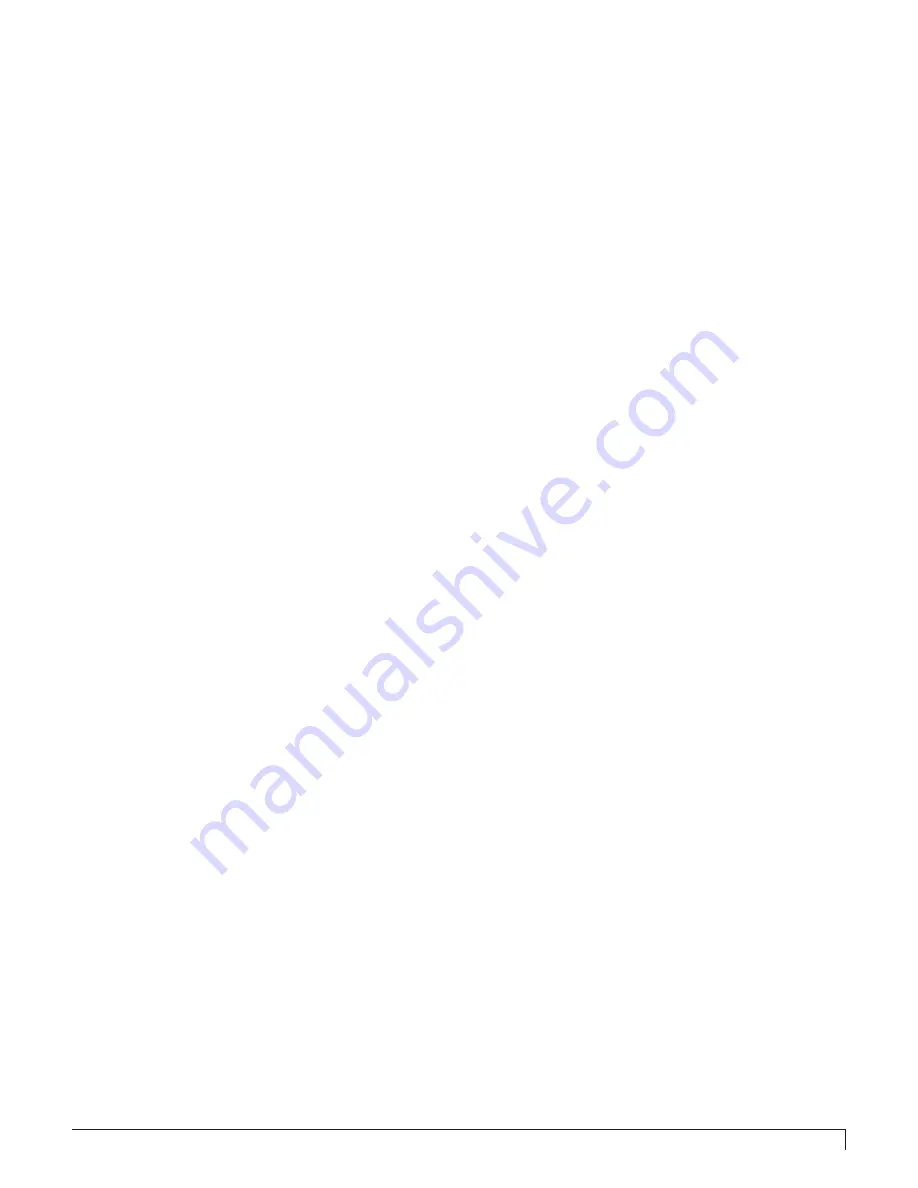
45
Genesis LXP
®
© 2015 Genesis Attachments, LLC
WELDING MAINTENANCE
GENERAL WELDING GUIDELINES
Build-up and hard-surfacing are welding procedures that protect the parent material of the jaws
and keep the blades in good adjustment. Build-up is the welding procedure that restores the jaws
to their original shape. Building up the jaws helps protect the blades and increases the life of the
shear. Hard-surfacing is the welding material added over the parent material (or build-up material)
to create a wear-resistant surface.
Welding should not be performed until the jaws are work-hardened. Work-hardening can take up
to 80 hours. However, shear jaws must not wear lower than the height of a new blade. If either
jaw wears down lower than blade height, immediately stop operating the processor and perform
build-up and hard-surfacing as described in the following pages of this manual.
When welding around blade seats or the piercing tip tang area, maintain the factory machined seat
radius. If the rounded grooves are welded up, use a die grinder with a carbide tool to recut these
areas to their original profile. Leaving a squared edge will eventually cause structural cracking.
The radius provides a broader area to absorb structural stress.
Before you begin:
•
Remove adjacent blades, as preheating and welding may cause blade damage.
•
Wearing an approved respirator, grind the area to clean it, removing all existing hard-surfacing.
• Preheat area to 350˚F (177˚C). Maintain this temperature throughout the procedure. Do
not exceed 450˚F interpass temperature.
During welding:
•
Always grind and weld with the grain of the material.
•
Peen each weld pass to relieve stress and harden the welds.
•
Do not undercut the ends of the welds.
•
Do not start or stop welds directly above a bolt hole or in the apex of the jaw.
After welding maintenance is complete:
•
Cover the area with a heat blanket and allow it to cool slowly, approximately eight hours.
•
Do not put the jaw set into operation until the welds have been allowed to cool.
Welding Ground Clamp
Disconnect all battery ground cables or shut off master battery switch, if equipped. Failure to do
so may cause excavator electrical problems, including permanent damage to onboard computer
systems.
Connect ground clamp as close as possible to the area being welded without allowing current to
pass through the pivot group, cylinder pin, cylinder, swivel, motor, gearbox or slewing ring.
If you are welding on the lower jaw, connect weld clamp to the lower. If you are welding on the
upper jaw, connect to the upper but not to the cylinder clevis. If needed, weld a piece of steel to
the area for the grounding clamp and cut the piece off when welding is completed.
Welding Rules