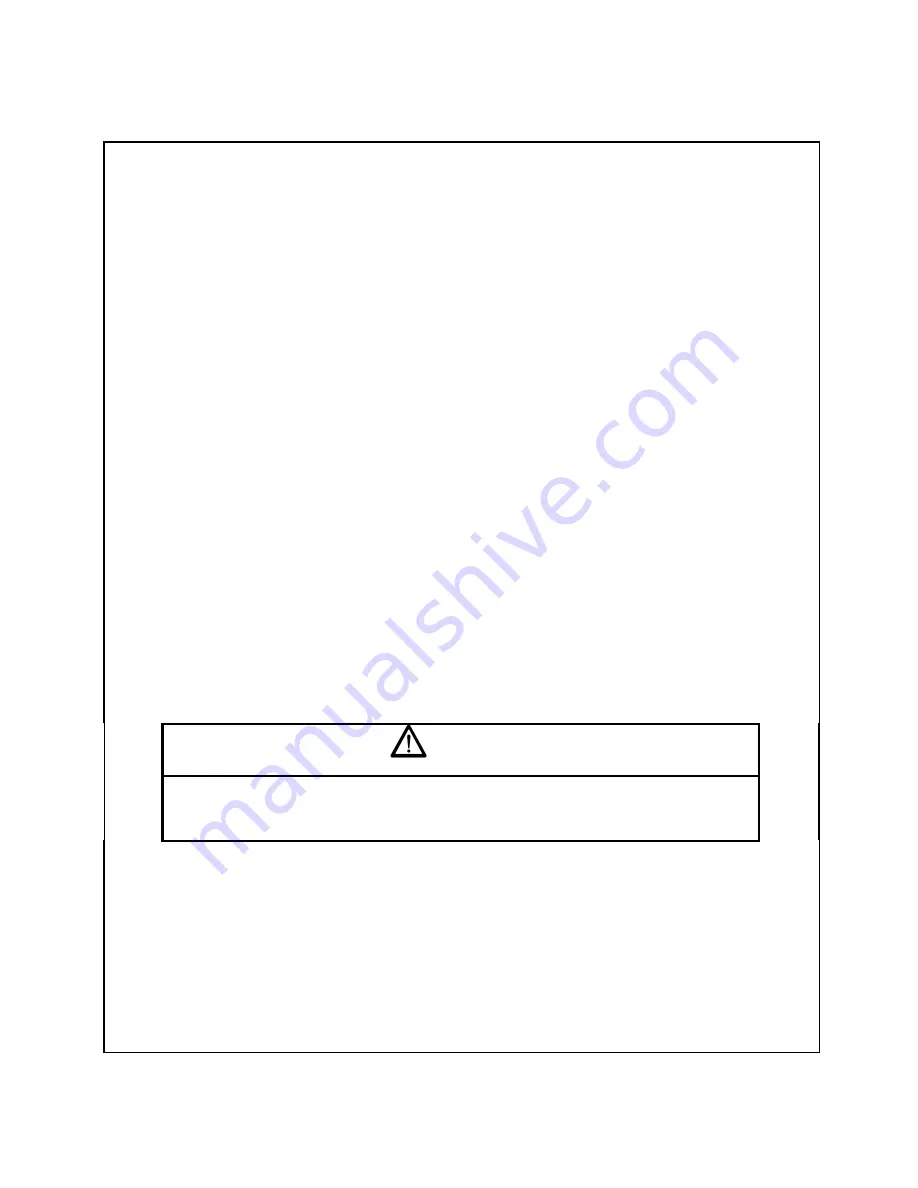
3-1-618 Page 16
CRANKCASE OIL REQUIREMENTS
API-GL5 Oil Grade
Oil Grade
Ambient
Temperature
Crankcase Operating
Oil Temperature*
Minimum Start-Up
Oil Temperature
75W – 90
-20º F TO 60º F
60º F TO 140º F
20º F
(-29º C TO 16º C)
(16º C TO 60 º C)
(-7º C)
80W – 140
10º F TO 100º F
90º F TO 180º F
50º F
(-12º C TO 38º C)
(32º C TO 82º C)
(10º C)
80
-10º F TO 45º F
70º F TO 125º F
30º F
(-23º C TO 7º C)
(21º C TO 52º C)
(-1º C)
90
20º F TO 80º F
100º F TO 160º F
60º F
(-7º C TO 27º C)
(38º C 59 71º C)
(16º C)
140
50º F TO 115º F
130º F TO 195º F
80º F
(10º C TO 46º C)
(54º C TO 90º C)
(27º C)
* An 80º F (27º C) crankcase oil temperature rise over ambient air temperature is typical for the pumps
covered by this manual when operating at or near rated horsepower.
Oil viscosity must not exceed 7000 SSU at start-up and must be between 1500 SSU and 200 SSU while
operating, regardless of the oil temperature or grade used. A crankcase heater and/or an oil heat
exchanger may be needed to meet these requirements.
Crankcase capacity is 12 gallons (45.4 liters).
WARNING
Failure to follow these lubrication requirements will void the warranty.
Some operating conditions and/or oil brands produce excessive oil foaming, even when the specified
GL-5 oils containing the antifoaming additives are used. Oil foaming can cause pump damage, as oil
bubbles will not lubricate moving parts properly. If significant oil foaming occurs, contact Gardner Denver
Marketing or Service for the current factory recommended defoamant to be added to the lubricating oil.
When it is not possible to contact Gardner Denver people, a small amount of kerosene added to the oil
will usually reduce foaming. One half of a fluid ounce of kerosene added to each gallon of oil should be
sufficient to control foaming. The use of larger amounts of kerosene per gallon of oil will reduce the oil
viscosity, which could result in rapid pump wear and failure.