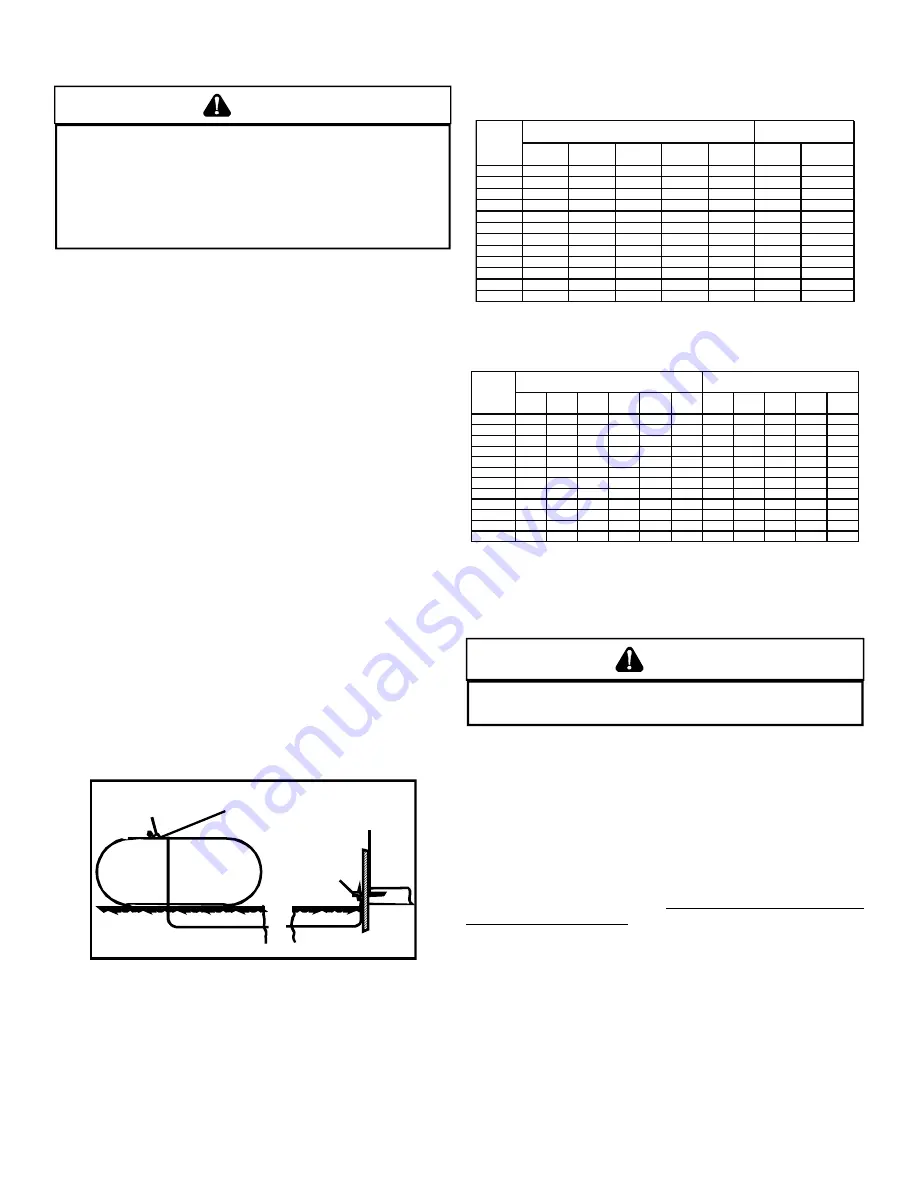
21
P
ROPANE
G
AS
T
ANKS
AND
P
IPING
WARNING
I
F THE GAS FURNACE IS INSTALLED IN A BASEMENT, AN EXCAVATED
AREA OR A CONFINED SPACE, IT IS STRONGLY RECOMMENDED TO
CONTACT A PROPANE SUPPLIER TO INSTALL A GAS DETECTING
WARNING DEVICE IN CASE OF A GAS LEAK.
•
S
INCE PROPANE GAS IS HEAVIER THAN AIR, ANY LEAKING GAS CAN
SETTLE IN ANY LOW AREAS OR CONFINED SPACES.
•
P
ROPANE GAS ODORANT MAY FADE, MAKING THE GAS UNDETECTABLE
EXCEPT WITH A W ARNING DEVICE.
A gas detecting warning system is the only reliable way to detect a
propane gas leak. Rust can reduce the level of odorant in propane
gas. Do not rely on your sense of smell. Contact a local propane
gas supplier about installing a gas detecting warning system. If
the presence of gas is suspected, follow the instructions on Page
4 of this manual.
All propane gas equipment must conform to the safety standards
of the National Board of Fire Underwriters, NBFU Manual 58.
For satisfactory operation, propane gas pressure must be 11 inch
w.c. at the furnace manifold with all gas appliances in operation.
Maintaining proper gas pressure depends on three main factors:
1. Vaporization rate, depending on temperature of the liquid,
and “wetted surface” area of the container or containers.
2. Proper pressure regulation. (Two-stage regulation is
recommended for both cost and efficiency).
3. Pressure drop in lines between regulators, and between
second stage regulator and the appliance. Pipe size will
depend on length of pipe run and total load of all appliances.
Complete information regarding tank sizing for vaporization,
recommended regulator settings, and pipe sizing is available from
most regulator manufacturers and propane gas suppliers.
Since propane gas will quickly dissolve white lead and most
standard commercial compounds, special pipe dope must be used.
Shellac-based compounds resistant to the actions of liquefied
petroleum gases such as Gasolac
®
, Stalactic
®
, Clyde’s
®
or John
Crane
®
are satisfactory.
Refer to the following illustration for typical propane gas installations
and piping.
200 PSIG
Maximum
5 to 15 PSIG
(20 PSIG Max.)
Continuous
11" W.C.
Second Stage
Regulator
First Stage
Regulator
Propane Gas Installation (Typ.)
P
ROPANE
G
AS
P
IPING
C
HARTS
Sizing Between First and Second Stage Regulator*
Maximum Propane Capacities listed are based on 2 psig pressure drop at 10 psig setting.
Capacities in 1,000 BTU/hour.
Pipe or
Nominal Pipe Size
Tubing
Tubing Size, O.D. Type L
Schedule 40
Length,
3/8"
1/2"
5/8"
3/4"
7/8"
1/2"
3/4"
Feet
10
730
1,700
3,200
5,300
8,300
3,200
7,500
20
500
1,100
2,200
3,700
5,800
2,200
4,200
30
400
920
2,000
2,900
4,700
1,800
4,000
40
370
850
1,700
2,700
4,100
1,600
3,700
50
330
770
1,500
2,400
3,700
1,500
3,400
60
300
700
1,300
2,200
3,300
1,300
3,100
80
260
610
1,200
1,900
2,900
1,200
2,600
100
220
540
1,000
1,700
2,600
1,000
2,300
125
200
490
900
1,400
2,300
900
2,100
150
190
430
830
1,300
2,100
830
1,900
175
170
400
780
1,200
1,900
770
1,700
200
160
380
730
1,100
1,800
720
1,500
To convert to capacities at 15 psig settings - multiply by 1.130
To convert to capacities at 5 psig settings - multiply by 0.879
Sizing Between Single or Second Stage Regulator and Appliance*
Maximum Propane Capacities Listed are Based on 1/2" W.C. pressure drop at 11" W.C. setting.
Capacities in 1,000 BTU/hour.
Pipe or
Nominal Pipe Size
Tubing
Tubing Size, O.D. Type L
Schedule 40
Length,
3/8"
1/2"
5/8"
3/4"
7/8"
1-1/8"
1/2"
3/4"
1"
1-1/4" 1-1/2"
Feet
10
39
92
199
329
501
935
275
567
1,071
2,205
3,307
20
26
62
131
216
346
630
189
393
732
1,496
2,299
30
21
50
107
181
277
500
152
315
590
1,212
1,858
40
19
41
90
145
233
427
129
267
504
1,039
1,559
50
18
37
79
131
198
376
114
237
448
913
1,417
60
16
35
72
121
187
340
103
217
409
834
1,275
80
13
29
62
104
155
289
89
185
346
724
1,066
100
11
26
55
90
138
255
78
162
307
630
976
125
10
24
48
81
122
224
69
146
275
567
866
150
9
21
43
72
109
202
63
132
252
511
787
200
8
19
39
66
100
187
54
112
209
439
665
250
8
17
36
60
93
172
48
100
185
390
590
*Data in accordance with NFPA pamphlet NO. 54
X. CIRCULATING AIR AND FILTERS
D
UCTWORK
- A
IR
F
LOW
WARNING
N
EVER ALLOW THE PRODUCTS OF COMBUSTION, INCLUDING CARBON
MONOXIDE, TO ENTER THE RETURN DUCTWORK OR CIRCULATION AIR SUPPLY.
Duct systems and register sizes must be properly designed for the
CFM and external static pressure rating of the furnace. Ductwork
should be designed in accordance with the recommended methods
of “Air Conditioning Contractors of America” Manual D.
A duct system must be installed in accordance with Standards of
the National Board of Fire Underwriters for the Installation of Air
Conditioning, Warm Air Heating and Ventilating Systems. Pamphlets
No. 90A and 90B.
A closed return duct system must be used, with the return duct
connected to the furnace.
NOTE:
Ductwork must never be attached
to the back of the furnace. Supply and return connections to the
furnace may be made with flexible joints to reduce noise
transmission. To prevent the blower from interfering with combustion
air or draft when a central return is used, a connecting duct must
be installed between the unit and the utility room wall. A room,
closet, or alcove must not be used as a return air chamber.
When the furnace is used in connection with a cooling unit, the
furnace should be installed in parallel with or on the upstream side
of the cooling unit to avoid condensation in the heating element.
With a parallel flow arrangement, the dampers or other means used
to control the flow of air must be adequate to prevent chilled air