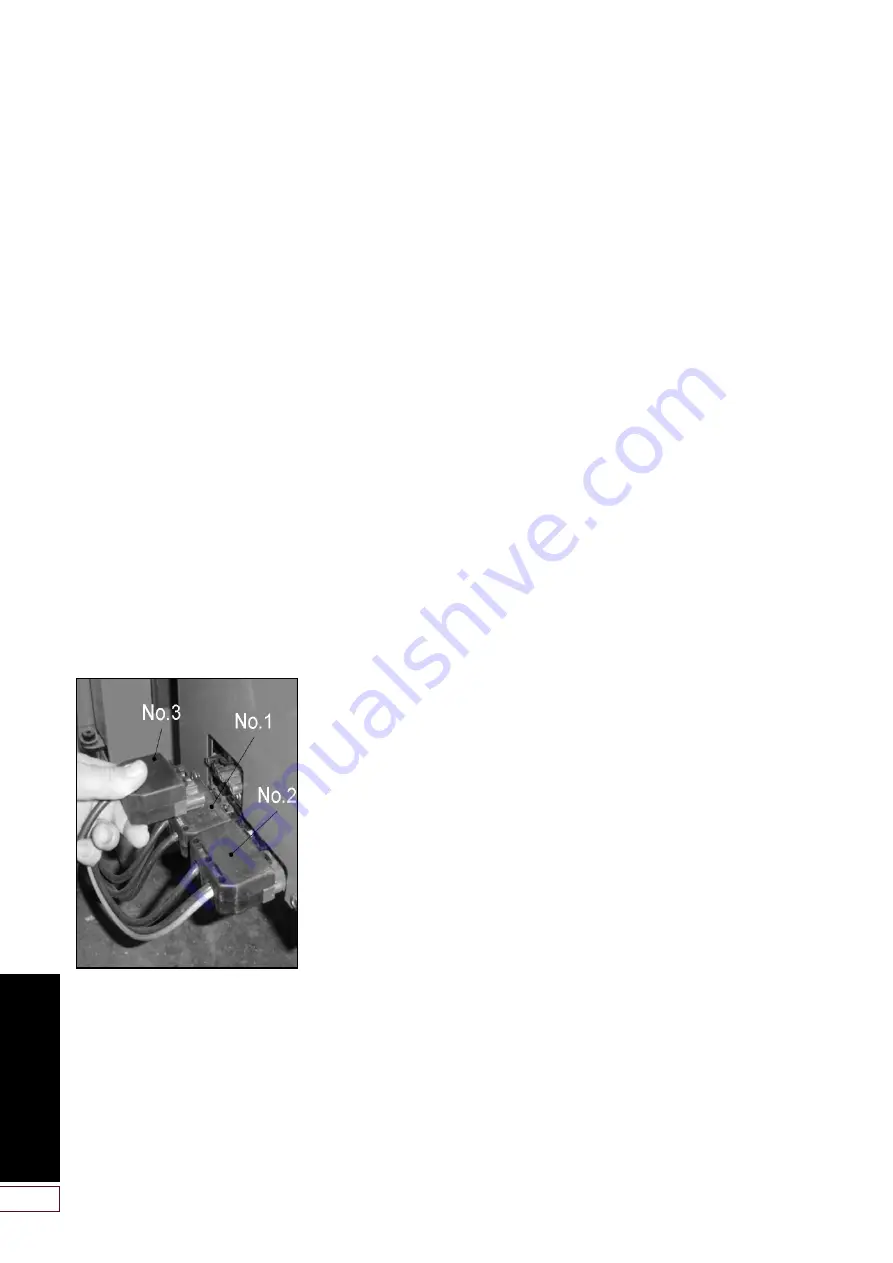
right or left, as required.
•
Re-fit the three screws and
washers. Tighten them down
evenly to secure the pellet feed
tube to the burner.
•
Fit the pellet feed tube thermostat
lead on to the thermostat
terminals.
•
Fit the pellet feed tube.
With the gasket correctly located, re-fit
the burner to the combustion chamber
door:
•
Carefully insert the burner brazier
through the opening and locate
the holes in the burner flange onto
the M8 studs (on either side of the
burner).
•
Secure the burner to the door
with the two M8 nuts previously
removed.
•
Re-connect the plugs to their
corresponding sockets on the left
side of the burner.
•
Ensure that each plug is fully
pushed home until the small catch
clicks into place. Refer to Figure
4.8.
4.12 Pellet Hoppers
4.12.1 Single Boiler Installation
Position the pellet hopper on the same
firm level surface as the boiler, on
either the left-hand or right-hand side of
the boiler (depending on hopper type
used), with the top access door facing
forwards. Refer to Figure 2-1 or 2-2 as
required, for clearance dimensions and
position.
36
Figure 4-8:
Auger plug connection
4.12.2 Double boiler installation
Position the pellet hopper on the same
firm level surface as, and in between,
the two boilers, with the top access
door facing forwards. Refer to Figure
2-3 for clearance dimensions and
position.
Failure to adhere to these
measurements can cause blockage of
the pellets in the pellet delivery hose
or can prevent access for servicing at
a later date. The hopper is supplied
with castors which allows the hopper
be moved during servicing. Once in
the correct position, engage the brakes
on the front castors to maintain this
position.
4.13 Pellet Feed Auger
4.13.1 Single Boiler Hoppers
The pellet feed auger is supplied
packed with the hopper but not factory-
fitted to it.
To fit, unpack the hopper and auger.
Remove the M5 screw fitted below
the auger opening on the front of the
hopper. Fit the end of the auger into
opening in the front of the hopper as far
as it will go and secure by fitting the M5
screw through the auger fixing flange
and tighten. See Figure 4-5.
4.13.2 Double Boiler Hoppers
Both augers on the ‘double boiler’
Intermediate hoppers are supplied
factory-fitted to the hopper.
To connect the hopper to the boiler,
fit one end of the pellet delivery hose
onto the pellet feed auger outlet and
the other end onto the pellet feed tube.
The pellet delivery hose may need to
be cut if too long. A sachet of lubricant
is supplied in the accessories carton;
apply the lubricant to the joint to ensure
the pellet delivery hose is easily fitted.
Ensure the pellet delivery hose is not
kinked in any way.
Fit the 6-way plug (No.3), from the
pellet feed auger motor, into the
corresponding 6-way socket on the left
side of the burner. Ensure that the plug
is fully pushed home until the small
catch it clicks into place. See Figure
4-6. Refer to Section 8.3 for all boiler
plug connections.
4.14 Before you Commission
To avoid the danger of dirt and foreign
matter entering the boiler the complete
heating system should be thoroughly
flushed out – both before the boiler is
connected and then again after the
system has been heated and is still hot.
This is especially important where
the boiler is to be installed on an old
system.
For optimum performance after
installation, the boiler and the
associated heating system must
be flushed in accordance with the
guidelines given in BS 7593:2006
‘Treatment of water in domestic hot
water central heating systems’. This
must involve the use of a proprietary
cleaner, such as Betz Dearborn’s
Sentinel x300 or x400, or Fernox
Restorer. Full instructions are supplied
with the products but for more details
visit either www.sentinel-solutions.net
for Betz Dearborn products or www.
fernox.com for Fernox products.
After flushing the system, an inhibitor
such as Sentinel X100 or Fernox MB-1
should be used in accordance with the
guidelines given in BS 7593:2006 for
long term protection against corrosion
and scale.
Grant Engineering (UK) Limited
strongly recommends that a Grant
Mag One in-line magnetic filter/s (or
equivalent*) is fitted in the heating
system pipework. This should be
installed and regularly serviced
in accordance with the filter
manufacturer’s instructions.
* As measured by gauss. The Mag-
One magnetic filter has a gauss
measurement of 12000.
4.15 Completion
Please ensure that the Grant Spira
Commissioning form (supplied with the
boiler) is completed in full and that it is
signed by the householder/user.
Leave the white copy with the user,
retain the pink copy for your own
records, and return the yellow copy to
Grant UK. Refer to Section 10-12.
Ensure that these Instructions are
handed over to the householder.
Содержание Spira 5-18
Страница 19: ...19 This page is intentionally left blank...
Страница 95: ...95 13 Spare Parts 13 1 Boiler Figure 13 1 Boiler components exploded view...
Страница 106: ...106 Notes...
Страница 107: ...107 This page is intentionally left blank...