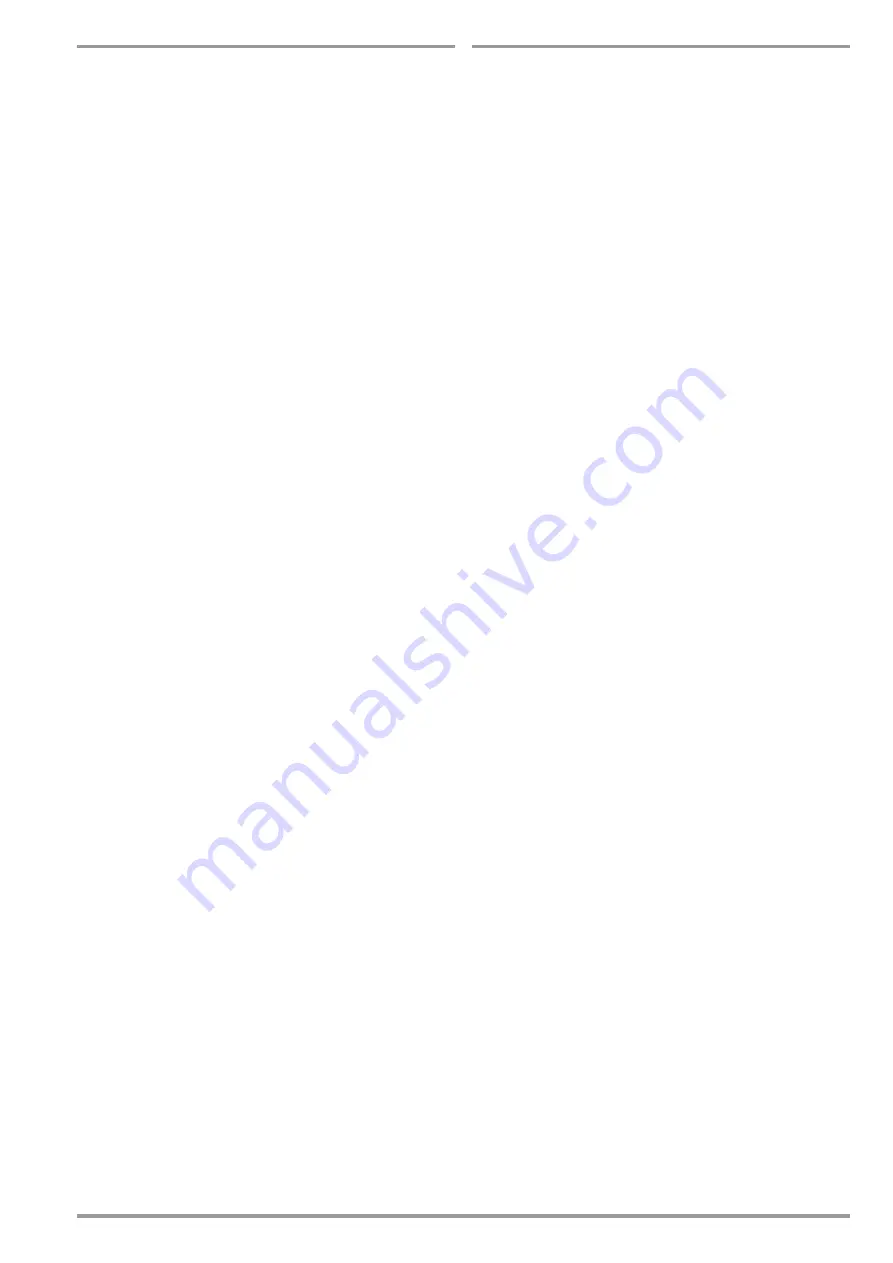
GMC-I Messtechnik GmbH
71
SIG1_SIG2, SIG1_SIG2? – Analog Interface Signal Outputs
Function and manual operation:
As opposed to manual operation, the computer generated
SIG1_SIG2
command addresses both signal outputs
simultaneously.
Signal output 1
: dependent upon power output status.
Signal output
2
: dependent upon current output control mode.
The status of the
SIG1_SIG2
function is
not
saved as a device
setting with the
SAVE
key.
See explanations on page 29 ff.
Programming
Setting command:
SI
G1_SIG2
txt1,txt2
Parameter:
txt1,txt2 (selection
)
Parameter type:
Text (character)
Default setting:
After RESET (*RST)
unchanged
Example
(HP Basic):
OUTPUT 713; "SIG1_SIG2 OUT, MODE"
Query
Displays the selected function for the signal outputs at the analog
interface.
Programming
Query command:
SI
G1_SIG2
?
Response string:
SIG1_SIG2
txt1,txt2
Length: 19
characters,
fixed
Parameter:
txt1, txt2 (selection)
Example
(HP Basic):
OUTPUT 713; "SIG1_SIG2?"
ENTER 713; A$
DISP A$
Display:
SIG1_SIG2 OUT,MODE
SRQ – SERVICE REQUEST
Functions
The service request
SRQ
is only available via the
IEEE
parallel
interface.
SRQ
can be activated by
any
device which is connected to the
IEC
bus.
SRQ
is
the only way for a device to trigger a specified action
at the
controller.
The
SRQ lead
is activated by the
KONSTANTER
when it
requests
service from the controller
.
SRQ
allows
for
simultaneous execution of several tasks
by the
controller
, and thus
increases
its
efficiency
.
The controller can execute other tasks
until
it receives an
SRQ
from the device
.
In
response
to the
SRQ message
via the IEC bus, the control
computer can start serial polling of the device status (
serial
poll
).
In this way, the
device which transmitted the SRQ
as well as the
reason
for the message, are both determined.
If
only one device is connected to the IEC bus
, the controller can
read out the status byte directly
and trigger the desired function
after receiving an SRQ.
Primarily, the
controller
should read out information regarding
device statuses and events.
The service request is transmitted via the
common interrupt lead
(SRQ)
at the IEC bus.
SRQ trigger conditions
can be
selected
from any of the messages
which occur in the event registers
(including MAV)
.
Which event message or messages result in an SRQ message
is determined by
setting the enable registers
accordingly (
SRQ
masking
).
If
all
utilized
devices with SRQ capability are equipped with
parallel polling
as well, it may be possible to identify the device
which generated the SRQ message
more quickly
by means of
this function, assuming they have been configured accordingly.
Example: SRQ triggering
upon receipt of an incorrect command:
Assuming all event registers have an initial value of 0.
An incorrect command is received.
The
ESR
(event standard register) sets bit 4 (
EXE
, execution
error) or bit 5 (
CME
, command error).
Did you previously set bits 4 and 5 in the
ESE
enable register
(command:
*ESE 48
)?
If so, the
ESR
group message is generated in the
STB
(status
byte register).
The associated
SRE
enable register must be set to bit 5
(command:
*SRE 32
).
The
ESR
bit is now able to generate the
MSS
group message
(master summary status).
The
MSS
group message enters itself once again to bit 6 in the
STB
(status byte).
In this way, a signal is generated indicating that there is
at least
one reason
for generating an
SRQ
message.
The
SRQ
message is then triggered by the downstream
service
request function
.
The respective
commands
for
setting
the assumed
SRQ
conditions are thus:
*ESE 48; *SRE 32
.
Service calls from the
ERA
and
ERB
event registers, or from the
MAV
message, are generated in the same way.
Setting range:
OFF
ON
SIG n
Passive high
Active low
OUT
OUTPUT ON
OUTPUT OFF
Passive high
Active low
MODE
OFF or CV
CC or OL
Passive high
Active low
SEQ
GO
Active low
SSET
OFF
ON
Passive high
Active low
U_LO
U
meas
U
min
U
meas
U
min
Passive high
Active low
U_HI
U
meas
U
max
U
meas
U
max
Passive high
Active low
I_LO
I
meas
I
min
I
meas
I
min
Passive high
Active low
I_HI
I
meas
I
max
I
meas
I
max
Passive high
Active low
Содержание SSP 120 Series
Страница 2: ...2 GMC I Messtechnik GmbH ...