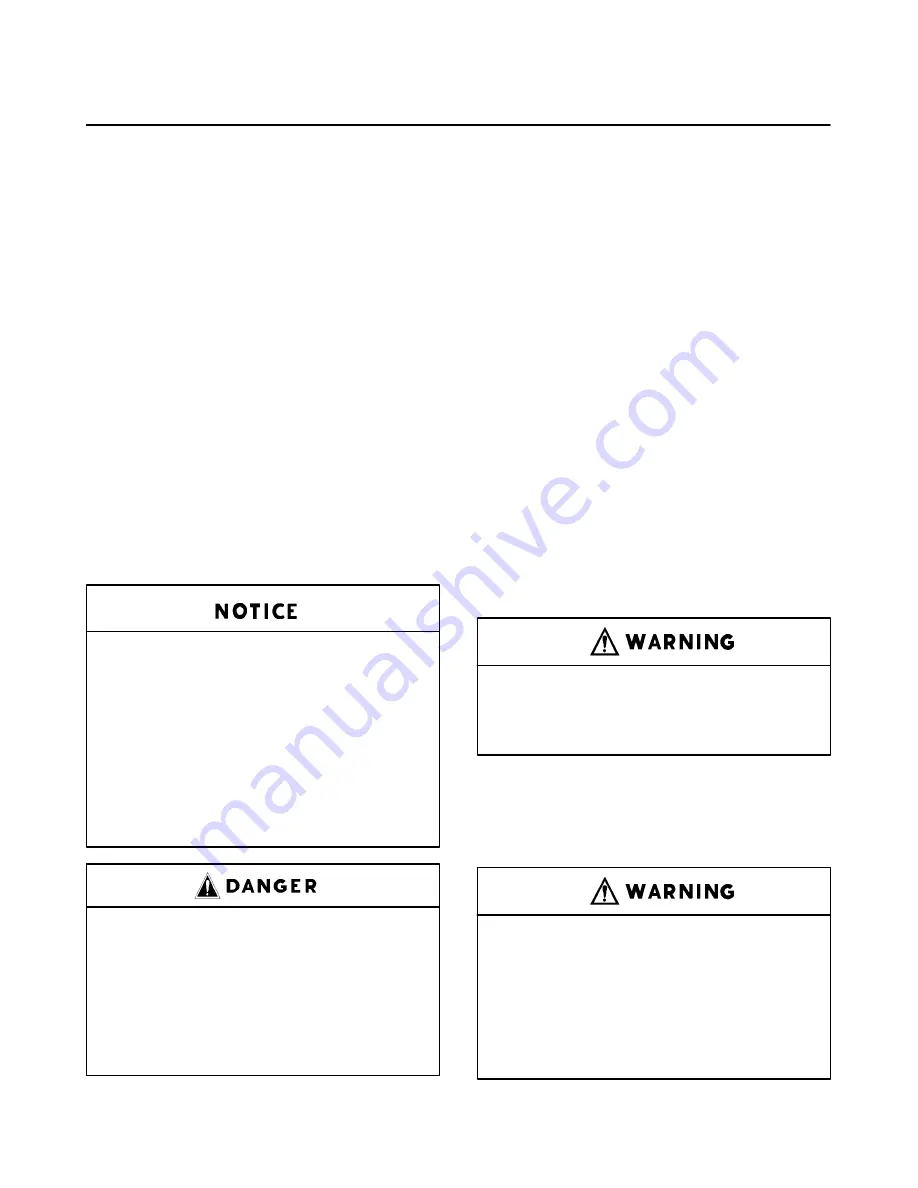
13–8–606 Page 15
SECTION 3
STARTING & OPERATING PROCEDURES
PRESTART–UP INSTRUCTIONS – A new unit as re-
ceived from the factory has been prepared for shipping
only. Do not attempt to operate the unit until checked
and serviced as follows:
1.
Compressor Oil – Check the oil level in the reser-
voir. Add oil only if the oil level gauge reads in the
red “ADD OIL” range. Do not mix different type
oils. The unit is shipped filled with Gardner Denver
AEON
t
4000 Lubricating Coolant which is suit-
able for the first 6000 hours under normal operat-
ing conditions. AEON
t
4000 is generally suitable
for use up to 6000 hours service life, provided the
lubricant is monitored by periodic analysis.
REPLACE OIL FILTER EVERY 1000 HOURS.
Initial fill, or filling after a complete draining of the
system, may show the oil level above the FULL
mark (the center of the gauge). After start–up, the
oil level will drop and fluctuate as the machine
runs. To check for proper oil level, shut off the ma-
chine and allow the foam to settle out. If neces-
sary, add oil to bring the level to the FULL mark.
See FIGURE 1–3, page 2.
Regular maintenance and replace-
ment at required intervals of the oil fil-
ter, air filter and air–oil separator is
necessary to achieve maximum ser-
vice and extended drain intervals of
AEON
t
4000 petroleum base lubri-
cant. Use only genuine Gardner Den-
ver filters designed and specified for
this compressor.
Before removing the oil filler plug,
always stop the unit and release air
pressure, tag and lockout the power
supply to the starter. Failure to
release pressure or properly dis-
connect the power may result in
personal injury or death.
During unloaded operation and after shutdown,
the system will partially drain back into the oil res-
ervoir and the oil level may read higher than when
operating on load. DO NOT DRAIN OIL TO COR-
RECT; on the next loaded cycle or start, oil will
again fill the system and the gauge will indicate the
operating level.
2.
Air Filter – Inspect the air filter to be sure it is clean
and tightly assembled. Refer to Section 6, “Air Fil-
ter,” page 40, for complete servicing instructions.
Be sure the inlet line, if used, is tight and clean.
3.
Coupling – Check all bolts and cap screws for
tightness. See Section 7, page 42.
4.
Piping – Refer to Section 2, “Installation,” page
8, and make sure piping meets all recommenda-
tions.
5.
Electrical – Check the wiring diagrams furnished
with the unit to be sure it is properly wired. See
FIGURE 4–10, page 26, for general wiring dia-
grams and Section 2, page 8 for installation
instructions.
6. Grounding – The unit must be properly grounded
according to Section 250 of the National Electrical
Code.
Failure to properly ground the com-
pressor package could result in con-
troller malfunction.
7.
Rotation – Check for correct motor rotation using
“JOG MODE.” Compressor drive shaft rotation
must be clockwise standing facing the compres-
sor coupling. See Section 4, page 22, Step 8.
Operation with incorrect motor rota-
tion can damage equipment and
cause oil eruption from the compres-
sor inlet. When checking motor rota-
tion, induce minimum rotation (less
than one revolution if possible). Nev-
er allow motor to reach full speed.
Содержание EDF-KB
Страница 14: ...13 8 606 Page 6 DECALS 206EAQ077 212EAQ077 218EAQ077 211EAQ077 207EAQ077...
Страница 15: ...13 8 606 Page 7 DECALS 216EAQ077 217EAQ077 222EAQ077 221EAQ077 208EAQ077...
Страница 34: ...13 8 606 Page 26 FIGURE 4 10 WIRING DIAGRAM FULL VOLTAGE DUAL CONTROL 208EDF546 Ref Drawing...
Страница 36: ...13 8 606 Page 28 FIGURE 5 1 FLOW DIAGRAM 204EDF797 Ref Drawing...
Страница 58: ......