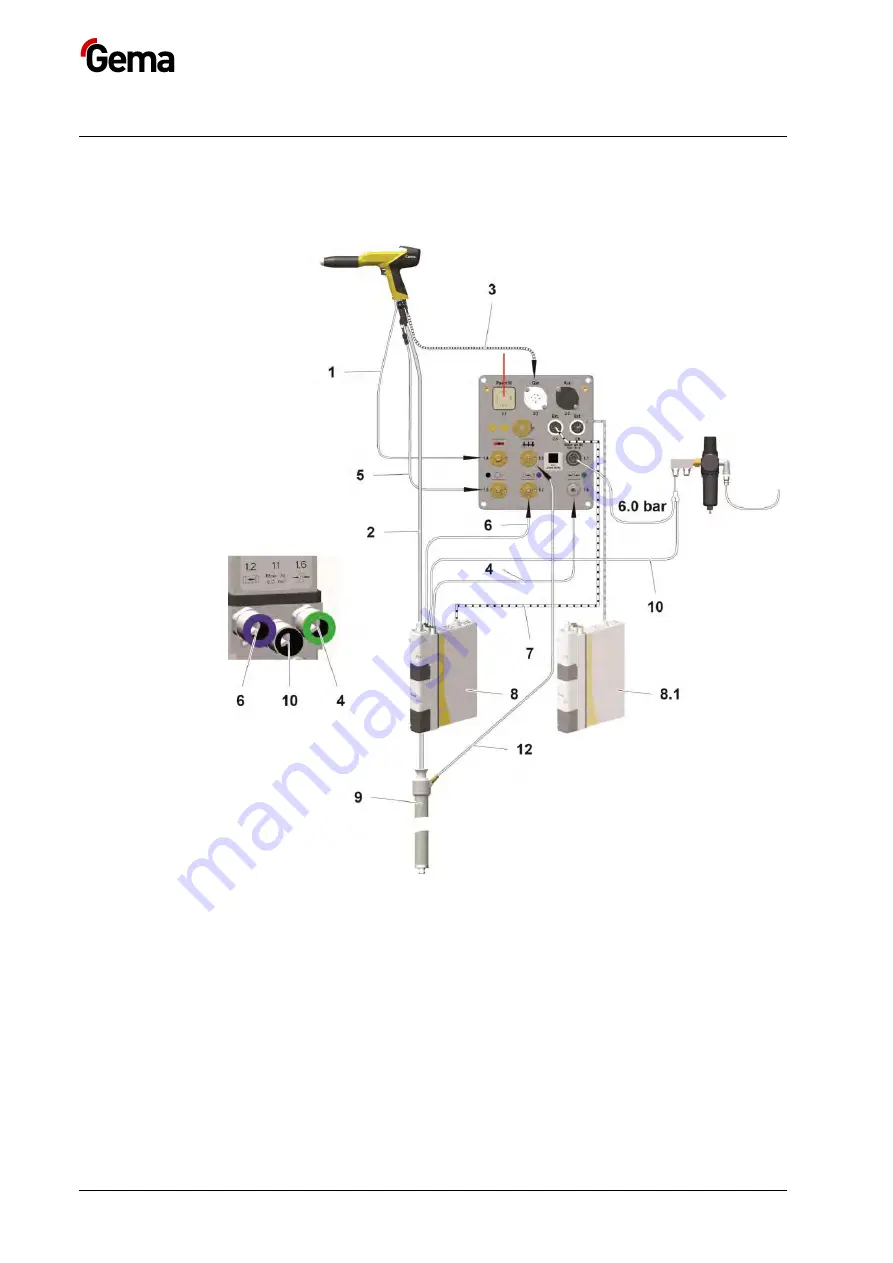
Rev. 00 03/19
24
Assembly / Connection
OptiFlex Pro B Spray
Connection instructions
The Gun control unit and the Application pump(s) are supplied ready for
use by the manufacturer. Just a few cables and hoses must be
connected.
fig. 6: Connecting guide – overview
1 Electrode rinsing air hose
2 Powder hose
3 Gun cable
4 Pinch valve air hose
5 Spraying air hose
6 Transport air hose
7 Control signal cable
8 Application pump no. 1
8.1 Application pump no. 2
9 Fluidizing/suction tube
10 Compressed air hose
12 Fluidizing air hose
Содержание OptiFlex Pro B Spray
Страница 5: ...Rev 00 03 19 OptiFlex Pro B Spray Table of contents 5 Diffuser OptiSelect 54 Pneumatic group 55 ...
Страница 6: ......
Страница 14: ...Rev 00 03 19 14 Safety OptiFlex Pro B Spray ...
Страница 22: ...Rev 00 03 19 22 Product description OptiFlex Pro B Spray ...
Страница 26: ...Rev 00 03 19 26 Assembly Connection OptiFlex Pro B Spray ...
Страница 48: ...Rev 00 03 19 48 Disposal OptiFlex Pro B Spray ...
Страница 51: ...Rev 00 03 19 OptiFlex Pro B Spray Spare parts list 51 OptiFlex Pro B Spray Spare parts fig 10 ...
Страница 56: ......
Страница 58: ...Rev 00 ...