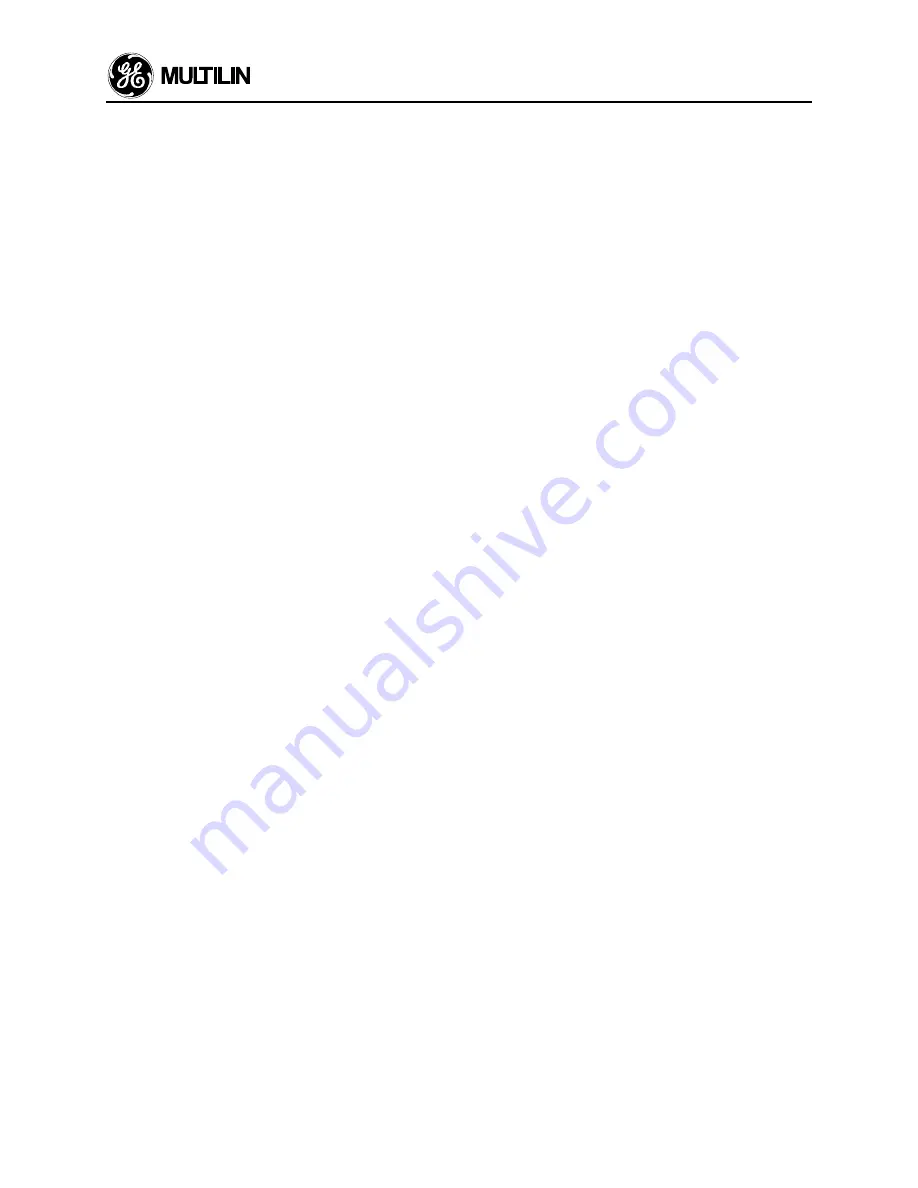
APPENDIX F
F-1
269 Do's and Don'ts Checklist
For proper, orderly and reliable operation of the 269
relay, it is imperative that the steps, recommendations,
and practices listed in the checklist below be adhered
to at all times.
The 269's reliability and proven track record as the best
Motor Protection Relay on the market to date, including
the years that its predecessor the 169 Plus has contrib-
uted, allowed us to compile the following "DO'S and
DON'TS" list that should, if followed, guarantee dura-
ble, reliable and trouble free operation of the 269 Relay
in all medium voltage motor protection applications.
À
269 Grounding
Users are requested to ground the 269 relay to a solid
ground, preferably directly to the main GROUND BUS
at ONE TERMINAL ONLY, terminal #42. Except for the
communications circuitry (which we will discuss later!),
all other internal circuitry in the 269 ties to the same
ground at terminal #42. The benefits of proper ground-
ing of the 269 are numerous, e.g,
l
Elimination of nuisance tripping
l
Elimination of internal hardware failures
l
Reliable operation of the relay
l
Higher MTBE (Mean Time Between Events)
Á
Grounding of Phase and Ground CTs
- All phase and Ground CTs must be grounded. The
potential difference between the CT's ground and the
ground bus should be minimal (ideally zero).
- It is highly recommended that, in addition to the solid
grounding of the ground CT as described above, a
shielded twisted pair be employed especially when
the GE Multilin 2000:1 Ground CT sensor is used.
The reason being the 2000:1 CT is usually used on
high resistance grounded systems where faults are
limited to 200 Amps or less, and the relay is set to
trip instantaneously on low levels of ground current
anywhere between 1 and 10 Amps. 1 to 10 Amp pri-
mary current on the 2000:1 CT translate into very
small signals (0.5 to 5 mA) on the secondary of that
same CT, which is the signal that the 269 relay sees.
Because we are calling upon the 269 relay to detect
even the smallest of signals, we have to make sure
that noise from any other source does not present it-
self to the relay's ground CT terminals.
Â
RTD's
Consult appendix C for the full description of the 269
RTD circuitry and the different RTD wiring schemes
acceptable for the proper operation of the 269. How-
ever, for best results the following recommendations
should be adhered to:
a)
Use a 3 wire twisted, shielded pair to connect
the RTD's from the motor to the 269. The
shields should be connected to the proper
terminals on the back of the 269.
b)
RTD shields are internally connected to the
269 ground (terminal #42) and must not be
grounded anywhere else.
c)
RTD signals can be characterized as very
small, sensitive signals. Therefore, cables car-
rying RTD signals should be routed as much
away as possible from power carrying cables
such as power supply and CT cables.
d)
If, after wiring the RTD leads to the 269, the
RTD Temperature displayed by the Relay is
zero, then check for the following conditions:
1 - shorted RTD
2 - RTD hot and compensation leads are re-
versed, i.e. hot lead in compensation ter-
minal and compensation lead in hot
terminal.
Содержание MULTILIN 269 MOTOR MANAGEMENT RELAY Series
Страница 3: ...TABLE OF CONTENTS ii GLOSSARY ...
Страница 11: ...2 INSTALLATION 2 2 Figure 2 2a Phase CT Dimensions ...
Страница 12: ...2 INSTALLATION 2 3 Figure 2 2b Ground CT 50 0 025 3 and 5 window ...
Страница 13: ...2 INSTALLATION 2 4 Figure 2 2c Ground CT 50 0 025 8 window ...
Страница 14: ...2 INSTALLATION 2 5 Figure 2 2d Ground CT x 5 Dimensions ...
Страница 17: ...2 INSTALLATION 2 8 Figure 2 4 Relay Wiring Diagram AC Control Power ...
Страница 19: ...2 INSTALLATION 2 10 Figure 2 6 Relay Wiring Diagram Two Phase CTs ...
Страница 20: ...2 INSTALLATION 2 11 Figure 2 7 Relay Wiring Diagram DC Control Power ...
Страница 29: ...2 INSTALLATION 2 20 Figure 2 11 269 Drawout Relay Physical Dimensions ...
Страница 30: ...2 INSTALLATION 2 21 Figure 2 12 269 Drawout Relay Mounting ...
Страница 31: ...2 INSTALLATION 2 22 Figure 2 13 269 Drawout Relay Typical Wiring Diagram ...
Страница 34: ...2 INSTALLATION 2 25 Figure 2 16 MPM Mounting Dimensions ...
Страница 35: ...2 INSTALLATION 2 26 Figure 2 17 MPM to 269 Typical Wiring 4 wire Wye 3 VTs ...
Страница 36: ...2 INSTALLATION 2 27 Figure 2 18 MPM to 269 Typical Wiring 4 wire Wye 2 VTs ...
Страница 37: ...2 INSTALLATION 2 28 Figure 2 19 MPM to 269 Typical Wiring 3 wire Delta 2 VTs ...
Страница 38: ...2 INSTALLATION 2 29 Figure 2 20 MPM to 269 Typical Wiring 2 CT ...
Страница 39: ...2 INSTALLATION 2 30 Figure 2 21 MPM Wiring Open Delta ...
Страница 40: ...3 SETUP AND USE 3 1 Figure 3 1 Front Panel Controls and Indicators ...
Страница 74: ...Setpoints Pg 6 3 SETUP AND USE 3 35 13 END OF PAGE SIX END OF PAGE SIX SETPOINT VALUES SETPOINT VALUES ...
Страница 86: ...3 SETUP AND USE 3 47 Figure 3 2 Wiring Diagram for Contactors ...
Страница 87: ...3 SETUP AND USE 3 48 Figure 3 3 Wiring Diagram for Breakers ...
Страница 93: ...3 SETUP AND USE 3 54 Figure 3 5 Standard Overload Curves ...
Страница 102: ...4 RELAY TESTING 4 2 Figure 4 1 Secondary Injection Test Set AC Input to 269 Relay ...
Страница 103: ...4 RELAY TESTING 4 3 Figure 4 2 Secondary Injection Test Set DC Input to 269 Relay ...
Страница 106: ...4 RELAY TESTING 4 6 Figure 4 3 Hi Pot Testing ...
Страница 108: ...5 THEORY OF OPERATION 5 2 Figure 5 1 Hardware Block Diagram ...
Страница 110: ...5 THEORY OF OPERATION 5 4 Figure 5 2 Firmware Block Diagram ...
Страница 112: ...6 APPLICATION EXAMPLES 6 2 Figure 6 1 Thermal Limit Curves ...
Страница 126: ...APPENDIX H H 3 Figure H 1 Excitation Curves Figure H 2 Excitation Curves Method ...
Страница 133: ......
Страница 137: ......
Страница 139: ......
Страница 141: ......
Страница 142: ......