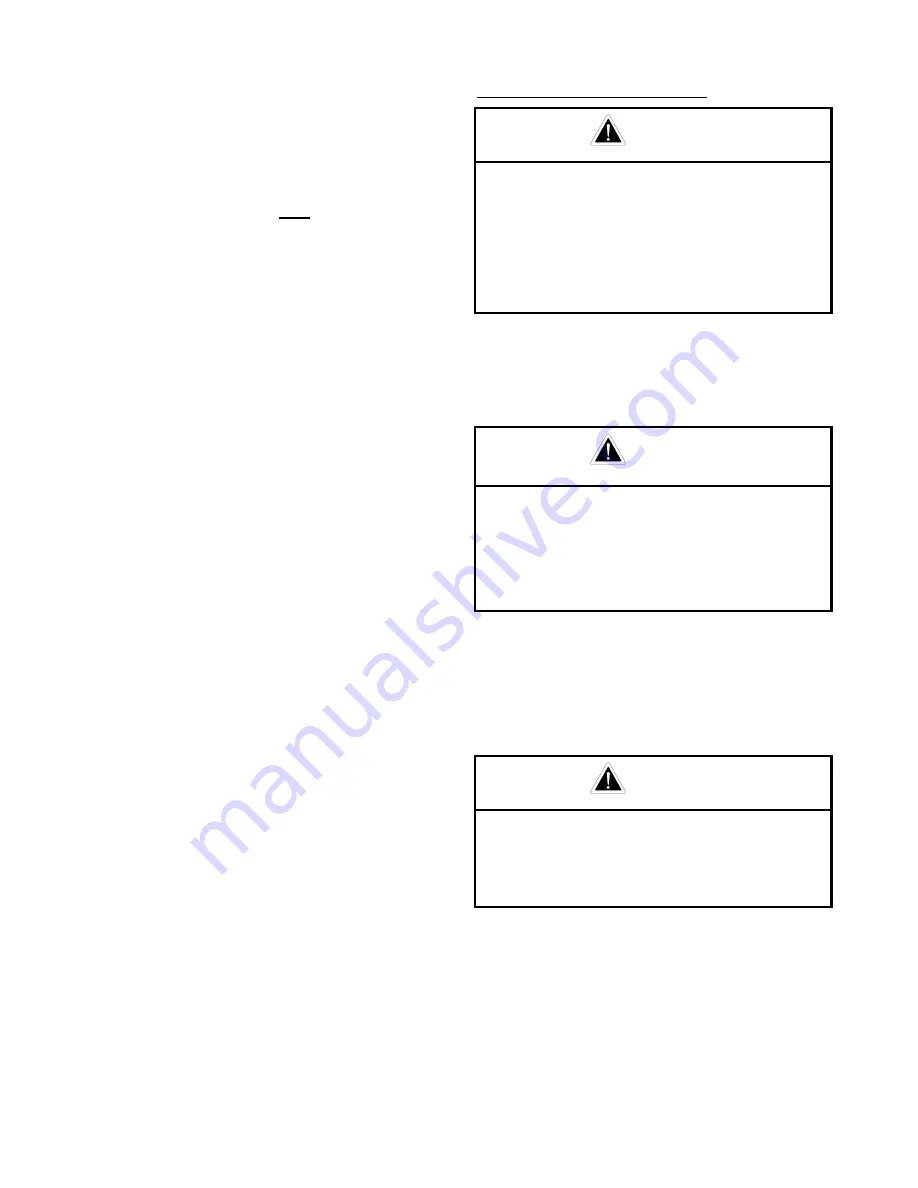
3-1-618 Page 3
Fully assembled pumps and pump package units
are heavy and should only be moved using the
specified lifting lugs or attachments.
Many individual components have lifting eyes
or lugs which must not be used to lift
assemblies, as they are designed to bear the
weight of the component only
.
Before lifting the individual component check to
insure the lifting attachment is firmly secured to the
component with undamaged, properly torqued
fasteners, sound welds, or other secure
attachments. Examine the lifting eyes, lugs, slots,
holes or other projections to insure they are not
cracked, otherwise damaged or badly worn. The
repair of existing or addition of new welded lifting
eyes, lugs or other projections should only be
performed by experienced, qualified welders.
Package units should be lifted with spreaders
connected to the lifting attachments normally built
into the package unit support skid. Packages too
large to lift fully assembled should be separated
into smaller loads.
For these smaller loads the lifting devices should
be fastened to the lifting attachments normally built
into the individual motor, engine, pump or
transmission/torque converter, or their separate
support skids.
When lifting subassembled components, for
example a suction stabilizer attached to suction
piping or a discharge pulsation dampener attached
to a strainer cross and piping, use special lifting
slings designed to safely support the combined
weight of the components.
If a crane or hoist is being used to lift large
components or assemblies, one or more persons
should assist the operator from the ground with
guide lines attached to the equipment being moved
to properly position it and prevent uncontrolled
movement.
When you start to lift a pump, package unit,
subassemblies or individual components and you
observe the equipment is tilting, or appears
unbalanced, lower the equipment and adjust the
lifting device to eliminate these improper lifting
conditions before proceeding to move the
equipment.
It is poor practice and dangerous to allow the
equipment to pass over or close to your body or
limbs. Be prepared to move quickly out of danger if
equipment starts to fall, slip or move unexpectedly
toward you.
PRESSURIZED PUMP SYSTEMS
Operating a pump against a blocked or restricted
discharge line can produce excessive pressures in
the entire discharge system, which can damage or
burst discharge system components.
The relief valve should be placed in the flowing
discharge line and not at the opposite end of the
discharge manifold in a dead end connection. The
dead end may become clogged with solid material
carried in the fluid, which could prevent proper relief
valve operation.
Make sure the pressure relief valve is installed so
any pressurized relief discharge from the valve is
directed away from possible contact with people or
equipment. The relief valve must be set to relieve
at a pressure equal to or below the maximum
pressure values shown on the pump data plate.
However, if a component is used in the discharge
system with a lower rated pressure capability than
that listed on the pump data plate, the pressure
DANGER
Fluids under high pressure can possess
sufficient energy to cause personal injury,
death and/or equipment damage either
through direct contact with escaping fluid
streams or by contact with loose objects
the pressurized fluid propels.
DANGER
Never operate a pump without a properly
sized pressure relief valve located in the
flowing discharge line immediately
adjacent to the pump discharge
connection.
DANGER
Never place a shut-off valve or any other
component between the pump discharge
connection and the pressure relief valve.