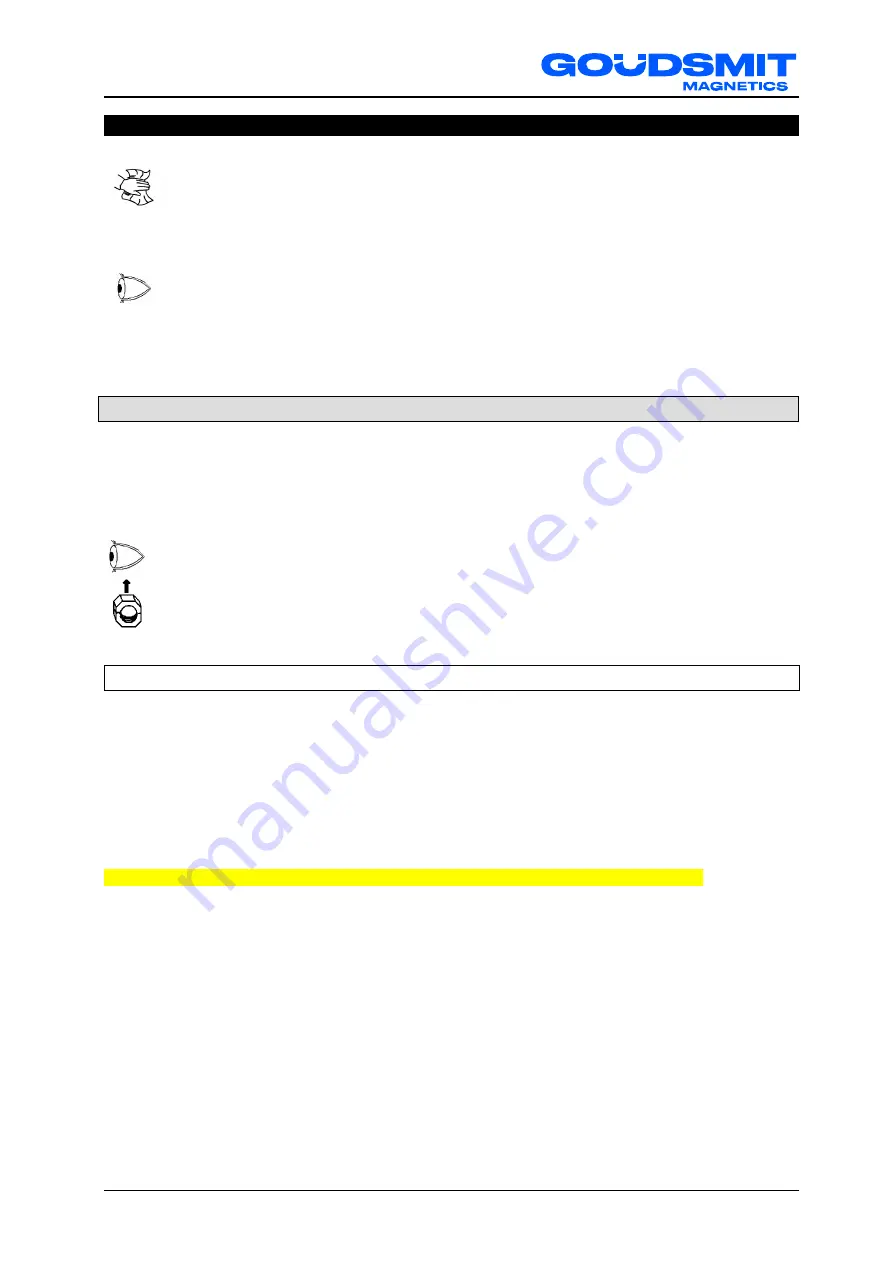
Maintenance
Page 29
Maintenance
Magnetic systems attract dust and Ferromagnetic particles.
Regular cleaning is essential.
All parts are best cleaned by pressurised air and/or rinsed with water.
Do NOT use pressurised water.
Regularly check that all warning pictograms and the identification plate are present at the correct
locations on the device. If lost or damaged, then immediately apply new ones to the original
locations.
Designate responsibility and always inform operating personnel regarding planned inspections,
maintenance, repairs or if attending to breakdowns.
Bearing systems
Note: If the system is equipped with a Sigmatek control unit, then it will automatically designate
greasing times to the operator. However, standard weekly greasing times may be programmed, but if
the machine runs for more than 100 hours a week, the control unit will add an extra greasing instruction.
Regularly check if the bearings make more noise than usual or if they are warmer than normal.
If this is the case, find out what the cause is and solve the problem(s). If necessary, replace the
bearing(s). For bearing replacement, please contact Goudsmit.
For bearing replacement intervals, combine your own experience of bearings in similar
applications with the recommended and/or estimated interval periods. If necessary, contact
Goudsmit Magnetics for advice.
Greasing with SKF LGMT2 grease
The bearing systems applied by GOUDSMIT all contain grease-lubricated bearings that are protected
against dirt and humidity. These use SKF LGMT2 grease. There are two sets of bearings that need to be
greased, a large outer tube bearing and a smaller rotor bearing.
Note: The bearing cover is on the side without the motor.
Once every three months or 1000 hours, remove the cover of the bearing and remove excess grease.
Follow the greasing instructions! Lubricate both sides of the machine!