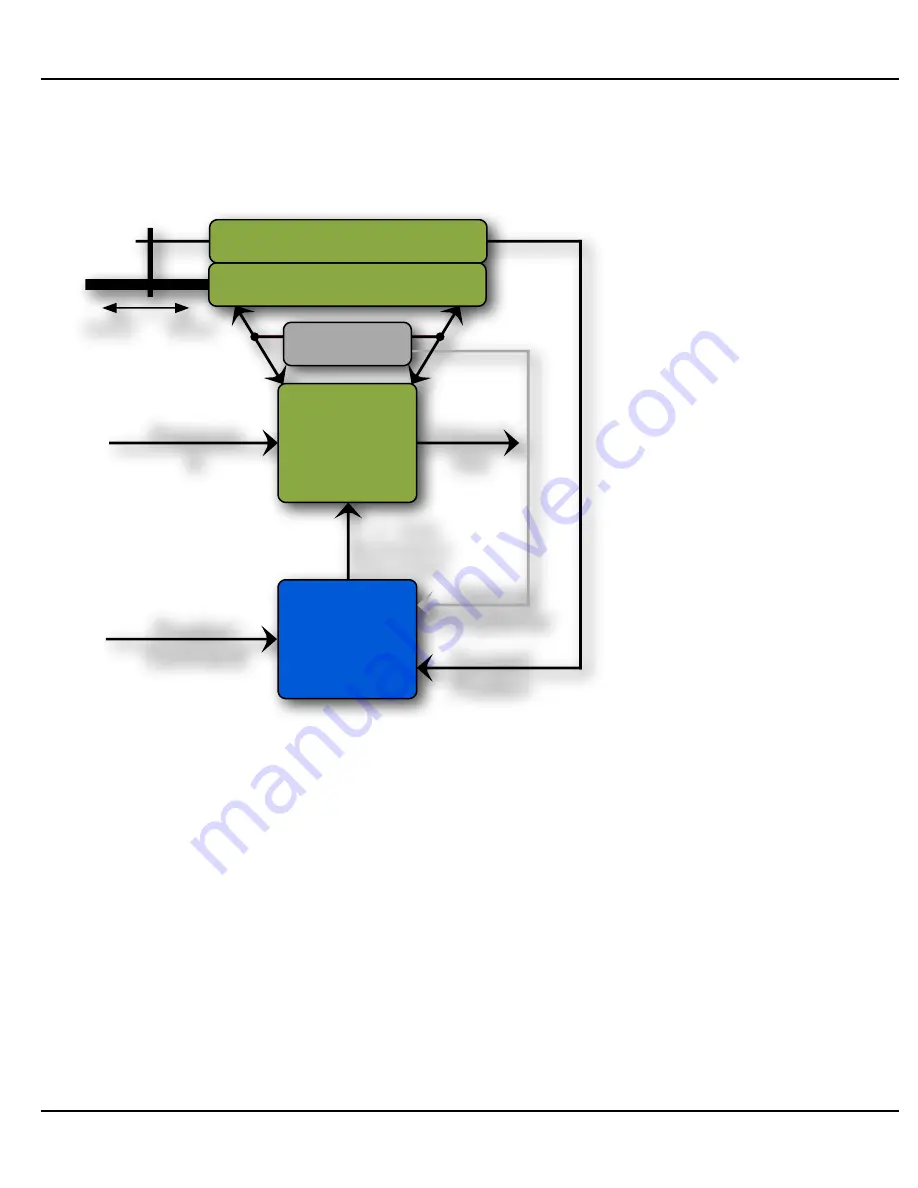
temporary. If you continue holding the actuator in a displaced position, it will soon
begin to fight you to move the actuator back to the original position using all its
strength.
If any actuator in a compliant figure is moved, the other actuators will feel the
changes in their loads and
move in sympathy. This
makes for a much more
'lifelike' animatronic.
If you tell a compliant
actuator to start moving
sharply, the acceleration
inertia of the actuator will be
s e n s e d , a n d t h e E F B
controller will open the
ServoValve/Motor Controller
more than just the positional
error would have caused.
This accelerates the actuator
more quickly.
C o n v e r s e l y, w h e n t h e
actuator is stopped abruptly,
the deceleration inertia is
sensed, and this can cause
t h e S e r v o Va l v e / M o t o r
Controller to close, or even open the ServoValve/Motor Controller in the reverse
direction to provide active braking to the actuator.
The net result is that the actuator will move when you push on it, making it seem
'softer', but can accelerate and decelerate more quickly than a non-compliant actuator
making it seem 'stiffer'.
Optional
'Compliance'
Differential
Pressure Sensor
ServoValve
(+/- 10
vdc Input)
Actuator
(Pneumatic or Hydraulic Cylinder)
Electronic
FeedBack
Controller
(EFB)
Position Sensor
'Position'
Command
+/- 10vdc
Command to
ServoValve
'Current'
Position
Pressure
In
Exhaust
Out
Retract
Extend
Gilderfluke & Co.• 205 South Flower Street • Burbank, California 91502 • 818/840-9484 • 800/776-5972 • fax 818/840-9485
Br-EFB Manual / May 22, 2018 3:28 PM / page 20 of 142