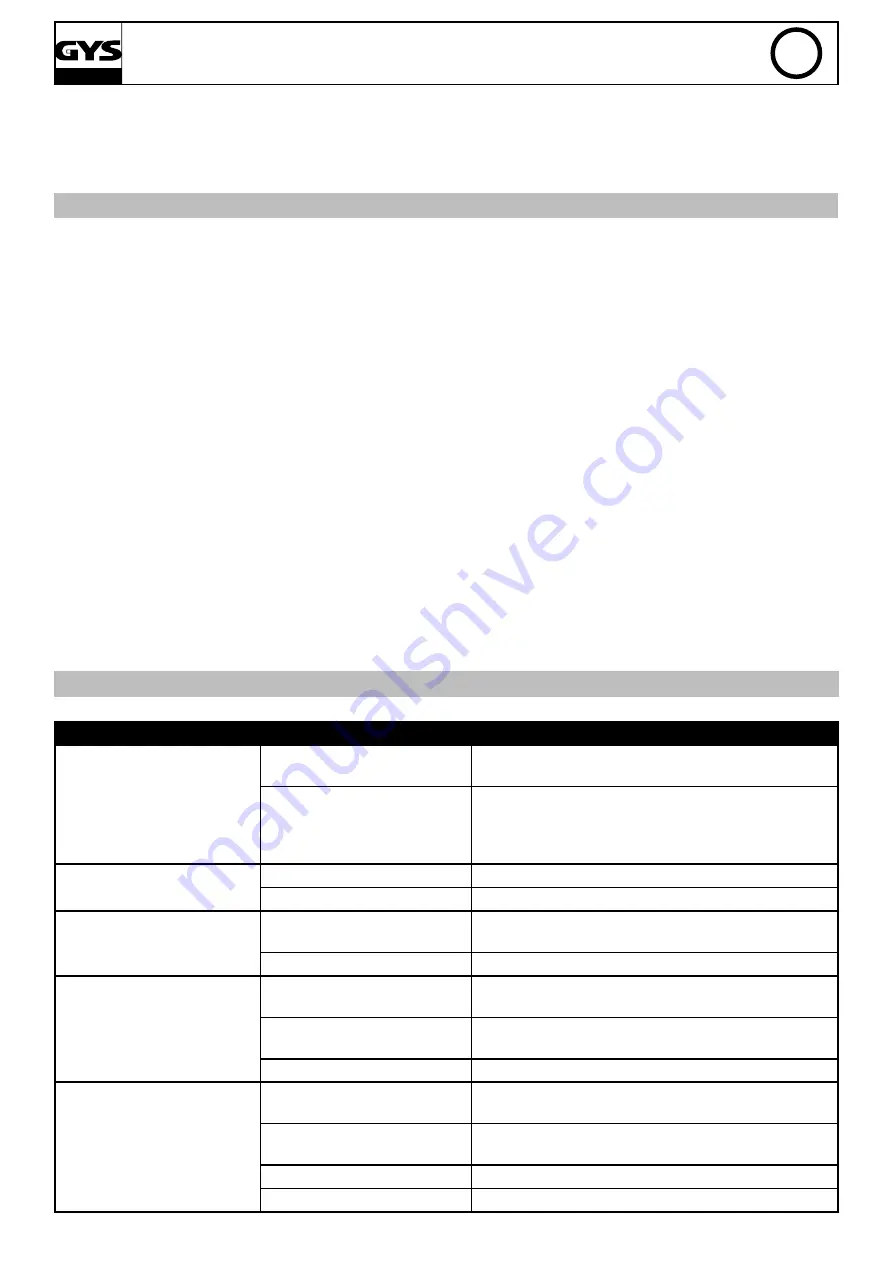
14
CARMIG
EN
• Welding installation assessment
Besides the area assessment, the assessment of arc welding systems can be used to identify and resolve cases of dis-
turbances. The assessment of emissions must include in situ measurements as specified in Article 10 of CISPR 11: 2009.
In situ measurements can also be used to confirm the effectiveness of mitigation measures.
RECOMMENDATIONS METHODS TO REDUCE ELECTROMAGNETIC EMISSIONS
• Electrical grid :
You should connect the welding equipment to the mains according to the manufacturer’s recom
-
mendations. If interferences occur, it may be necessary to take additional preventive measures such as the filtering
of the power supply network. Consideration should be given to shielding the power supply cable in a metal conduit.
It is necessary to ensure the shielding’s electrical continuity along the cable’s entire length. The shielding should be
connected to the welding current’s source to ensure good electrical contact between the conductor and the casing of
the welding current source.
•Maintenance of the arc welding equipment :
The machine should be connected to the electrical grid according to
the manufacturer’s recommendations. If interferences occur, it may be necessary to take additional preventive measures
such as the filtering of the power supply network. Consideration should be given to shielding the power supply cable in a
metal conduit. It is necessary to ensure the shielding’s electrical continuity along the cable’s entire length. The shielding
should be connected to the welding current’s source to ensure good electrical contact between the conduct and the
casing of the welding current source.
• Welding cables:
The cables should be as short as possible. Regroup them and leave them on the ground if possible.
d. Electrical bonding : consideration shoud be given to bonding all metal objects in the surrounding area. However, metal
objects connected to the workpiece increase the risk of electric shock if the operator touches both these metal elements
and the electrode. It is necessary to insulate the operator from metal objects.
• Earthing of the welding piece :
This can reduce disruption problems. It can be done directly or via an appropriate
capacitor. This choice is made according to national regulations.
• Protection and Shielding:
Protection and selective shielding of the cables and other equipment in the surrounding
area can limit disruption problems.
SYMPTOMS, REASONS, SOLUTIONS
SYMPTOMS
POSSIBLE REASONS
SOLUTIONS
The welding wire speed is
not constant.
Cracklings blocking up the
opening.
Clean out the contact batch or change it and replace
the anti-adherence product.
The wire skids in the rollers.
- Control the roller pressure or replace it.
- Wire diameter non-consistent with roller
- Covering wire guide in the torch not consistent with
wire.
The unwinding motor
doesn’t operate.
Reel or roller brake too tight.
Release the brake and rollers.
Electrical supply problem.
Check that the running button is on the position on.
Bad wire unwinding.
Covering wire guide dirty or
damaged.
Clean or replace
Reel brake too tight
Release the brake
No welding current
Bad connection to the mains
supply.
Check the branch connection and ensure it is fed by
3 phases.
Bad earth connection.
Control the earth cable (connection and clamp condi-
tion).
Power contactor inoperative.
Control the torch trigger.
The WIRE rubs down after
the rollers.
Covering WIRE guide
crushed.
Check the covering and torch body.
Locking of the wire in the
torch
Clean or replace.
No capillary tube.
Check the presence of capillary tube.
Wire speed too fast
Reduce the wire speed