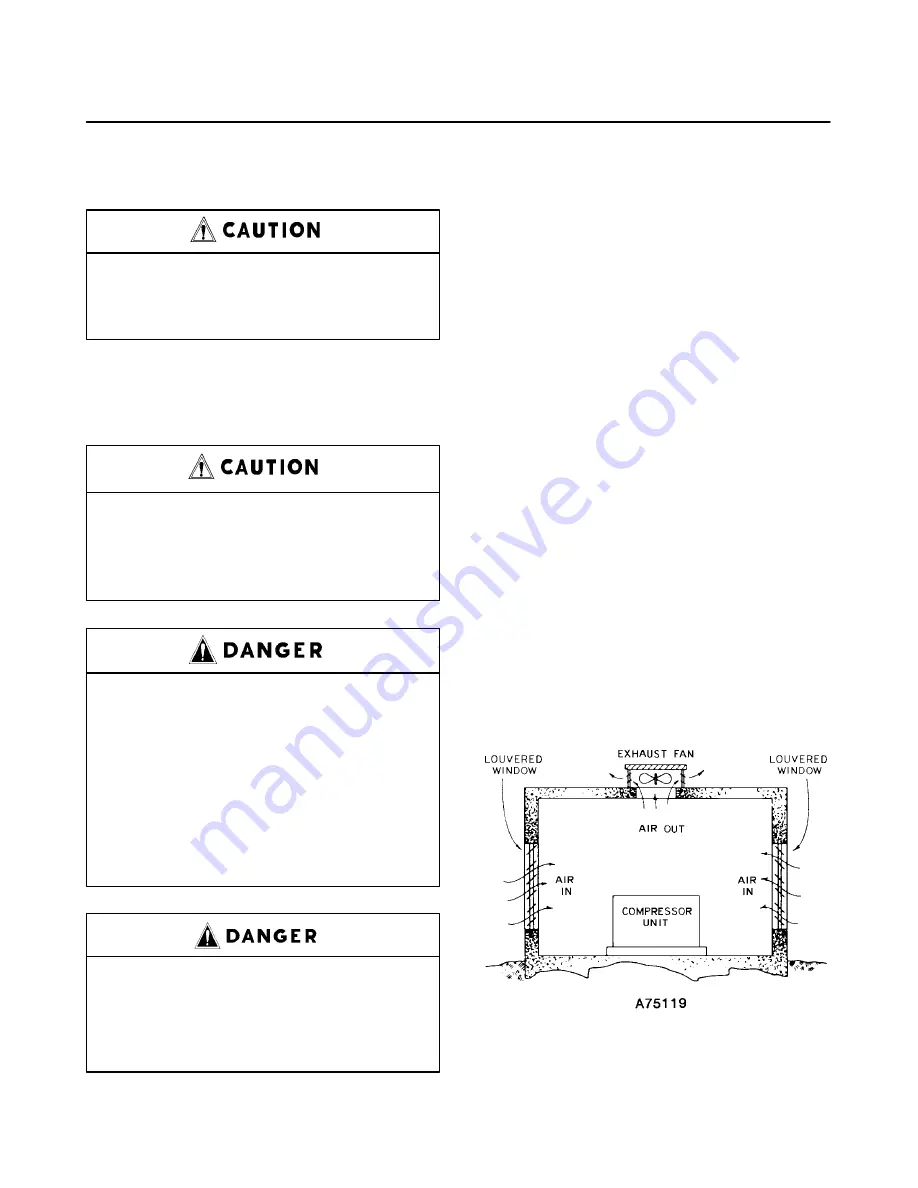
13–8–606 Page 8
SECTION 2
INSTALLATION
GENERAL – On receipt of the unit, check for any dam-
age that may have been incurred during transit. Report
any damage or missing parts as soon as possible.
Do not electric weld on the compres-
sor or base; bearings can be damaged
by passage of current.
LIFTING UNIT – Proper lifting and/or transporting
methods must be used to prevent damage. Lifting slots
are provided in the base for towmotor use. The unit may
also be moved into location by rolling on bars.
Lift compressor unit by base only. Do
not use other places such as motor,
compressor or discharge manifold
piping as lifting points.
The eyebolts or lugs provided on the
motor are for lifting the motor only
and should not be used to lift any
additional weight. All eyebolts must
be securely tightened. When lifting
the motor the lifting angle must not
exceed 15 degrees. Failure to observe
this warning may result in damage to
equipment or personal injury.
Compressor, air/oil reservoir, separa-
tion chamber and all piping and tub-
ing may be at high temperature during
and after operation.
LOCATION – The compressor should be installed,
whenever possible, in a clean, well–lighted, well–venti-
lated area with ample space all around for mainte-
nance. Select a location that provides a cool, clean, dry
source of air. In some cases it may be necessary to
install the air filter at some distance from the compres-
sor to obtain proper air supply.
Both the air–cooled and water–cooled units require
cooling air as well as air to the compressor inlet. Proper
ventilation MUST be provided; hot air must be ex-
hausted from the compressor operating area. A typical
inlet–outlet air flow arrangement is shown in
FIGURE 2–1.
Air–Cooled Units – A combination oil/aftercooler is
supplied as standard equipment on all air–cooled units.
The air–cooled unit with the standard enclosure re-
quires sufficient flow, FIGURE 2–2, page 9, for the
compressor oil/aftercooling system and for electric mo-
tor cooling. Air is drawn into the unit at the motor side
of the enclosure and is exhausted at the oil cooler side.
Do not block the air flow to and from the unit. Allow
three and one–half (3–1/2) feet (1.1 M) to the nearest
obstruction on the starter end and control box end of
the unit. Allow three (3) feet (.9 M) to the nearest ob-
struction above and on other sides of unit. For continu-
ous efficiency, oil cooler cores must be periodically
cleaned with either vacuum or compressed air. If wet
cleaning is required, shield motor and spray on a mild
soap solution and flush with clean water.
FIGURE 2–1 – TYPICAL COMPRESSOR ROOM
Содержание EDF-KB
Страница 14: ...13 8 606 Page 6 DECALS 206EAQ077 212EAQ077 218EAQ077 211EAQ077 207EAQ077...
Страница 15: ...13 8 606 Page 7 DECALS 216EAQ077 217EAQ077 222EAQ077 221EAQ077 208EAQ077...
Страница 34: ...13 8 606 Page 26 FIGURE 4 10 WIRING DIAGRAM FULL VOLTAGE DUAL CONTROL 208EDF546 Ref Drawing...
Страница 36: ...13 8 606 Page 28 FIGURE 5 1 FLOW DIAGRAM 204EDF797 Ref Drawing...
Страница 58: ......