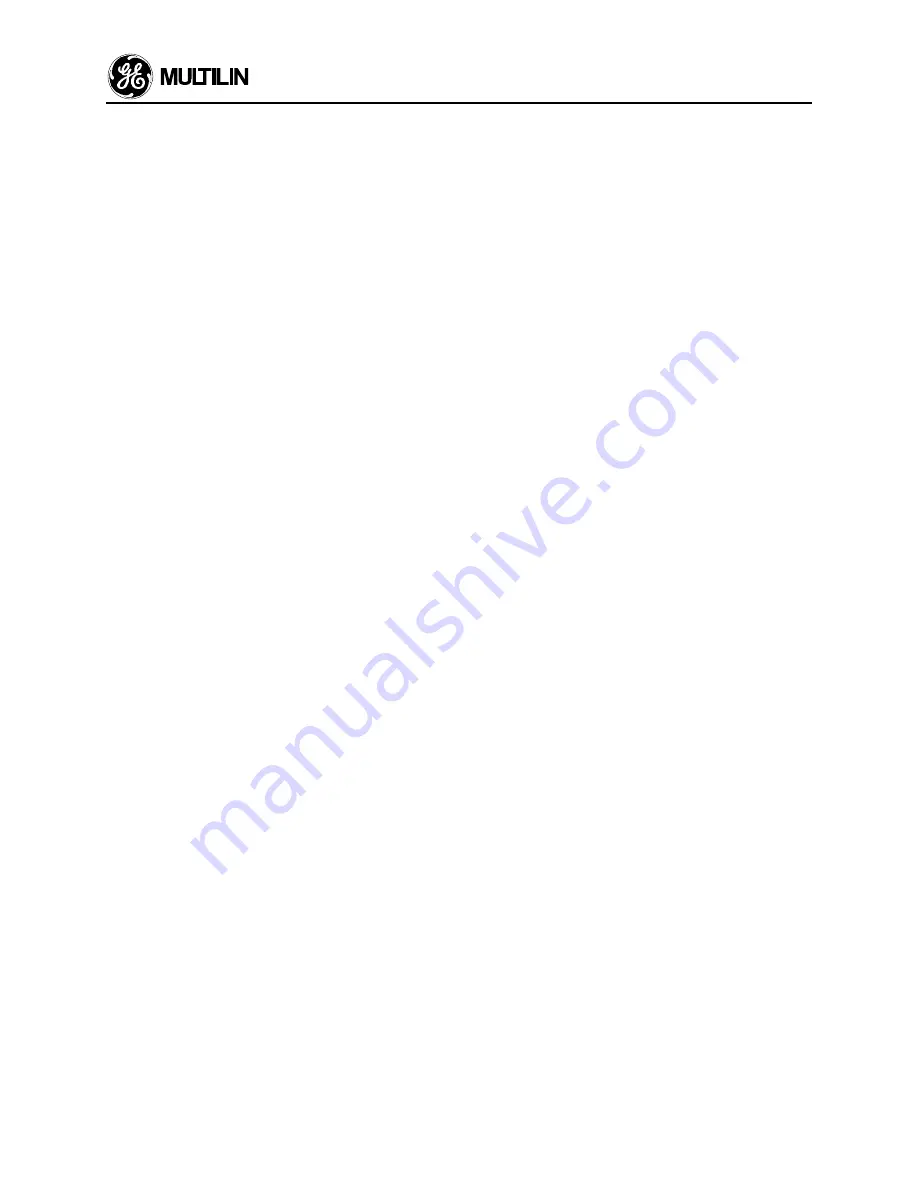
4 RELAY TESTING
4-5
4.6 Power Failure Testing
When the A.C. voltage applied to the 269 relay de-
creases to below about 80 V, all relay L.E.D.s should
become illuminated. If a different supply voltage is be-
ing used (240VAC, 125VDC, 250VDC, 24VDC, or
48VDC) consult the specifications section for power
fail levels. All output relays will also go to their power
down states. To test the memory circuitry of the relay,
remove and then re-apply control power. All stored
setpoints and statistical data should be unchanged.
The displayed lock-out time after an overload trip
should continue to decrease even when control power
is removed.
4.7 Analog Current Output
Using the factory default setpoints to test the analog
current output, a 4-20 mA D.C. ammeter should be
connected between terminals 58 and 59. While viewing
the "HOTTEST STATOR RTD" actual value adjust the
resistance of the simulated stator RTD potentiometers
shown in figure 4-1. A displayed reading of 0 C should
correspond to a 4 mA output. A reading of 200 C
should correspond to an output of 20 mA. The output
should be a linear function of temperature between
these extremes. Similar tests can be performed for the
other output options (thermal capacity used, motor load
as a percentage of full load).
4.8 Routine Maintenance Verification
Once a relay has been properly installed, annual testing
should be performed to check correct operation of the
protection system. Many conditions can be simulated
without creating the actual trip/alarm conditions them-
selves. This is done by changing relay setpoints to
values which will initiate trips and alarms during normal
motor operation. Changed setpoints should be re-
turned to their proper values when tests have been
completed. The Access terminals must be shorted
together to allow setpoint changes. The Emergency
Restart terminals should be shorted together momen-
tarily 5 times before each test to ensure that the relay
thermal memory is fully discharged and starts per hour
counter is fully cleared.
To test relay functions using phase current data, with
the motor running, change the "MOTOR FULL LOAD
CURRENT" setpoint to a value under the actual motor
current. Stop the motor and short the Emergency Re-
start terminals together momentarily to discharge the
thermal memory in the relay. The trip relay should ac-
tivate after a time determined from the overload curve,
amount of unbalance present, and motor RTD tem-
perature. The time to trip at a given overload level
should never be greater than the time on the overload
curve. Current unbalance and high stator RTD tem-
peratures will cause this time to be shorter (if the RTD
bias and/or U/B bias functions are enabled).
Larger overloads, representing short circuits or me-
chanical jams, can be simulated by changing the
"MOTOR FULL LOAD CURRENT" setpoint to a value
much lower than the actual motor phase current.
Unbalance trip or alarm conditions can be simulated by
changing the Unbalance Trip or Alarm Level setpoints
to values below the actual unbalance present at the
motor terminals.
Other trip or alarm conditions using ground fault cur-
rent data and RTD temperature data can be simulated
using the procedures outlined in the previous sections.
To test the operation of the 269 output relays and the
switchgear connected to them the "EXERCISE: XXXXX
RELAY" setpoint in page 6 of SETPOINTS mode can
be used. The motor must be stopped in order for this
function to operate. Any or all of the output relays can
be toggled using this setpoint.
To test the analog output current hardware the
"ANALOG OUT FORCED TO: XXXXXX SCALE" set-
point can be used. The output current can be forced to
"ZERO", "MID", or "FULL" scale. This feature can be
used to test the calibration of the 269 as well as the
operation of any device through which the current is
flowing. The motor must be stopped in order for this
function to operate.
To test the operation of devices connected to the Ac-
cess terminals, Emergency Restart terminals, and Ex-
ternal Reset terminals the "STATUS" setpoint can be
used. This is in page 6 of SETPOINTS mode. This
line will give the status of each pair of terminals as ei-
ther "OPEN" or "SHORT".
4.9 Dielectric Strength (Hi-Pot) Test
The 269 relay is Hi-Pot tested at the factory for 1 sec-
ond at 2200 VAC in order to verify its dielectric
strength. See Fig 4.3 for the test procedure.
If the 269 is of the Drawout version, Hi-Pot testing of
wires in the switchgear is possible without the need to
remove wires attached to the drawout case terminals.
However, the 269 in its cradle should be withdrawn
from the case before Hi-Pot testing starts. Failure to do
so may result in internal damage to the 269.
Содержание MULTILIN 269 MOTOR MANAGEMENT RELAY Series
Страница 3: ...TABLE OF CONTENTS ii GLOSSARY ...
Страница 11: ...2 INSTALLATION 2 2 Figure 2 2a Phase CT Dimensions ...
Страница 12: ...2 INSTALLATION 2 3 Figure 2 2b Ground CT 50 0 025 3 and 5 window ...
Страница 13: ...2 INSTALLATION 2 4 Figure 2 2c Ground CT 50 0 025 8 window ...
Страница 14: ...2 INSTALLATION 2 5 Figure 2 2d Ground CT x 5 Dimensions ...
Страница 17: ...2 INSTALLATION 2 8 Figure 2 4 Relay Wiring Diagram AC Control Power ...
Страница 19: ...2 INSTALLATION 2 10 Figure 2 6 Relay Wiring Diagram Two Phase CTs ...
Страница 20: ...2 INSTALLATION 2 11 Figure 2 7 Relay Wiring Diagram DC Control Power ...
Страница 29: ...2 INSTALLATION 2 20 Figure 2 11 269 Drawout Relay Physical Dimensions ...
Страница 30: ...2 INSTALLATION 2 21 Figure 2 12 269 Drawout Relay Mounting ...
Страница 31: ...2 INSTALLATION 2 22 Figure 2 13 269 Drawout Relay Typical Wiring Diagram ...
Страница 34: ...2 INSTALLATION 2 25 Figure 2 16 MPM Mounting Dimensions ...
Страница 35: ...2 INSTALLATION 2 26 Figure 2 17 MPM to 269 Typical Wiring 4 wire Wye 3 VTs ...
Страница 36: ...2 INSTALLATION 2 27 Figure 2 18 MPM to 269 Typical Wiring 4 wire Wye 2 VTs ...
Страница 37: ...2 INSTALLATION 2 28 Figure 2 19 MPM to 269 Typical Wiring 3 wire Delta 2 VTs ...
Страница 38: ...2 INSTALLATION 2 29 Figure 2 20 MPM to 269 Typical Wiring 2 CT ...
Страница 39: ...2 INSTALLATION 2 30 Figure 2 21 MPM Wiring Open Delta ...
Страница 40: ...3 SETUP AND USE 3 1 Figure 3 1 Front Panel Controls and Indicators ...
Страница 74: ...Setpoints Pg 6 3 SETUP AND USE 3 35 13 END OF PAGE SIX END OF PAGE SIX SETPOINT VALUES SETPOINT VALUES ...
Страница 86: ...3 SETUP AND USE 3 47 Figure 3 2 Wiring Diagram for Contactors ...
Страница 87: ...3 SETUP AND USE 3 48 Figure 3 3 Wiring Diagram for Breakers ...
Страница 93: ...3 SETUP AND USE 3 54 Figure 3 5 Standard Overload Curves ...
Страница 102: ...4 RELAY TESTING 4 2 Figure 4 1 Secondary Injection Test Set AC Input to 269 Relay ...
Страница 103: ...4 RELAY TESTING 4 3 Figure 4 2 Secondary Injection Test Set DC Input to 269 Relay ...
Страница 106: ...4 RELAY TESTING 4 6 Figure 4 3 Hi Pot Testing ...
Страница 108: ...5 THEORY OF OPERATION 5 2 Figure 5 1 Hardware Block Diagram ...
Страница 110: ...5 THEORY OF OPERATION 5 4 Figure 5 2 Firmware Block Diagram ...
Страница 112: ...6 APPLICATION EXAMPLES 6 2 Figure 6 1 Thermal Limit Curves ...
Страница 126: ...APPENDIX H H 3 Figure H 1 Excitation Curves Figure H 2 Excitation Curves Method ...
Страница 133: ......
Страница 137: ......
Страница 139: ......
Страница 141: ......
Страница 142: ......