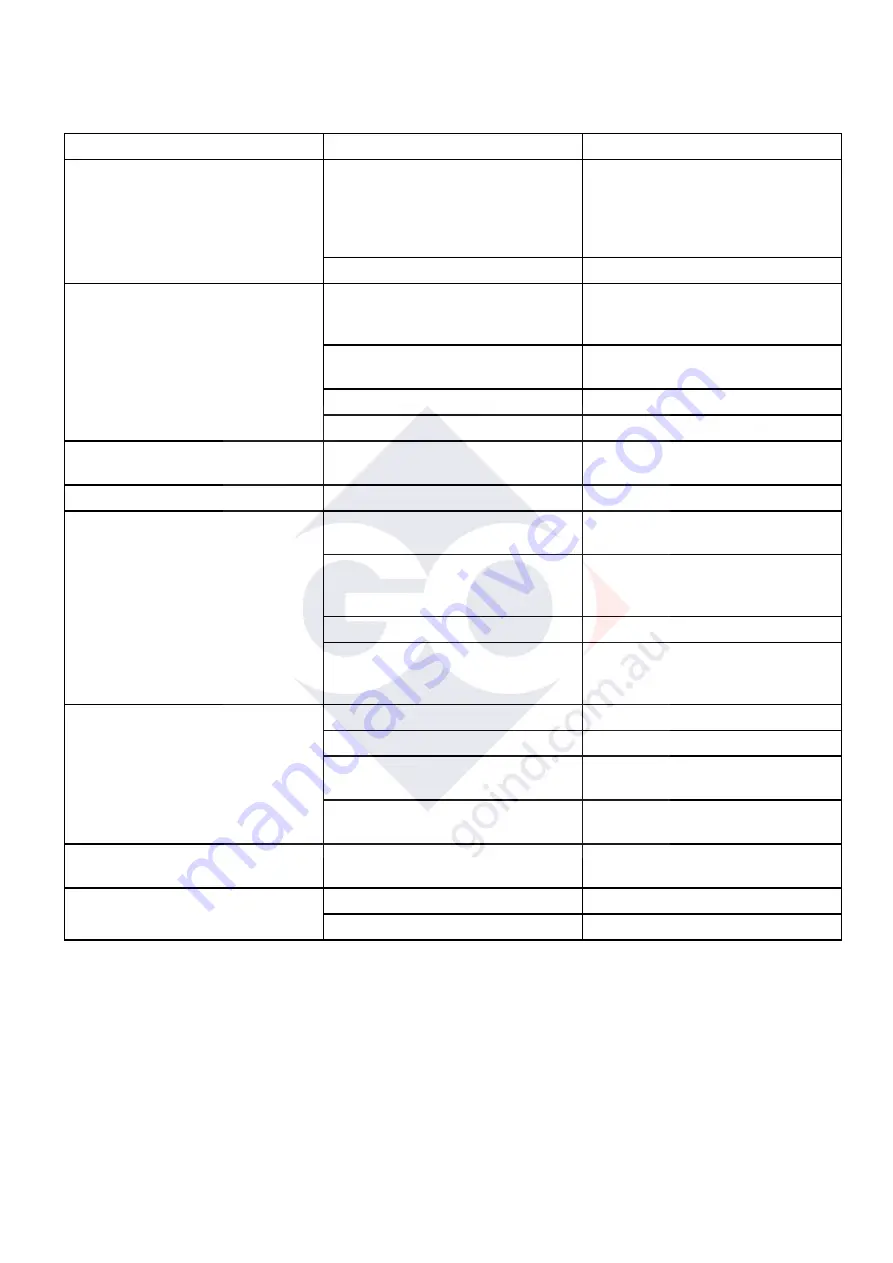
Gun Operation Troubleshooting
Problem
Cause
Solution
Atomizing air pressure too high.
Close atomizing air valve part way,
or decrease air pressure as low
as possible; minimum 45 psi (0.32
MPa, 3.2 bar) needed at gun for full
voltage.
Excessive spray fog.
Fluid too thin.
Increase viscosity.
Atomizing air pressure too low.
Open atomizing air valve more or
increase gun air inlet pressure; use
lowest air pressure necessary.
Spray tip is too large.
Use smaller tip. See
Spray Tip Selection Chart, page 71
Poorly mixed or filtered fluid.
Remix or refilter fluid.
“Orange Peel” finish.
Fluid too thick.
Reduce viscosity.
Fluid leaks from the fluid packing
area.
Worn fluid needle packings or rod.
See
Fluid Needle Replacement, page 51
.
Air leaks from the front of the gun.
Air valve is not seating properly.
See
Worn or damaged fluid needle ball.
See
Fluid Needle Replacement, page 51
.
Worn fluid seat housing.
See
Seat Housing Replacement, page
Loose spray tip.
Tighten retaining ring.
Fluid leakage from the front of the
gun.
Damaged tip seal.
See
Seat Housing Replacement, page
Low fluid supply.
Add fluid if necessary.
Damaged spray tip.
Replace.
Dirty or clogged spray tip.
Clean.
See
Gun does not spray.
Damaged fluid needle.
See
Fluid Needle Replacement, page 51
.
Dirty air cap.
Damaged or plugged air cap.
Clean air cap. See
Poor grounding.
See
Excessive paint wrap back to
operator.
Incorrect distance from gun to part.
Should be 8–12 in. (200–300 mm).
44
3A2497C