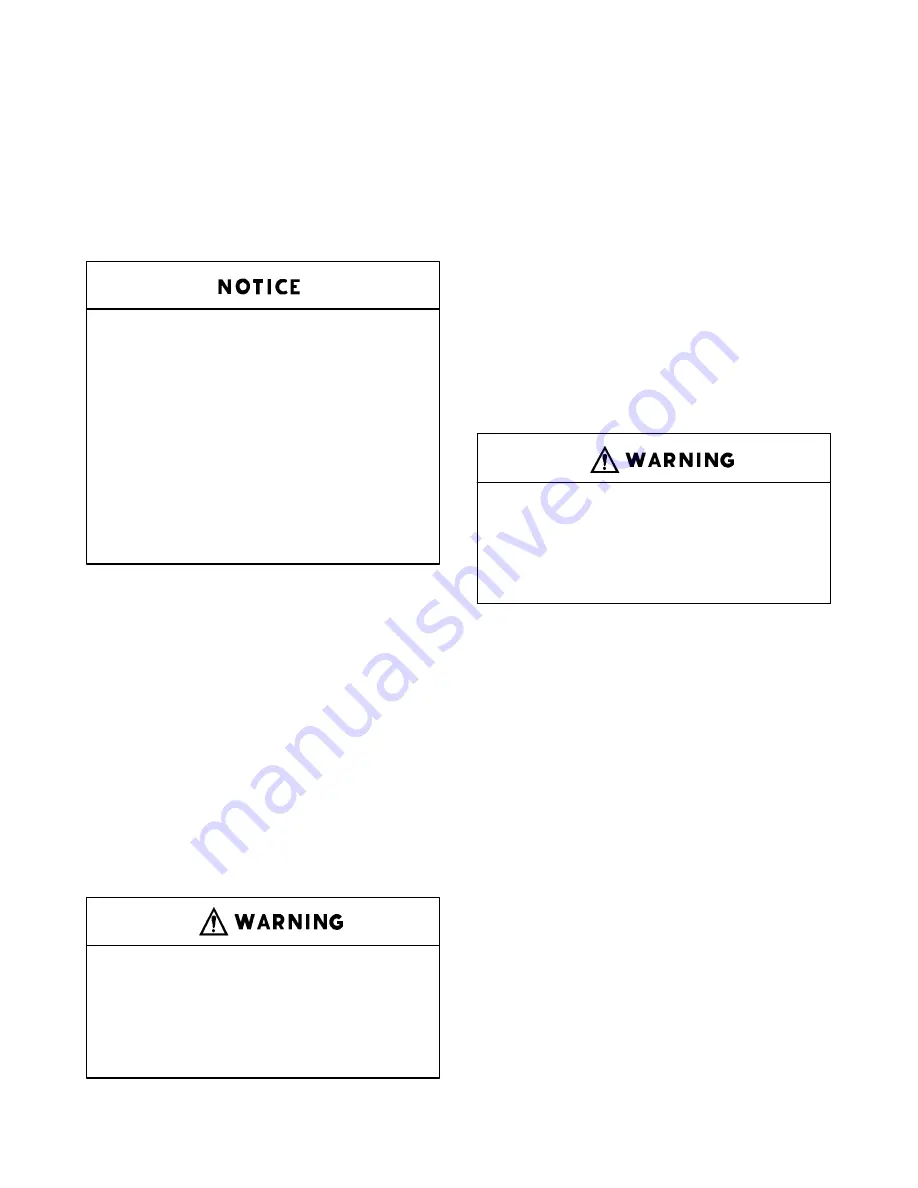
13–8–606 Page 23
back to the normal setup mode. The display
should read “0” pressure in the left window,
and –––– current sump temperature in the
right window.
Step 12: Stop the compressor and disconnect, tag
and lockout the power supply to the starter.
Step 13: Move the circuit board slide switch back to
the “set” position (right). You may now pro-
ceed with normal start up procedure.
A.
To readjust, the slide switch
must be in the “+” position.
B.
If procedure is repeated, the
transducer zero operation may
be bypassed by not pressing
“Stop–Reset” while the dashes
(––– –––) are displayed.
C.
Transducer must be zeroed only
while at zero “0” pressure, or in-
valid shutdowns may occur.
LEAD–LAG OPERATION OF TWO COMPRES-
SORS – The Auto–Sentry S controller provides the ca-
pability of true lead–lag operation without the need to
purchase any additional equipment and without compli-
cated interconnecting wiring.
Follow these steps to operate two compressors in a
lead–lag arrangement:
Step 1:
Program load and unload pressure setpoint
on both units to the same value. For exam-
ple: Compressor “A” load at 92 PSI (6.3
Bars); unload at 100 PSI (6.9 Bars). Com-
pressor “B” load at 92 PSI (6.3 Bars); unload
at 100 PSI (6.9 Bars). See page 21, this sec-
tion, for complete information on program-
ming the setpoints.
Operation at excessive discharge air
pressure can cause personal injury or
damage to equipment. Do not set un-
load pressure above the maximum
stamped on the unit nameplate.
Step 2:
Operate one compressor in the “Auto Lead”
mode. This compressor will now be the
“Lead” or “Base Load” compressor.
Step 3:
Operate the second compressor in the “Auto
Lag” mode. This compressor will now be the
“lag” or “trim” compressor. It will automatical-
ly be brought on line, if required, by a large air
demand. After the demand is satisfied, the
lag unit will unload, time out and stop, ready
to start again when needed.
Step 4:
Periodically reverse the roles of the units by
changing each unit’s mode of operation from
“Auto Lead” to “Auto Lag” and vice versa. By
using the hourmeters on the control panel to
schedule the mode changes, the operating
hours can be kept as close as possible,
equalizing machine wear and minimizing
maintenance costs.
Automatic restarting or electrical
shock can cause injury or death.
Open, tag and lockout main discon-
nect and any other circuits before
servicing the unit.
Subtractive Pilot (Modulating Feature) – The subtrac-
tive pilot is an adjustable, spring–loaded diaphragm
valve that controls pressure in relation to the upstream
(discharge) pressure.
The downstream pressure is maintained equal to the
upstream pressure minus a constant which is adjust-
able. In the example shown in FIGURE 4–5, page 24,
the downstream pressure equals the upstream pres-
sure minus 95 psi (6.6 Bars). When the upstream
pressure rises to 100 psig (6.9 Bars), the downstream
pressure rises to 5 psig (.3 Bar). This 1 to 1 psi (Bar)
rise is constant above the set point.
Below the set point, the valve seat is closed and the
downstream pressure is vented. In the example of
FIGURE
4–5, page 24, downstream pressure is
vented below 95 psig (6.6 Bars).
FIGURE 4–6, page 24, shows a schematic cross sec-
tion of the subtractive pilot with the valve seat closed
and downstream line vented. FIGURE 4–7, page 24,
shows the pilot with valve seat open, holding a down-
stream pressure which is adjustable with the screw. In
this position it is normal for the valve to continually
bleed air through the small vent hole in the bowl.
Содержание EDF-KB
Страница 14: ...13 8 606 Page 6 DECALS 206EAQ077 212EAQ077 218EAQ077 211EAQ077 207EAQ077...
Страница 15: ...13 8 606 Page 7 DECALS 216EAQ077 217EAQ077 222EAQ077 221EAQ077 208EAQ077...
Страница 34: ...13 8 606 Page 26 FIGURE 4 10 WIRING DIAGRAM FULL VOLTAGE DUAL CONTROL 208EDF546 Ref Drawing...
Страница 36: ...13 8 606 Page 28 FIGURE 5 1 FLOW DIAGRAM 204EDF797 Ref Drawing...
Страница 58: ......