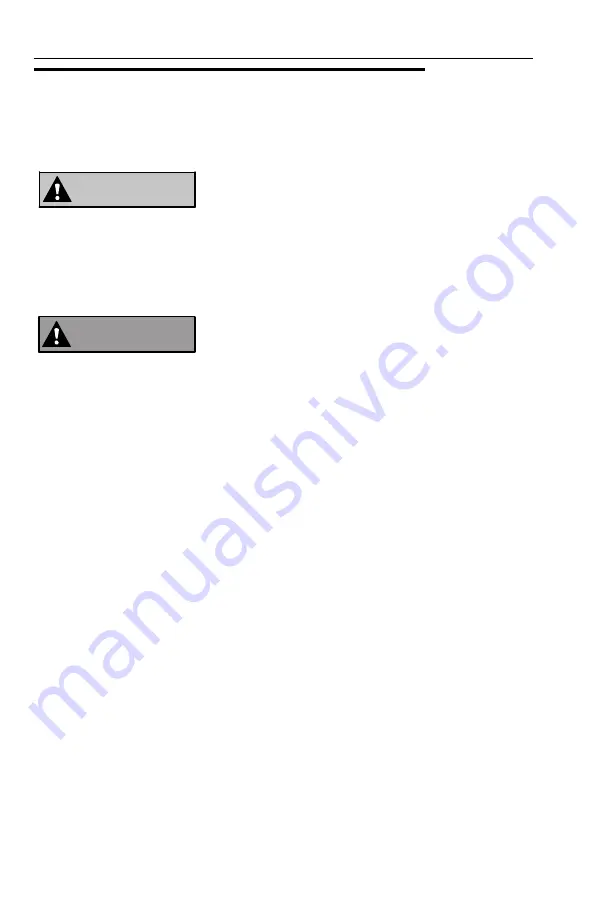
Section 3 - Operation
3-4
80804002
3.3
TRAVEL MODE BRAKE SYSTEM
The air brake system includes service brakes, emergency brakes, parking brakes
and digging brakes.
NEW BRAKES.
New brakes need increased stopping
distance. Brake capability will improve after several
stops. Failure to stop may result in death or serious
injury.
BRAKING HAZARDS.
Always wear seat belt to avoid
being thrown from driver’s seat during braking
emergency.
Do not “fan” the brake valve pedal. A long series of
rapid brake applications could reduce system pressure
to a point where effective service braking will be lost
until brake pressure is restored.
Do not operate undercarriage or upperstructure while
low air indicator is illuminated. If light comes on while
undercarriage is moving, stop in a safe area as soon
as possible. If undercarriage will not maintain the
proper brake pressure, notify maintenance personnel
immediately for repair of condition.
CAUTION
OW0031
WARNING
OW0021
Содержание XL3100IV
Страница 6: ...Read This First d 80804002 NOTES...
Страница 24: ...Section 1 General Safety Practices 1 14 80804002 NOTES...
Страница 33: ...Section 2 Pre Operation and Controls 2 9 80804002 NOTES...
Страница 53: ...Section 2 Pre Operation and Controls 2 29 80804002 NOTES...
Страница 61: ...Section 2 Pre Operation and Controls 2 37 80804002 NOTES...
Страница 79: ...Section 3 Operation 3 9 80804002 NOTES...
Страница 108: ...Section 3 Operation 3 38 80804002 This Page Intentionally Left Blank...
Страница 152: ...Section 5 Lubrication Maintenance 5 38 80804002 NOTES...
Страница 164: ...Section 7 Specifications 7 10 80804002 This Page Intentionally Left Blank...