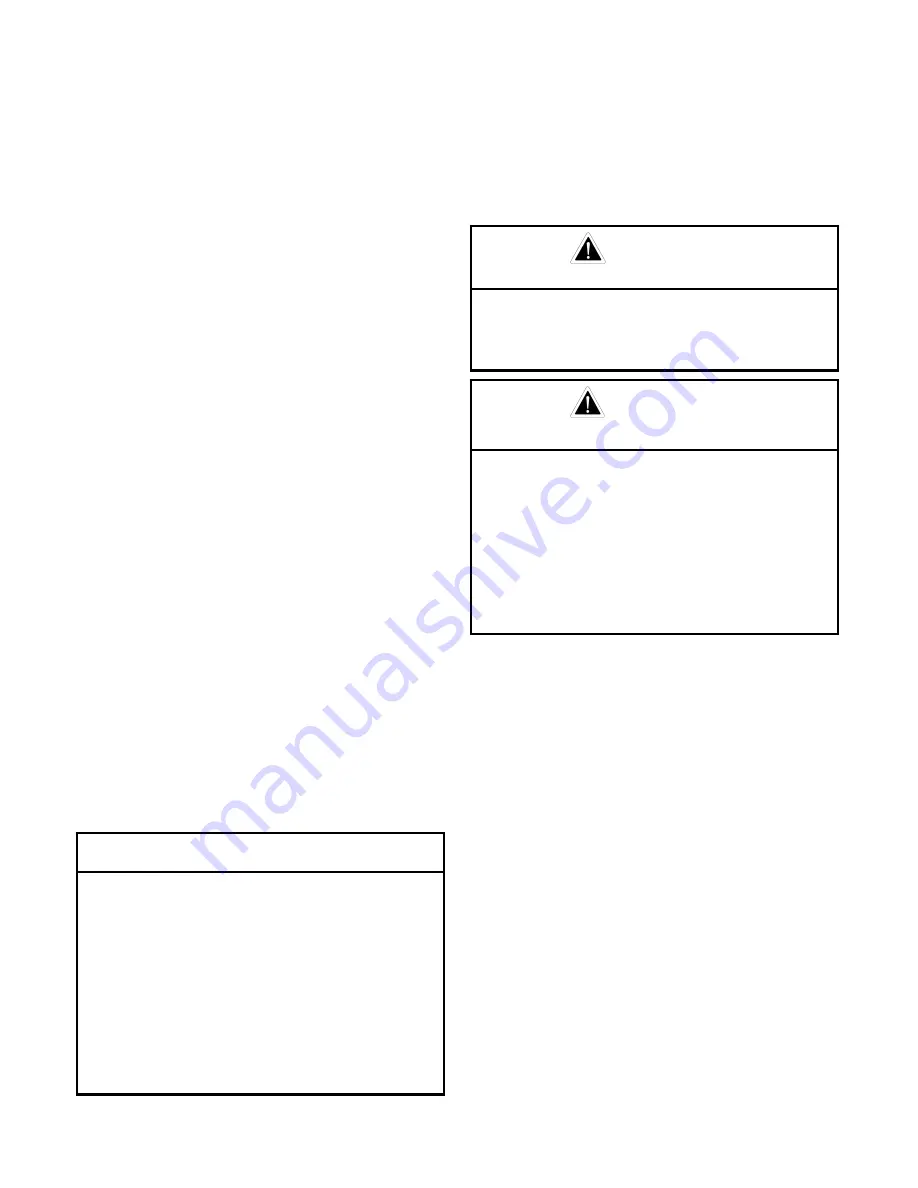
3-1-618 Page 12
Use only Gardner Denver replacement plungers, as
many other brands do not have the material quality or
fine surface finish needed to provide long plunger and
packing life.
A plunger, packing and stuffing box should be
installed in the pump as an assembly (see “Stuffing
Boxes,” above). After this assembly has been
completed, take the plunger coupling halves that had
been kept as a matched set from the time of
disassembly, and install the set using the screws and
nuts. If one coupling half has been damaged, do not
use a new half with a used half. Instead, use a
complete new coupling set. Tighten the coupling
evenly so the gap between the halves is the same on
both ends.
PLUNGER PACKING
-The stuffing boxes are packed
with nonadjustable lip type packing for low pressure,
general service applications. Self adjusting packing
in various lip styles and braided configurations is also
offered for higher pressure and/or special service
conditions. Lubrication is required for all lip style and
most braided style packings. Packing lubricating oil
types and required flow rates are discussed in
“Packing Lubricator,”
Before installing the packing, clean the stuffing box
and check the bore for nicks, scratches and wear. A
damaged box should be replaced to avoid early
packing failure. Inspect all metal and/or plastic
packing rings, spacers and bushings to insure they
are clean and free of nicks and burrs. Always install
new packing rings in complete sets. Coat all packing
parts with light oil. DO NOT USE GREASE. Install
the packing and components in the stuffing box in the
same order as the parts were removed. When using
lip style packing, be sure the lips of the sealing rings
face the pressure (toward the fluid end). Coat the
plunger with oil and slide it into the packing.
Install stuffing box, plunger and packing as an
assembly on the fluid cylinder, using the procedure
described in the “Stuffing Boxes,”
When the nonadjustable packing is used, tighten the
gland firmly with a 24 inch section of one half inch
pipe placed over a lock pin, which has been inserted
in a lock pin hole in the gland. When using self-
adjusting packing, tighten the gland nut firmly, after
assembling it metal-to-metal with the stuffing box. Do
not over tighten the nut, as the threads or lock pin
holes could be damaged.
When using the nonadjustable packing, operate the
pump for two (2) or three (3) hours under pressure,
stop the pump, relieve the pressure and retighten the
glands to prevent packing movement.
Regardless of the style packing used, keep lock pins
in place to prevent the glands from backing loose.
Several other types of packing may be used in
standard stuffing boxes. Installation procedures for
other packing may vary from the above. Additional
information can be obtained by contacting Gardner
Denver Customer Service.
PACKING LUBRICATOR
- A force-feed plunger
packing lubricator is required for most packings and
is available as optional equipment. The lubricator is
mounted on a bracket over the frame and is driven by
a ratchet drive off the plunger coupling. Oil is
delivered to the tapped opening in each stuffing box
through steel tubing. The lubricator is equipped with a
check valve at each stuffing box connection.
Use rock drill oil for normal conditions and steam
cylinder oil for high temperature fluids. Select an oil
with the proper pour point for the ambient
temperature. Some acceptable oils are listed in the
chart on p16
NOTICE
This procedure details that the gland
should not be threaded on the stuffing box
before the box is assembled on the fluid
cylinder.
This assembly sequence is recommended
since on most pump models the gland will
interfere with the wrench and/or socket
used to tighten the fluid cylinder stud nuts,
particularly nuts on the bottom side of the
box.
DANGER
Do not attempt to adjust packing while
pump is in operation to avoid personal
injury or death from moving parts.
DANGER
Regardless of the packing used, the gland
must be engaged by at least (3) threads to
hold the pump discharge pressure. An
improperly tightened gland could cause
personal injury, death and/or equipment
damage. This can occur either through
direct contact with the pressurized flow or
by contact with objects the fluid stream
propels.