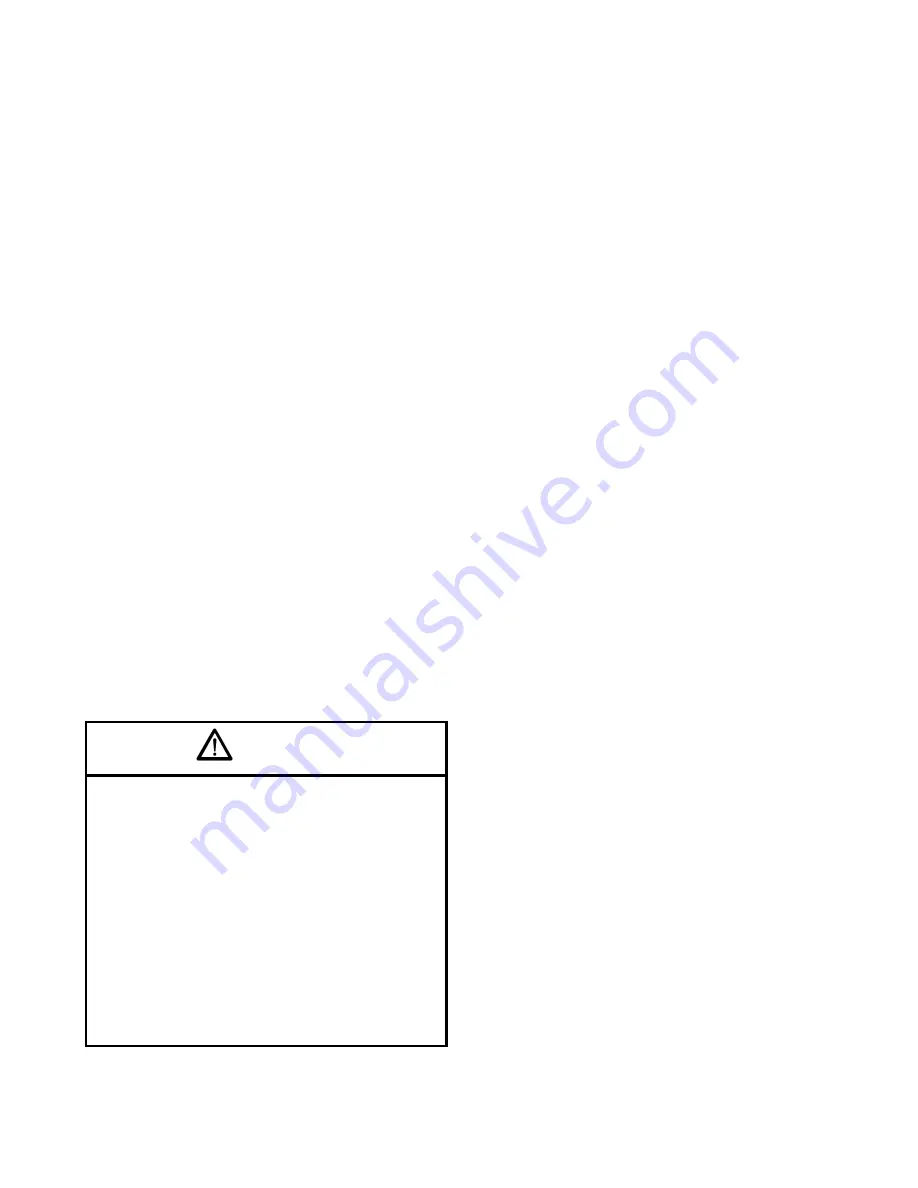
3-1-618 Page 11
Before installing a valve, inspect the valve seats and
fluid cylinder valve deck tapers to insure they re not
scratched, nicked or otherwise damaged. Replace
any seat found damaged and have any damaged
deck tapers re-machined. NOTE: Do not coat the
tapers with any kind of lubricant or coating before
assembly.
Drive the seat into the taper using a four-pound (1.8
kilogram) hammer striking either a wood block
(covering the full upper surface of the seat) or one of
the factory option valve seat drivers that thread onto
the various style valve seats. One sharp blow on the
block or the rod end of the driver should be sufficient
for seating. If the seat jumps up when it is struck,
take it out and inspect both the seat and the deck
tapers. They must be clean, dry and undamaged
before a second attempt is made to install the seat.
Again use only one sharp blow on the block or driver
after dropping the seat into the taper. Excessive
pounding could loosen or damage the seat.
Use caution when installing the valve cover to
prevent “pinching” of gaskets. The gasket must be
installed with the chamfer facing up. Tighten the
valve cover nuts to proper torque as shown in
“Rebuilding Data”, page 26.
STUFFING BOXES
- Stuffing boxes made from
different materials and in several sizes can be
matched with various fluid cylinders used on the
pumps.
When servicing a stuffing box, plunger or packing,
start by removing the plunger to extension rod
coupling. Keep the coupling halves together as sets.
Do not intermix halves.
Continue to rotate the crankshaft to pull the extension
rod away from the plunger as far as it will go.
Remove the gland nut and the all the fluid cylinder
stud nuts. Remove the fluid cylinder assembly from
the front of the frame. Next remove the stuffing box
assemblies from the frame. Lay the stuffing box
assembly on a work bench and slide the plunger and
packing out of the stuffing box.
When replacing the stuffing box, plunger and packing
assembly, the above procedure is reversed.
However, first inspect the stuffing box bore for
scratches, wear or other defects. Clean and check
the stuffing box face, gasket groove and outside
diameter that pilots into the frame, to insure they are
free of defects, burrs and dirt. Clean out any burrs,
dirt and rust in the stuffing box pilot bores in the
frame. Install the packing in the box. Place a new
gasket in the stuffing box groove. The gasket
chamfered edge must face out to prevent gasket
pinching when the stuffing box and cylinder surfaces
are pressed together. Place the stuffing box
assemblies into the frame bores, then install the fluid
cylinder onto the frame. Align the counterbores in the
fluid cylinder with the stuffing box pilots.
If the stuffing boxes do not enter the frame easily, do
not hit them with any type of hammer, as you may
damage the boxes or dislodge the gasket from the
groove. Instead, remove the boxes and recheck the
frame bores for dirt or rust build-up and the stuffing
box pilots for dirt or damage. Install and torque the
fluid cylinder stud nuts to the value listed on page 27
Alternately tighten the nuts diagonally across from
each other to insure the gaskets are drawn up evenly.
Install the gland bushing and gland on the box.
PLUNGERS
- Plungers with colmonoy, ceramic or
tungsten carbide wear surfaces are normally used,
depending on the service conditions. However, other
materials can be supplied for special applications.
To remove a plunger, remove the coupling which
holds the plunger to the crosshead extension and
remove the gland nut.
Next remove the suction valve cover, and shove the
plunger through the packing and out the suction valve
cover opening. To assemble, reverse the above
procedure.
Before installing a new plunger, or reinstalling a used
plunger, check for scratches, pits, nicks or a rough
finish on the plunger wear surface. Inspect the
mating pilots and ends of both the plunger and
extension rod for burrs and dirt. Check to make sure
the extension rod pilot is not broken or damaged. A
broken pilot could also be lodged in the plunger pilot
hole. Replace any damaged parts. Burrs, other
damage, or dirt between the plunger and extension
rod ends and pilots can misalign a plunger and lead
to early plunger and packing failure.
WARNING
After removing the plunger to crosshead
extension coupling, do not use a
screwdriver or cold chisel to separate the
extension and plunger flanges, as burrs
may be formed which would cause
misalignment on reassembly. Instead,
rotate the eccentric slightly. If the parts
do not separate, carefully slip a pipe
wrench around the plunger neck and use a
pulling and rotating motion to separate the
plunger from the extension rod. Use
caution to avoid damaging the plunger
wear surface.