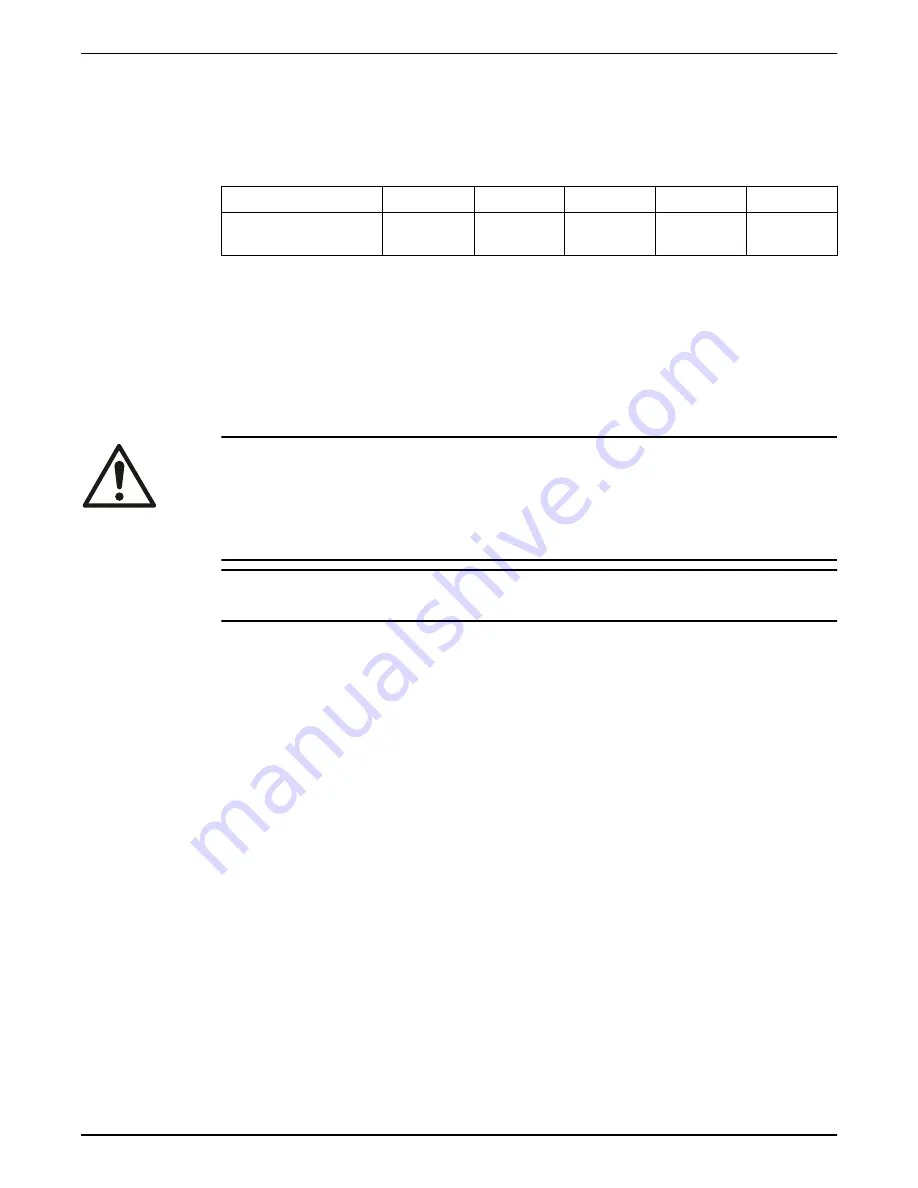
3 Product Description
3.1 Products included
Pump model
Standard Ex-proof MSHA
Drainage Sludge
Sandy INOX
8120.280
X
X
3.2 Pump design
The pump is submersible, and driven by an electric motor.
Intended use
The product is intended for moving waste water, sludge, raw and clean water.
Always follow the limits given in
question regarding the intended use of the equipment, then contact a sales or
authorized service representative before proceeding.
DANGER: Explosion/Fire Hazard
Special rules apply to installations in explosive or flammable atmospheres. Do
not install the product or any auxiliary equipment in an explosive zone unless it
is rated explosion-proof or intrinsically-safe. If the product is rated explosion-
proof or intrinsically-safe, then see the specific explosion-proof information in
the safety chapter before taking any further actions.
NOTICE:
Do NOT use the unit in highly corrosive liquids.
For information about pH, see
on page 36.
Particle size
The pump can handle liquid containing particles that correspond to the pump
housing inlet.
Pressure class
N
Medium head
Impeller type
Sludge
3.3 Monitoring equipment
The following applies to the monitoring equipment of the pump:
• The stator incorporates thermal contacts connected in series that activate the
alarm at overtemperature.
• The thermal contacts open at 130°C (266°F) and close at 100°C (212°F).
3.4 The data plate
Introduction
The data plate is a metal label located on the main body of the pump. The data
plate lists key product specifications.
3 Product Description
10
8120.280 Sandy Inox Installation, Operation, and Maintenance Manual
Содержание 8120.280 Sandy Inox
Страница 1: ...www grindex com Installation Operation and Maintenance Manual 8120 280 Sandy Inox ...
Страница 2: ......
Страница 41: ......
Страница 42: ......
Страница 43: ......