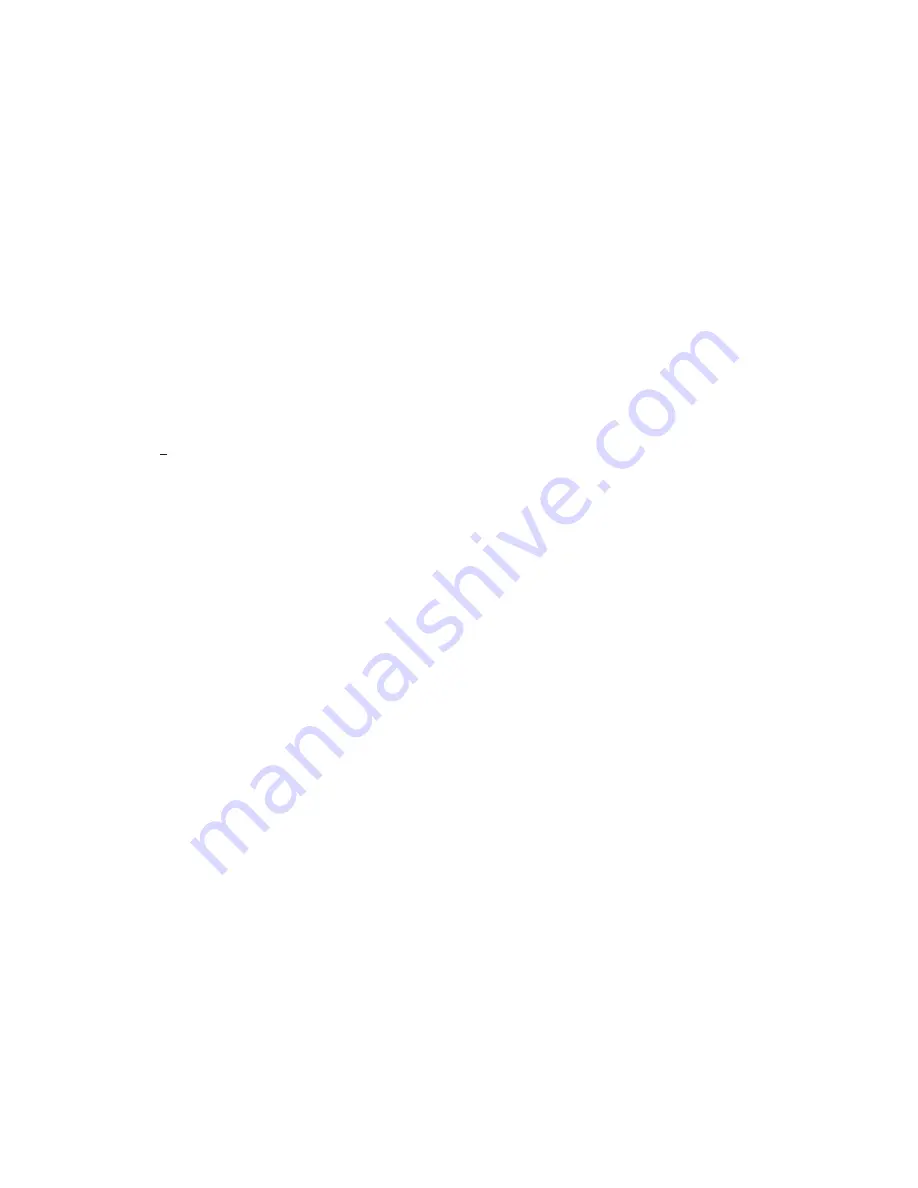
10
Figure 7 shows a schematic of a heat pump on the cooling cycle and the heating cycle. In addition to a reversing valve,
a heat pump is equipped with an expansion device and check valve for the indoor coil, and similar equipment for the
outdoor coil. It is also provided with a defrost control system.
The expansion devices are flowrator distributors and perform the same function on the heating cycle as on the cooling
cycle. The flowrator distributors also act as check valves to allow for the reverse of refrigerant flow.
When the heat pump is on the heating cycle, the outdoor coil is functioning as an evaporator. The temperature of the
refrigerant in the outdoor coil must be below the temperature of the outdoor air in order to extract heat from the air.
Thus, the greater the difference in the outdoor temperature and the outdoor coil temperature, the greater the heating
capacity of the heat pump. This phenomenon is a characteristic of a heat pump. It is a good practice to provide
supplementary heat for all heat pump installations in areas where the temperature drops below 45° F. It is also a good
practice to provide sufficient supplementary heat to handle the entire heating requirement should there be a component
failure of the heat pump, such as a compressor, or refrigerant leak, etc.
Since the temperature of the liquid refrigerant in the outdoor coil on the heating cycle is generally below freezing point,
frost forms on the surfaces of the outdoor coil under certain weather conditions of temperature and relative humidity.
Therefore, it is necessary to reverse the flow of the refrigerant to provide hot gas in the outdoor coil to melt the frost
accumulation. This is accomplished by reversing the heat pump to the cooling cycle. At the same time, the outdoor fan
stops to hasten the temperature rise of the outdoor coil and lessen the time required for defrosting. The indoor blower
continues to run and the supplementary heaters are energized.
DEFROST CONTROL
During operation the power to the circuit board is controlled by a temperature sensor, which is clamped to a feeder tube
entering the outdoor coil. Defrost timing periods of 30,60 and 90 minutes may be selected by setting the circuit board
jumper to 30, 60 and 90 respectively. Accumulation of time for the timing period selected starts when the sensor closes
(approximately 34 + 5° F), and when the wall thermostat calls for heat. At the end of the timing period, the unit’s defrost
cycle will be initiated provided the sensor remains closed. When the sensor opens (approximately 60° F), the defrost cycle
is terminated and the timing period is reset. If the defrost cycle is not terminated due to the sensor temperature, a
twelve minute override interrupts the unit’s defrost period.
SUGGESTED FIELD TESTING/TROUBLESHOOTING
1. Run unit in the heating mode (room thermostat calling for heat).
2. Check unit for proper charge.
Note: Bands of frost on the condenser coil indicate low refrigerant charge.
3. Shut off power to unit.
4. Disconnect outdoor fan by removing the outdoor fan motor wire from “DF2” on defrost control.
5. Restart unit and allow frost to accumulate.
6. After a few minutes of operation, the unit’s defrost thermostat should close. To verify this, check for 24 volts
between “DFT” and “C” on board. If the temperature at the thermostat is less than 28° F and the thermostat is
open, replace the unit’s defrost thermostat, as it is defective.
7. When the unit’s defrost thermostat has closed, short the test pins on the defrost board until the reversing valve
shifts, indicating defrost. This should take up to 22 seconds depending on what timing period the control is set on.
After defrost initiation, the short must instantly be removed or the unit’s defrost period will only last 3 seconds.
8. The control is shipped from the factory with the compressor delay option selected. This will de-energize the compressor
contactor for 30 seconds on defrost initiation and defrost termination. If the jumper is set to Normal, the compressor
will continue to run during defrost initiation and defrost termination. The control will also ignore the low pressure
switch connected to R-PS1 and PS2 for 5 minutes upon defrost initiation and 5 minutes after defrost termination.
9. After the unit’s defrost thermostat has terminated, check the defrost thermostat for 24 volts between “DFT” and
“C”. The reading should indicate 0 volts (open sensor).
10. Shut off power to unit.
11. Replace outdoor fan motor lead to terminal “DF2” on defrost board and turn on power.
AIR FLOW MEASUREMENT AND ADJUSTMENT
After reviewing section on DUCTING, proceed with airflow measurements and adjustments. Unit’s blower curves (in
Specification Sheets) are based on external static pressure (ESP, in. of W.C.). The duct openings on the unit are considered
internal static pressure, so as long as ESP is maintained, the unit will deliver the proper air up to the maximum static
pressure listed for the CFM required by the application (i.e. home, building, etc.).
In general 400 CFM per ton of cooling capacity is a rule of thumb. Some applications depending on the sensible and latent
capacity requirements may need only 350 CFM or up to 425 CFM per ton. Check condition space load requirements (from
load calculations) and equipment expanded ratings data to match CFM and capacity.
After unit is set and ducted, verify ESP with a 1" inclined manometer with pitot tubes or a Magnahelic gauge and confirm
CFM to blower curves in the specification sheets. All units have multiple speed blower motors. If factory selected speed
is not utilized, the speed tap can be changed. Never run CFM below 350 CFM per ton, evaporator freezing or poor unit
performance is possible.