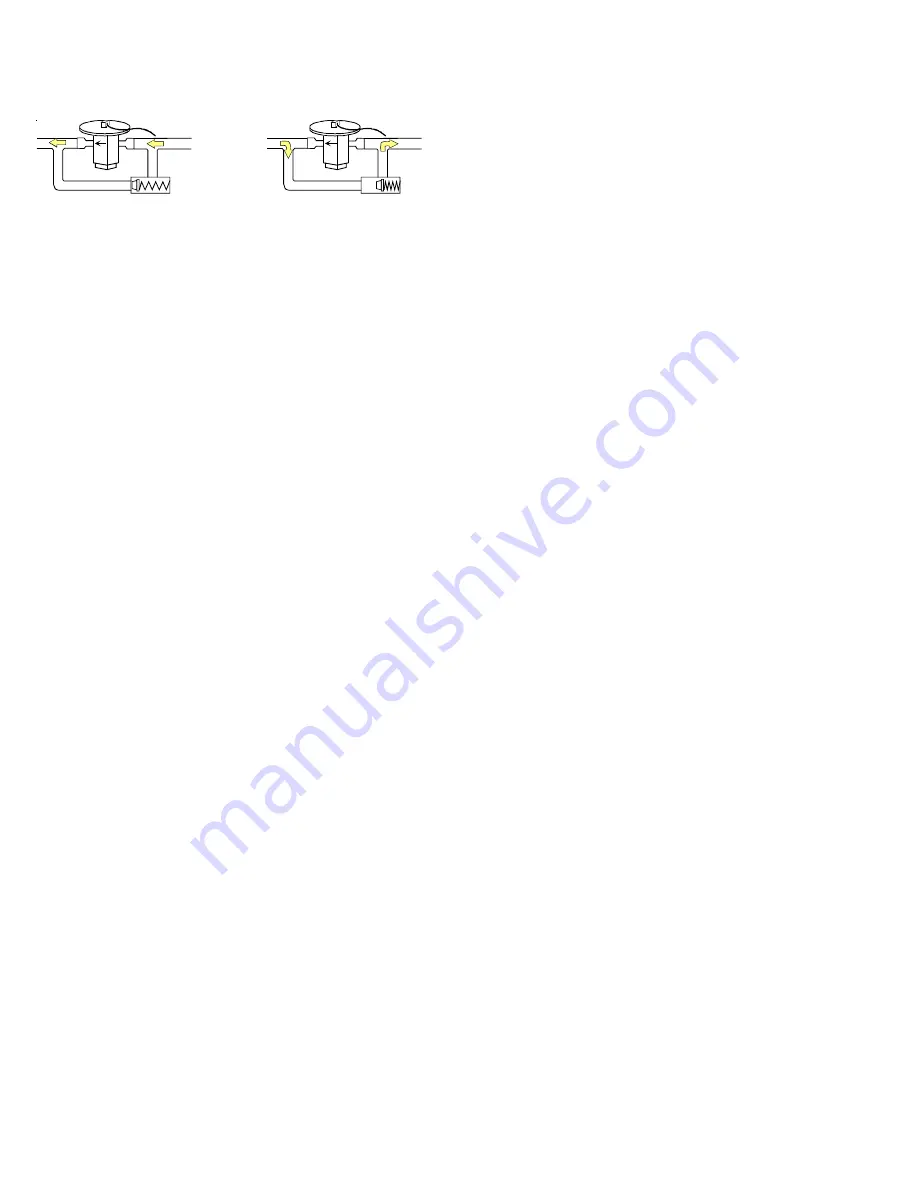
SERVICING
54
COOLING
HEATING
THERMOSTATIC EXPANSION VALVES
Some TXV valves contain an internal check valve thus
eliminating the need for an external check valve and bypass
loop. The three forces which govern the operation of the valve
are: (1) the pressure created in the power assembly by the
feeler bulb, (2) evaporator pressure, and (3) the equivalent
pressure of the superheat spring in the valve.
0% bleed type expansion valves are used on indoor and
outdoor coils. The 0% bleed valve will not allow the system
pressures (High and Low side) to equalize during the shut
down period. The valve will shut off completely at approxi-
mately 100 PSIG.
30% bleed valves used on some other models will continue
to allow some equalization even though the valve has shut-off
completely because of the bleed holes within the valve. This
type of valve should not be used as a replacement for a 0%
bleed valve, due to the resulting drop in performance.
The bulb must be securely fastened with two straps to a clean
straight section of the suction line. Application of the bulb to
a horizontal run of line is preferred. If a vertical installation
cannot be avoided, the bulb must be mounted so that the
capillary tubing comes out at the top.
THE VALVES PROVIDED BY GOODMAN ARE DESIGNED
TO MEET THE SPECIFICATION REQUIREMENTS FOR
OPTIMUM PRODUCT OPERATION. DO NOT USE SUB-
STITUTES.
S-106 OVERFEEDING
Overfeeding by the expansion valve results in high suction
pressure, cold suction line, and possible liquid slugging of the
compressor.
If these symptoms are observed:
1. Check for an overcharged unit by referring to the cooling
performance charts in the servicing section.
2. Check the operation of the power element in the valve as
explained in S-110 Checking Expansion Valve Operation.
3. Check for restricted or plugged equalizer tube.
S-107 UNDERFEEDING
Underfeeding by the expansion valve results in low system
capacity and low suction pressures.
If these symptoms are observed:
1. Check for a restricted liquid line or drier. A restriction will
be indicated by a temperature drop across the drier.
2. Check the operation of the power element of the valve as
described in S-110 Checking Expansion Valve Operation.
S-108 SUPERHEAT
The expansion valves are factory adjusted to maintain 12 to
18 degrees superheat of the suction gas. Before checking
the superheat or replacing the valve, perform all the proce-
dures outlined under Air Flow, Refrigerant Charge, Expan-
sion Valve - Overfeeding, Underfeeding. These are the most
common causes for evaporator malfunction.
CHECKING SUPERHEAT
Refrigerant gas is considered superheated when its tempera-
ture is higher than the saturation temperature corresponding
to its pressure. The degree of superheat equals the degrees
of temperature increase above the saturation temperature at
existing pressure. See Temperature - Pressure Chart Table
7.
1. Attach an accurate thermometer or preferably a thermo-
couple type temperature tester to the suction line at a
point at least 6" from the compressor.
2. Install a low side pressure gauge on the suction line ser-
vice valve at the outdoor unit.
3. Record the gauge pressure and the temperature of the
line.
4. Convert the suction pressure gauge reading to tempera-
ture by finding the gauge reading in Temperature - Pres-
sure Chart and reading to the left, find the temperature in
the °F. Column.
5. The difference between the thermometer reading and pres-
sure to temperature conversion is the amount of super-
heat.
EXAMPLE:
a. Suction Pressure = 84
b. Corresponding Temp. °F. = 50
c. Thermometer on Suction Line = 63°F.
To obtain the degrees temperature of superheat subtract 50.0
from 63.0°F.
The difference is 13° Superheat. The 13° Superheat would
fall in the ± range of allowable superheat.
SUPERHEAT ADJUSTMENT
The expansion valves used on Amana® brand coils are
factory set and are not field adjustable. If the superheat
setting becomes disturbed, replace the valve.
On systems using capillary tubes or flow control restrictors,
superheat is adjusted in accordance with the "DESIRED
SUPERHEAT vs. OUTDOOR TEMP" chart as explained in
section S-103 CHARGING.
Содержание ASH Series
Страница 76: ...5 W D H PRODUCT DIMENSIONS Model Dimensions W x D x H GSH101203AC 35 x 35 x 41 ...
Страница 210: ...CONTROL COVER CONTROL BOX 4 RP 364A www goodmanmfg com www amana hac com ...
Страница 212: ...COMPRESSOR TUBING ASSEMBLY 6 RP 364A www goodmanmfg com www amana hac com ...
Страница 214: ...COIL CABINET TOP SIDE PANELS 8 RP 364A www goodmanmfg com www amana hac com ...
Страница 219: ...Control Cover Control Box 4 RP 436G www goodmanmfg com www amana hac com ...
Страница 221: ...Basepan Compressor Coil Assembly 6 RP 436G www goodmanmfg com www amana hac com ...
Страница 223: ...Tubing Assembly 8 RP 436G www goodmanmfg com www amana hac com ...
Страница 225: ...Cabinet Top Side Panels 10 RP 436G www goodmanmfg com www amana hac com ...
Страница 230: ...Control Cover Control Box 4 RP 356D ...
Страница 232: ...Tubing Assembly 6 RP 356D ...
Страница 234: ...Cabinet Top Side Panels Cond Coil 8 RP 356D ...
Страница 239: ...Control Cover Control Box 4 RP 392E www amana hac com ...
Страница 241: ...Coil Compressor Tubing 6 RP 392E www amana hac com ...
Страница 243: ...Cabinet Top Side Panels 8 RP 392E www amana hac com ...
Страница 248: ...Control Cover Control Box 4 RP 569A www goodmanmfg com www amana hac com ...
Страница 250: ...Cabinet Top Side Panels Cond Coil 6 RP 569A www goodmanmfg com www amana hac com ...
Страница 252: ...Tubing Assembly 8 RP 569A www goodmanmfg com www amana hac com ...