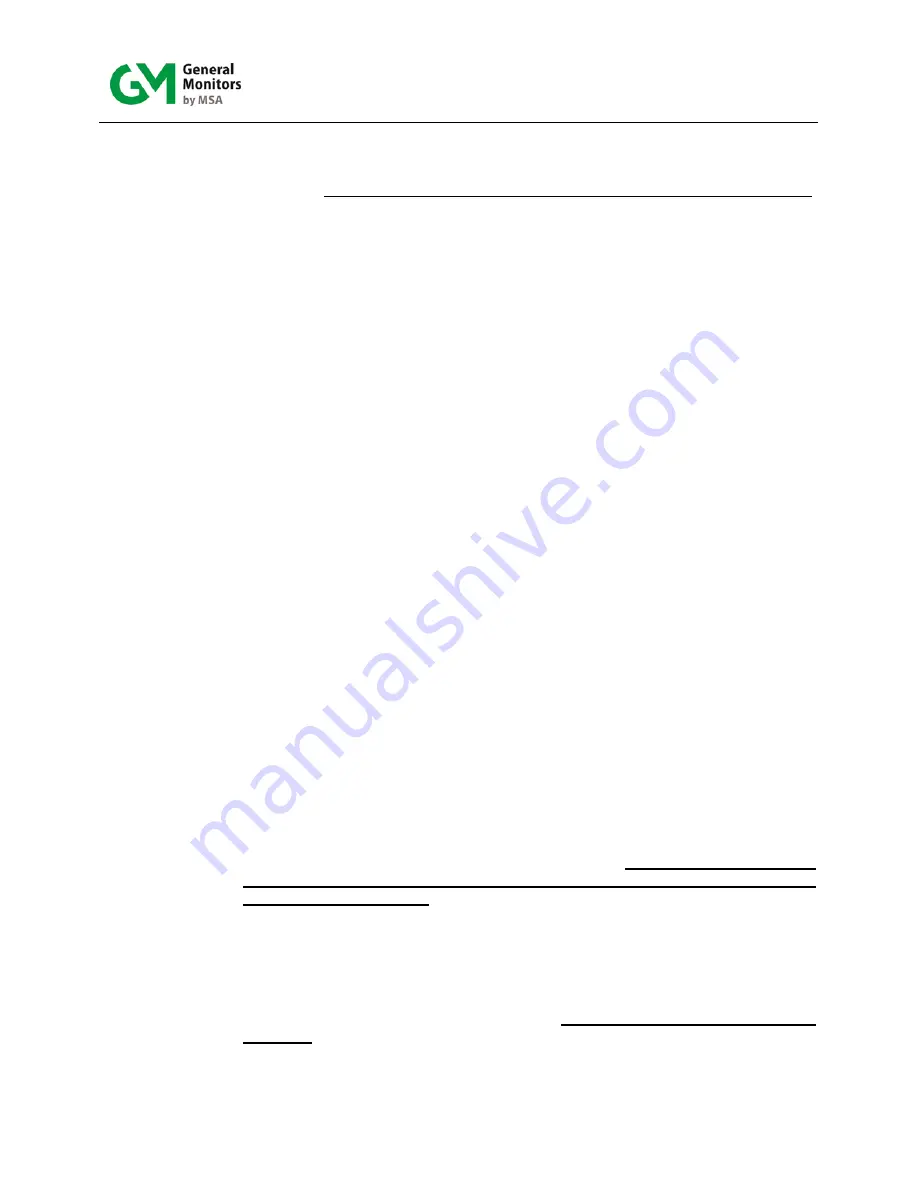
Model IR5500
Quick Start Guide
xii
first few threads of each M6 screw. A packet of lubricant is included with the pan/tilt
assembly. Without lubricant, alignment will be more difficult, and bolts may seize.
Verify that the back two screws have been hand-tightened but that the front two have
not. Hand-tighten the 24 mm nut for the pan-tilt assembly. On the assembly, verify
that the front and back fine adjust screws are flush with the assembly surface, to allow
full movement of tilt. If necessary, use a 2.5 mm hex wrench to adjust the screws.
Align the notch and pin of the sights with the Source center.
3. At the Source, adjust the Source pan (side-to-side) for maximum signal level. Slowly
tighten the 24 mm nut at the bottom of the pan-tilt assembly while holding the left side
of the Source. Verify that the signal level is reduced by 10% or less.
4. At the Source, check the four M6 screws that hold the unit to the pan-tilt assembly.
Verify that the back two screws have been hand-tightened but that the front two have
not. On the pan-tilt assembly, verify that the front and back fine adjust screws are
flush with the assembly surface. Use the housing sights to aim the unit at the center of
the Source. Verify that the Receiver display is 0. If the Receiver does not have
adequate signal from the Source, it may be in fault, depending on fault delay settings.
Put the magnet on the upper right edge of the display over the GM logo. The display
will change from 0 to rst, ---, SE, in, and Pct or AJ. To align the system using AJ, refer
to the Appendix. To align the system using Pct, remove the magnet when Pct
appears. Apply the magnet when Pth appears. Select the units for the path length,
enter the path length (LEn), and whether or not there is an attenuator on the Source
(nAt/At, for 5-30m range systems only), whether or not there is a visible light filter on
the Source (nLF/LF), and Fi to finish the Pth menu. The path length entered (LEn)
should be accurate to within ±5% of the actual distance. The Receiver will display a
number that is a percent of expected signal level. Aim for 100 percent or higher. The
minimum acceptable percent is 80. Below 50, the alignment fault F20 will be set.
5. At the Source, lightly tighten the front fine adjust screw until it bottoms out against the
internal tilt lever. Slowly make a small turn to tighten the screw and lower the front of
the Source. Wait a few seconds for the signal level number at the Receiver to settle.
Continue making small turns, waiting after each turn for the signal level number to
settle. Once the signal level number begins to decline, back out the front fine adjust
screw until it is flush with the assembly surface. Lightly tighten the back fine adjust
screw until it bottoms out, and then slowly make a small turn to further tighten it. Wait
a few seconds for the signal level number to settle. Continue until the signal level
reaches its maximum and begins to decline. Back out the back fine adjust screw.
6. Secure all four M6 mounting screws, tightening them gradually and alternately in a
crisscross pattern to minimize change in alignment. Verify that signal level is reduced
by 10% or less (increase of any amount is acceptable).
To complete alignment, all
four M6 mounting screws and the 24 mm nut of the pan/tilt assembly must be
fully tightened and secure
.
7. With the Source secure, repeat steps 3 through 6 for the Receiver. The Pct should be
at least 80 percent. Aim for 100 percent or higher.
8. Once adjusts are done and the signal level has been maximized, put the magnet on
the upper right edge of the display to exit alignment mode. The unit will display a
flashing AC and begin zeroing the gas reading. Once zeroing is complete, the unit will
display 0C, followed by the gas concentration.
To complete alignment, 0C must be
displayed.
With all screws secured on both units, once 0C is displayed, system
alignment is complete.