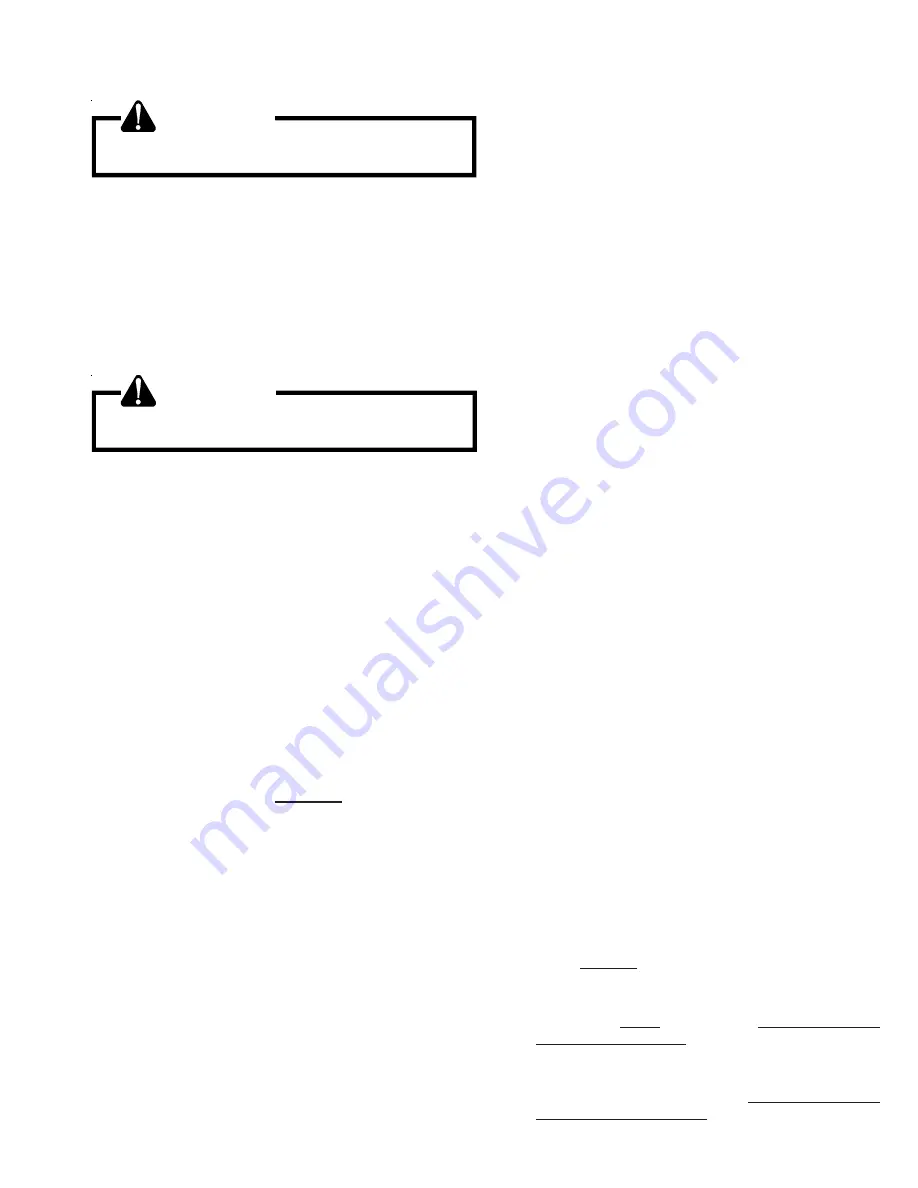
SERVICING
57
NOTICE
Violation of EPA regulations may result in fines
or other penalties.
Now determine if a burn out has actually occurred. Confirm
by analyzing an oil sample using a Sporlan Acid Test Kit, AK-
3 or its equivalent.
Remove the compressor and obtain an oil sample from the
suction stub. If the oil is not acidic, either a burnout has not
occurred or the burnout is so mild that a complete clean-up
is not necessary.
If acid level is unacceptable, the system must be cleaned by
using the clean-up drier method.
CAUTION
Do not allow the sludge or oil to contact the skin.
Severe burns may result.
NOTE:
The Flushing Method using R-11 refrigerant is no
longer approved by Goodman Company, L.P.
Suction Line Drier Clean-Up Method
Use AMANA
®
brand part number RF000127 suction line filter
drier kit. This drier should be installed as close to the
compressor suction fitting as possible. The filter must be
accessible and be rechecked for a pressure drop after the
system has operated for a time. It may be necessary to use
new tubing and form as required.
NOTE:
At least twelve (12) inches of the suction line
immediately out of the compressor stub must be discarded
due to burned residue and contaminates.
1. Remove compressor discharge line strainer.
2. Remove the liquid line drier and expansion valve.
3
Purge all remaining components with dry nitrogen or
carbon dioxide until clean.
4. Install new components
including
liquid line drier.
5. Braze all joints, leak test, evacuate, and recharge sys-
tem.
6. Start up the unit and record the pressure drop across the
drier.
7. Continue to run the system for a minimum of twelve (12)
hours and recheck the pressure drop across the drier.
Pressure drop should not exceed 6 PSIG.
8. Continue to run the system for several days, repeatedly
checking pressure drop across the suction line drier. If
the pressure drop never exceeds the 6 PSIG, the drier has
trapped the contaminants. Remove the suction line drier
from the system.
9. If the pressure drop becomes greater, then it must be
replaced and steps 5 through 9 repeated until it does not
exceed 6 PSIG.
NOTICE:
Regardless, the cause for burnout must be deter-
mined and corrected before the new compressor is started.
S-120 REFRIGERANT PIPING
The piping of a refrigeration system is very important in
relation to system capacity, proper oil return to compressor,
pumping rate of compressor and cooling performance of the
evaporator.
This long line set application guideline applies to all AHRI
listed R22 air conditioner and heat pump split system
matches of nominal capacity 18,000 to 60,000 Btuh. This
guideline will cover installation requirements and additional
accessories needed for split system installations where the
line set exceeds 50 feet in actual length.
Additional Accessories:
1.
Crankcase Heater
- a long line set application can
critically increase the charge level needed for a system.
As a result, the system is very prone to refrigerant
migration during its off-cycle and a crankcase heater will
help minimize this risk. A crankcase heater is recom-
mended for any long line application (50 watt minimum).
2.
TXV Requirement:
All line set applications over 50 ft will
require a TXV.
3.
Hard Start Assist
- increased charge level in long line
applications can require extra work from the compressor
at start-up. A hard start assist device may be required to
overcome this.
4.
Liquid Line Solenoid
- A long line set application can
critically increase the charge level needed for a system.
As a result, the system is very prone to refrigerant
migration during its off-cycle and a liquid line solenoid will
help minimize this. A liquid line solenoid is recommended
for any long line application on straight cooling units.
Tube Sizing:
1. In long line applications, the “equivalent line length” is the
sum of the straight length portions of the suction line plus
losses (in equivalent length) from 45 and 90 degree
bends.
Select the proper suction tube size based on
equivalent length of the suction line (see Tables 9 &
10) and recalculated system capacity.
Equivalent length = Length hori Length ve
Losses from bends (see Table 11)
2.
For any residential split system installed with a long
line set, the liquid line size must never exceed 3/8".
Limiting the liquid line size to 3/8" is critical since an
increased refrigerant charge level from having a larger
liquid line could possibly shorten a compressor’s lifespan.
3.
Single Stage Condensing Unit:
The maximum length
of tubing must not exceed 150 feet.
•
50 feet
is the maximum recommended vertical differ-
ence between the condenser and evaporator when the
evaporator is above the condenser. Equivalent length is
not to exceed 150 feet.
• The vertical difference between the condenser and
evaporator when the evaporator is below the condenser
can approach 150 feet, as long as the equivalent length
does not exceed 150 feet.
Содержание ASH Series
Страница 76: ...5 W D H PRODUCT DIMENSIONS Model Dimensions W x D x H GSH101203AC 35 x 35 x 41 ...
Страница 210: ...CONTROL COVER CONTROL BOX 4 RP 364A www goodmanmfg com www amana hac com ...
Страница 212: ...COMPRESSOR TUBING ASSEMBLY 6 RP 364A www goodmanmfg com www amana hac com ...
Страница 214: ...COIL CABINET TOP SIDE PANELS 8 RP 364A www goodmanmfg com www amana hac com ...
Страница 219: ...Control Cover Control Box 4 RP 436G www goodmanmfg com www amana hac com ...
Страница 221: ...Basepan Compressor Coil Assembly 6 RP 436G www goodmanmfg com www amana hac com ...
Страница 223: ...Tubing Assembly 8 RP 436G www goodmanmfg com www amana hac com ...
Страница 225: ...Cabinet Top Side Panels 10 RP 436G www goodmanmfg com www amana hac com ...
Страница 230: ...Control Cover Control Box 4 RP 356D ...
Страница 232: ...Tubing Assembly 6 RP 356D ...
Страница 234: ...Cabinet Top Side Panels Cond Coil 8 RP 356D ...
Страница 239: ...Control Cover Control Box 4 RP 392E www amana hac com ...
Страница 241: ...Coil Compressor Tubing 6 RP 392E www amana hac com ...
Страница 243: ...Cabinet Top Side Panels 8 RP 392E www amana hac com ...
Страница 248: ...Control Cover Control Box 4 RP 569A www goodmanmfg com www amana hac com ...
Страница 250: ...Cabinet Top Side Panels Cond Coil 6 RP 569A www goodmanmfg com www amana hac com ...
Страница 252: ...Tubing Assembly 8 RP 569A www goodmanmfg com www amana hac com ...