part of the parameters. While parameters are displayed, press the right arrow button
to select the gear compensation tables. There is a separate plus direction table from the minus direction table.
Use the right arrow button to display the plus or minus table. The gear compensation data is displayed as:
gP Pnnn cc
for plus table
G- Pnnn cc
for minus table
The nnn value is the machine position in degrees and the cc is the compensation value in encoder steps.
There is a table entry every two degrees starting at 001 and going to 359. If your control has non-zero values in
the gear compensation tables, it is recommended that you do not change them.
When the gear compensation tables are displayed, the up and down arrow button will select the next two
degree (2
o
) entry and the minus (-) and numeric buttons will enter a new value. In addition to this, the JOG
button may be used to adjust the compensation value. If the servo is on when changes are made, and the table
is at the position corresponding to the entry changed, the servo motor will move by the adjustment amount.
This is valuable in that the JOG button can be used to move the motor to a desired position.
Clearing of parameters will set all of the gear compensation tables to zero. To exit the gear compensation
display, press the MODE button; this returns the control to RUN mode.
When a table is using gear compensation, the values in Parameter 11 must be set to "0".
6.3 P
ARAMETER
L
IST
The following is a list of the programmable parameters:
If the brushless software ranges are different, they will be shown in parentheses.
Parameter 1: CNC Interface Relay Control, range 0 to 2
0:
relay active during indexer motion
1:
relay pulsed for ¼ second at end of motion
2:
no relay action
Parameter 2: CNC Interface Relay Polarity & Aux. Relay Enable, range 0 to 3
0:
normally open
+1: normally closed
+2: optional relay number 2 pulsed at end of program
Parameter 3: Servo Loop Proportional Gain, range 0 to 255 PROTECTED!
Servo loop proportional gain increases current in proportion to the proximity to the target position. The
farther from the target, the greater the current up to the maximum value in parameter 40. A mechanical
analogy is a spring that will oscillate past the target unless dampened by the Derivative gain.
Parameter 4: Servo Loop Derivative Gain, range 0 to 255 (0 to 99999) PROTECTED!
Servo loop derivative gain resists motion effectively braking oscillations. This parameter is increased in
proportion to the p gain.
Parameter 5: Double Remote Trigger Option, range 0 to 1
When this parameter is set to 1, the remote START must be triggered twice to activate the control. When
it is zero, each activation of the remote input will trigger a step.
Содержание HRT 160
Страница 9: ...8 96 5047 rev L June 2005 HRT210SHS MACHINE DIMENSIONS ...
Страница 55: ...54 96 5047 rev L June 2005 9 HRT ASSEMBLY DRAWINGS ...
Страница 58: ...57 96 5047 rev L June 2005 ...
Страница 59: ...58 96 5047 rev L June 2005 ...
Страница 61: ...60 96 5047 rev L June 2005 ...
Страница 62: ...61 96 5047 rev L June 2005 ...
Страница 63: ...62 96 5047 rev L June 2005 ...
Страница 64: ...63 96 5047 rev L June 2005 ...