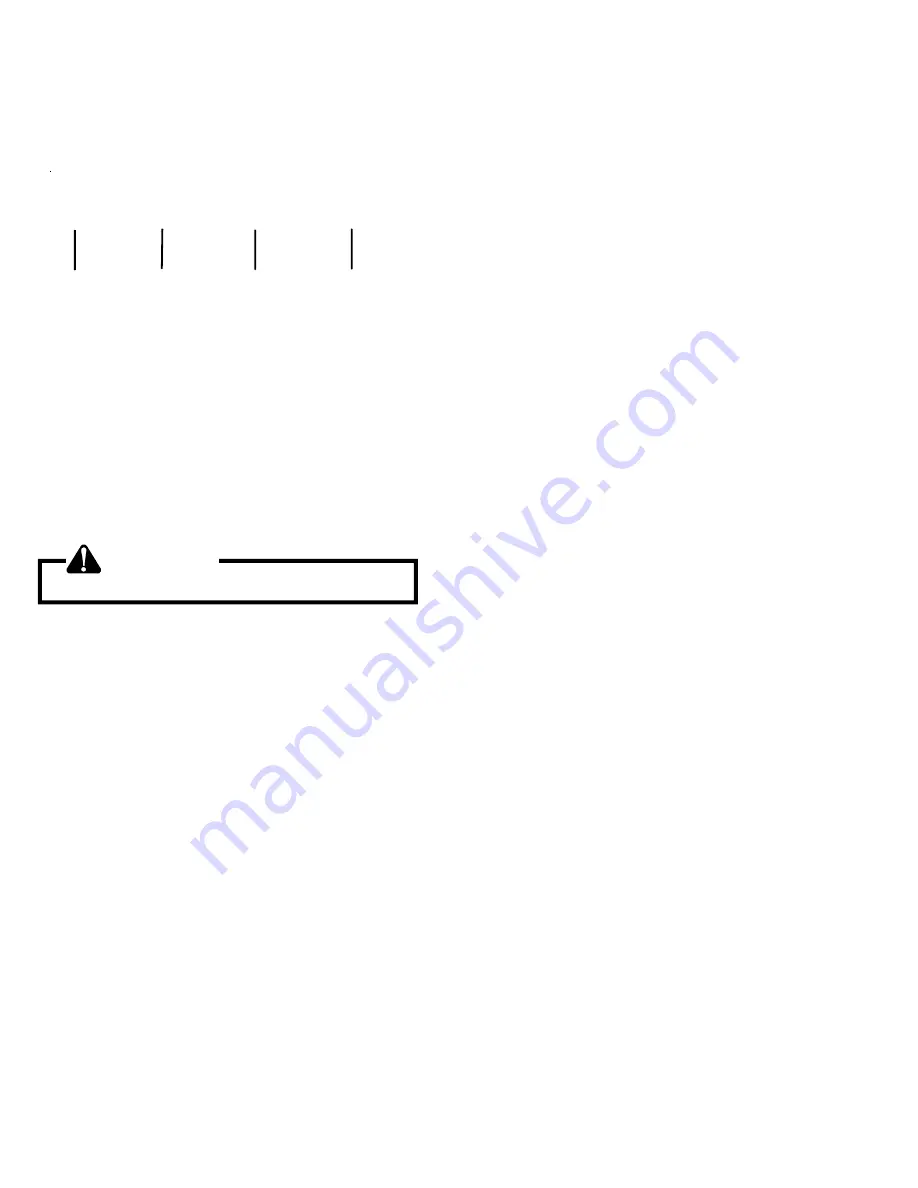
SERVICING
44
A. If the compressor starts and continues to run, the cause
for failure is somewhere else in the system.
B. If the compressor fails to start - replace.
COPELAND COMPRESSOR
03 A 12345 L
YEA R
M ONTH
SER IAL
NUM BER
PLANT
S-18 TESTING CRANKCASE HEATER
(OPTIONAL ITEM)
The crankcase heater must be energized a minimum of four
(4) hours before the condensing unit is operated.
Crankcase heaters are used to prevent migration or accumu-
lation of refrigerant in the compressor crankcase during the
off cycles and prevents liquid slugging or oil pumping on start
up.
A crankcase heater will not prevent compressor damage due
to a floodback or over charge condition.
WARNING
Disconnect ALL power before servicing.
1. Disconnect the heater lead in wires.
2. Using an ohmmeter, check heater continuity - should test
continuous. If not, replace.
NOTE:
The positive temperature coefficient crankcase heater
is a 40 watt 265 voltage heater. The cool resistance of the
heater will be approximately 1800 ohms. The resistance will
become greater as the temperature of the compressor shell
increases.
S-21 CHECKING REVERSING VALVE
AND SOLENOID
Occasionally the reversing valve may stick in the heating or
cooling position or in the mid-position.
When stuck in the mid-position, part of the discharge gas
from the compressor is directed back to the suction side,
resulting in excessively high suction pressure. An increase
in the suction line temperature through the reversing valve can
also be measured. Check operation of the valve by starting
the system and switching the operation from COOLING to
HEATING cycle.
If the valve fails to change its position, test the voltage (24V)
at the valve coil terminals, while the system is on the
COOLING cycle.
If no voltage is registered at the coil terminals, check the
operation of the thermostat an the continuity of the connect-
ing wiring from the "O" terminal of the thermostat to the unit.
If voltage is registered at the coil, tap the valve body lightly
while switching the system from HEATING to COOLING, etc.
If this fails to cause the valve to switch positions, remove the
coil connector cap and test the continuity of the reversing
valve solenoid coil. If the coil does not test continuous -
replace it.
If the coil test continuous and 24 volts is present at the coil
terminals, the valve is inoperative - replace it.
S-24 TESTING DEFROST CONTROL
To check the defrost control for proper sequencing, proceed
as follows: With power ON; unit not running.
1. Jumper defrost thermostat by placing a jumper wire
across the terminals "DFT" and "R" at defrost control
board.
2. Connect jumper across test pins on defrost control board.
3. Set thermostat to call for heating. System should go into
defrost within 21 seconds.
4. Immediately remove jumper from test pins.
5. Using VOM check for voltage across terminals "C & O".
Meter should read 24 volts.
6. Using VOM check for voltage across fan terminals DF1
and DF2 on the board. You should read line voltage (208-
230 VAC) indicating the relay is open in the defrost mode.
7. Using VOM check for voltage across "W2 & C" terminals
on the board. You should read 24 volts.
8. If not as above, replace control board.
9. Set thermostat to off position and disconnect power
before removing any jumpers or wires.
NOTE: Remove jumper across defrost thermostat before
returning system to service.
S-25 TESTING DEFROST THERMOSTAT
1. Install a thermocouple type temperature test lead on the
tube adjacent to the defrost control. Insulate the lead
point of contact.
2. Check the temperature at which the control closes its
contacts by lowering the temperature of the control. Part
# 0130M00009P which is used on 2 and 2.5 ton units
should close at 34°F ± 5°F. Part # 0130M00001P which
is used on 3 thru 5 ton units should close at 31°F ± 3°F.
3. Check the temperature at which the control opens its
contacts by raising the temperature of the control. Part #
0130M00009P which is used on 2 and 2.5 ton units
should open at 60°F ± 5°F. Part # 0130M00001P which
is used on 3 thru 5 ton units should open at 75°F ± 6°F.
4. If not as above, replace control.
Содержание ASH Series
Страница 76: ...5 W D H PRODUCT DIMENSIONS Model Dimensions W x D x H GSH101203AC 35 x 35 x 41 ...
Страница 210: ...CONTROL COVER CONTROL BOX 4 RP 364A www goodmanmfg com www amana hac com ...
Страница 212: ...COMPRESSOR TUBING ASSEMBLY 6 RP 364A www goodmanmfg com www amana hac com ...
Страница 214: ...COIL CABINET TOP SIDE PANELS 8 RP 364A www goodmanmfg com www amana hac com ...
Страница 219: ...Control Cover Control Box 4 RP 436G www goodmanmfg com www amana hac com ...
Страница 221: ...Basepan Compressor Coil Assembly 6 RP 436G www goodmanmfg com www amana hac com ...
Страница 223: ...Tubing Assembly 8 RP 436G www goodmanmfg com www amana hac com ...
Страница 225: ...Cabinet Top Side Panels 10 RP 436G www goodmanmfg com www amana hac com ...
Страница 230: ...Control Cover Control Box 4 RP 356D ...
Страница 232: ...Tubing Assembly 6 RP 356D ...
Страница 234: ...Cabinet Top Side Panels Cond Coil 8 RP 356D ...
Страница 239: ...Control Cover Control Box 4 RP 392E www amana hac com ...
Страница 241: ...Coil Compressor Tubing 6 RP 392E www amana hac com ...
Страница 243: ...Cabinet Top Side Panels 8 RP 392E www amana hac com ...
Страница 248: ...Control Cover Control Box 4 RP 569A www goodmanmfg com www amana hac com ...
Страница 250: ...Cabinet Top Side Panels Cond Coil 6 RP 569A www goodmanmfg com www amana hac com ...
Страница 252: ...Tubing Assembly 8 RP 569A www goodmanmfg com www amana hac com ...