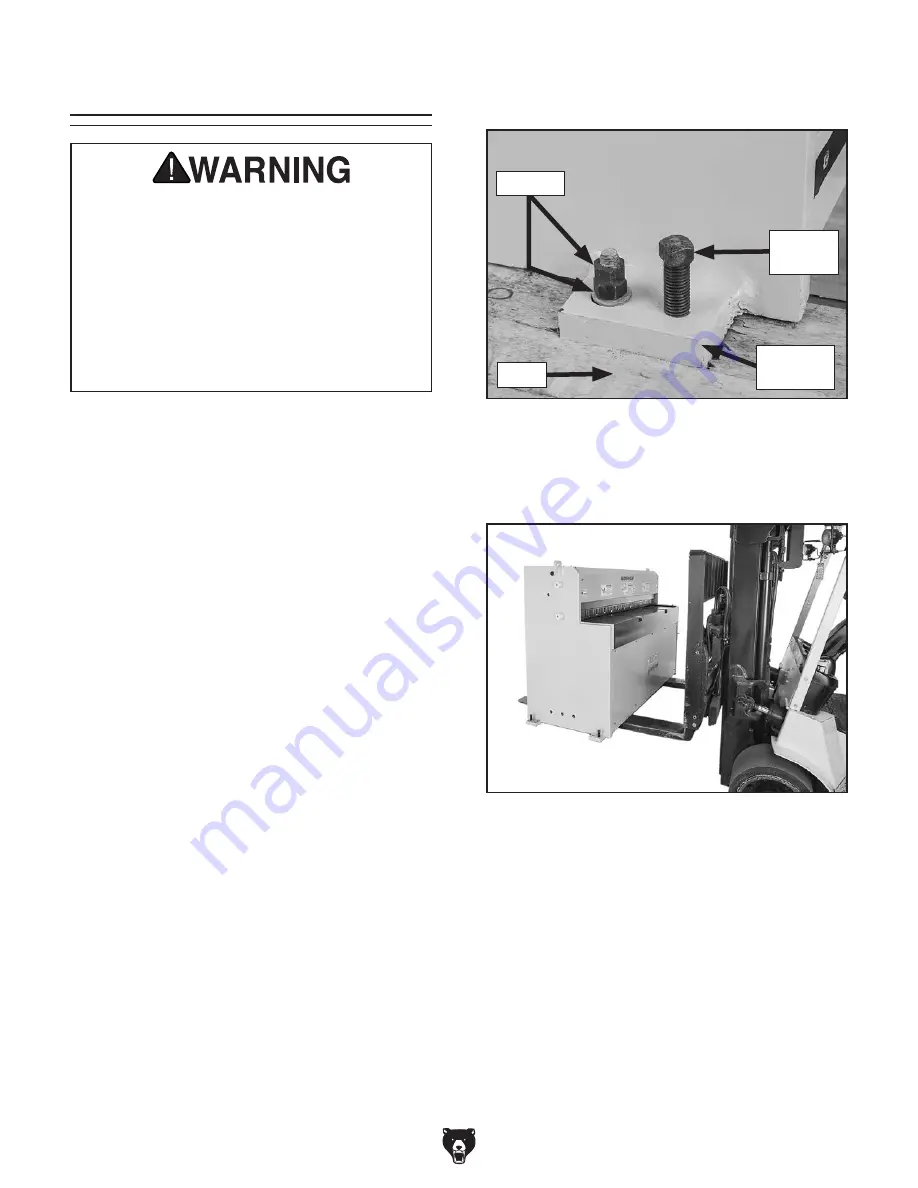
-18-
Model G0845P (Mfd. Since 01/18)
DO NOT attempt to lift or move machine without
using proper lifting equipment (such as forklift or
crane) and assistance from other people. Each
piece of lifting equipment must be rated for
at
least 4000 lbs. to support dynamic loads that
may be applied while lifting.
Review the
Power Supply section beginning on
Page 10, then prepare a permanent location for
the machine.
Note: Place the G0845P on a level concrete floor.
Position the machine to provide clear access for
the loading and unloading areas (refer to
Site
Considerations on Page 17).
4. Lift machine enough to just clear shipping
pallet.
5. Move machine to prepared location.
Figure 13. Lifting the Model G0845P.
Lifting & Placing
Items Needed
Qty
Forklift (Rated For At Least 4000 lbs.) .............. 1
Wrench or Socket 18mm ................................... 1
Another Person .................................................. 1
To move machine:
1. Remove shipping crate and accessories box.
3. Carefully slide forklift forks under machine
base (see
Figure 13).
Figure 12. Remove hex nuts and flat washers
securing machine to pallet.
Do Not
Remove
Mounting
Foot
Pallet
Remove
This is an extremely heavy machine! Serious
personal injury or death may occur if safe
lifting and moving methods are not fol-
lowed. To be safe, you will need assistance
and power equipment when moving the
shipping crate and removing the machine
from the crate. Seek assistance from a
professional rigger if you are unsure about
your abilities or maximum load ratings of
your lifting equipment.
2. Remove (2) hex nuts and (1) flat washer on
each mounting foot (see
Figure 12).
Содержание G0845P
Страница 68: ......