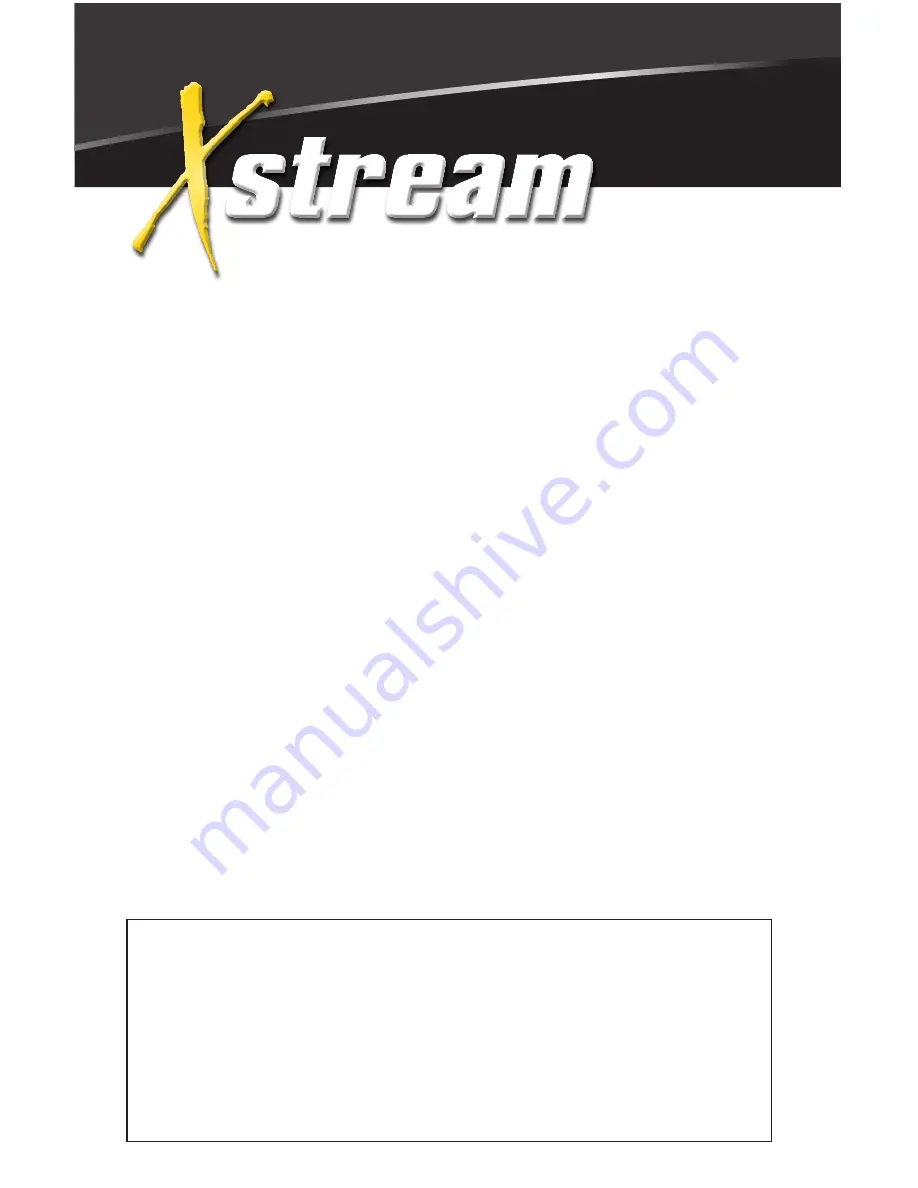
operation
manual
AC5060B
AIR COMPRESSOR
CAUTION READ THIS MANUAL CAREFULLY
before operating or servicing this
air compressor, to familiarize yourself with the proper safety, operation, and standard
operating procedures of this unit.
FAILURE TO COMPLY WITH INSTRUCTIONS IN
THIS MANUAL COULD RESULT IN THE VOIDING OF YOUR WARRANTY, AND
PERSONAL INJURY, AND/OR PROPERTY DAMAGE. THE MANUFACTURER
OF THIS AIR COMPRESSOR WILL NOT BE LIABLE FOR ANY DAMAGE
BECAUSE OF FAILURE TO FOLLOW THE INSTRUCTIONS IN THIS MANUAL.
By following the instructions and recommendations in this manual you will ensure a
longer and safer service life of your air compressor.