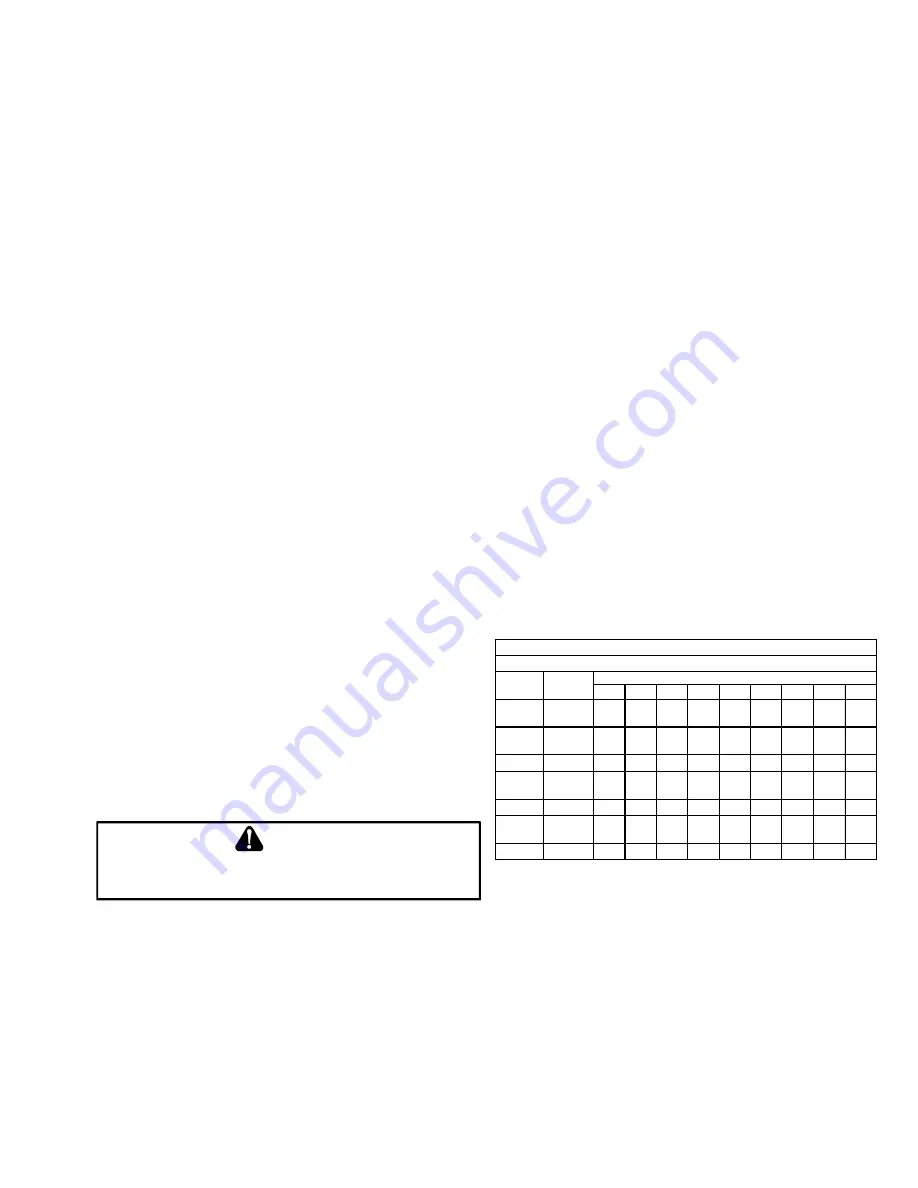
27
7.
Upflow
and
Counterflow
units
.
For
upright installations
, externally mount the rubber
elbow to the vent/flue coupling using a worm gear hose
clamp. Secure field supplied vent/flue piping to the
rubber elbow using a worm gear hose clamp.
NOTE:
Use of the alternate vent/flue location for upright instal-
lations, requires the drain trap be installed on the
same side of the unit as the flue pipe.
8.
Upflow
and
Counterflow
units
.
For
horizontal installations
, externally secure the
field-supplied vent/flue pipe directly to the vent/flue cou-
pling using a PVC or ABS coupling or elbow.
A
LTERNATE
C
OMBUSTION
A
IR
I
NTAKE
L
OCATION
The alternate combustion air intake location consists of a large,
unobstructed hole (alternate vent connection is aligned with the
Induced Draft Blower). To use the alternate combustion air intake
location, refer to the following steps, and the “Alternate Combus-
tion Air Intake Location” figure.
1.
Remove and save the four screws securing the com-
bustion air intake coupling to the basepan. Remove an
additional three screws securing the furnace’s internal
combustion air intake pipe to the blower deck.
2.
Remove the combustion air intake pipe from the fur-
nace and cut the pipe at the basepan coupling. Save
the basepan coupling and gasket from the blower deck
coupling for use in the alternate location. Discard the
remaining pipe.
3.
Remove plastic plug from alternate combustion air in-
take location. Relocate and install plug in standard air
intake location (basepan). Plug the remaining hole in
the blower deck with the plastic plug included in the
drain kit bag.
4.
With the gasket facing the cabinet side panel, and the
flange’s flat spot facing forward, secure the combustion
air intake coupling to the cabinet using the screws re-
moved in step 1 or with field-supplied 3/8” #8 self -drill-
ing screws.
B
E
SURE
NOT
TO
DAMAGE
INTERNAL
WIRING
OR
OTHER
COMPONENTS
WHEN
REINSTALLING
COUPLING
AND
SCREWS
.
CAUTION
5.
For
non-direct vent installation
s
installed
horizon-
tally
, a minimum of one 90° elbow should be installed
on the combustion air intake coupling to guard against
inadvertent blockage. No elbow is required on the al-
ternate combustion air intake of
upright
installations,
however, a minimum clearance of 2 inches is required
to assure proper air supply.
6.
For
direct vent installations
, secure field-supplied
combustion air intake pipe directly to the air intake
coupling.
NOTE:
A PVC coupling or elbow is required on
counterflow units.
N
ON
-D
IRECT
V
ENT
(S
INGLE
P
IPE
) P
IPING
Non-direct
vent
installations require only a vent/flue pipe. The
vent pipe can be run horizontally with an exit through the side of
the building or run vertically with an exit through the roof of the
building. The vent can also be run through an existing
unused
chimney; however, it must extend a minimum of 12 inches above
the top of the chimney. The space between the vent pipe and the
chimney must be closed with a weather-tight, corrosion-resistant
flashing. For details concerning connection of the vent/flue pipe
to the furnace, refer to
Vent/Flue Pipe and Combustion Air - Stan-
dard Furnace Connections
or
Alternate Furnace Connections
for
specific details. Refer to the following
Non-Direct Vent (Single
Pipe) Piping - Vent/Flue Pipe Terminations
for specific details on
termination construction.
Although
non-direct
vent
installations do not require a combus-
tion air intake
pipe
, a minimum of one 90° elbow should be at-
tached to the furnace’s combustion air intake
if
: an upright instal-
lation uses the standard intake location, or a horizontal installa-
tion uses the alternate air intake location. This elbow will guard
against inadvertent blockage of the air intake.
V
ENT
/F
LUE
P
IPE
L
ENGTHS
AND
D
IAMETERS
Refer to the following table for applicable length, elbows, and pipe
diameter for construction of the vent/flue pipe system of a non-
direct vent installation. In addition to the vent/flue pipe, a single
90° elbow should be secured to the combustion air intake to
prevent inadvertent blockage. The tee used in the vent/flue termi-
nation must be included when determining the number of elbows
in the piping system.
0
1
2
3
4
5
6
7
8
60,000
2
or 2 1/2
250
245
240
235
230
225
220
215
210
80,000
2
or 2 1/2
250
245
240
235
230
225
220
215
210
80,000
3
250
243
236
229
222
215
208
201
194
100,000
2
or 2 1/2
90
85
80
75
70
65
60
55
50
100,000
3
250
243
236
229
222
215
208
201
194
115,000
2
or 2 1/2
75
70
65
60
55
50
45
40
35
115,000
3
220
213
206
199
192
185
178
171
164
*MVM9/*CVM9 Direct Vent (2 - Pipe) and Non-Direct Vent (1- Pipe)
(6)
Maximum Allowable Length of Vent/Flue Pipe & Combustion Air Pipe (ft)
(1) (2)
Unit Input
(Btu)
Pipe Size
(4)
(in.)
Number of Elbows
(3) (5)
1) Maximum allowable limits listed on individual lengths for inlet and flue
and NOT a combination.
2) Minimum requirement for each vent pipe is five (5) feet in length and
one elbow/tee.
3) Tee used in the vent/flue termination must be included when deter-
mining the number of elbows in the piping system.
4) 2 1/2” or 3” diameter pipe can be used in place of 2” diameter pipe.
5) Increased Clearance Configurations using (2) 45 deg. Elbows should
be considered equivalent to one 90 deg. elbow.
6) One 90° elbow should be secured to the combustion air intake con-
nection.
PRODUCT DESIGN