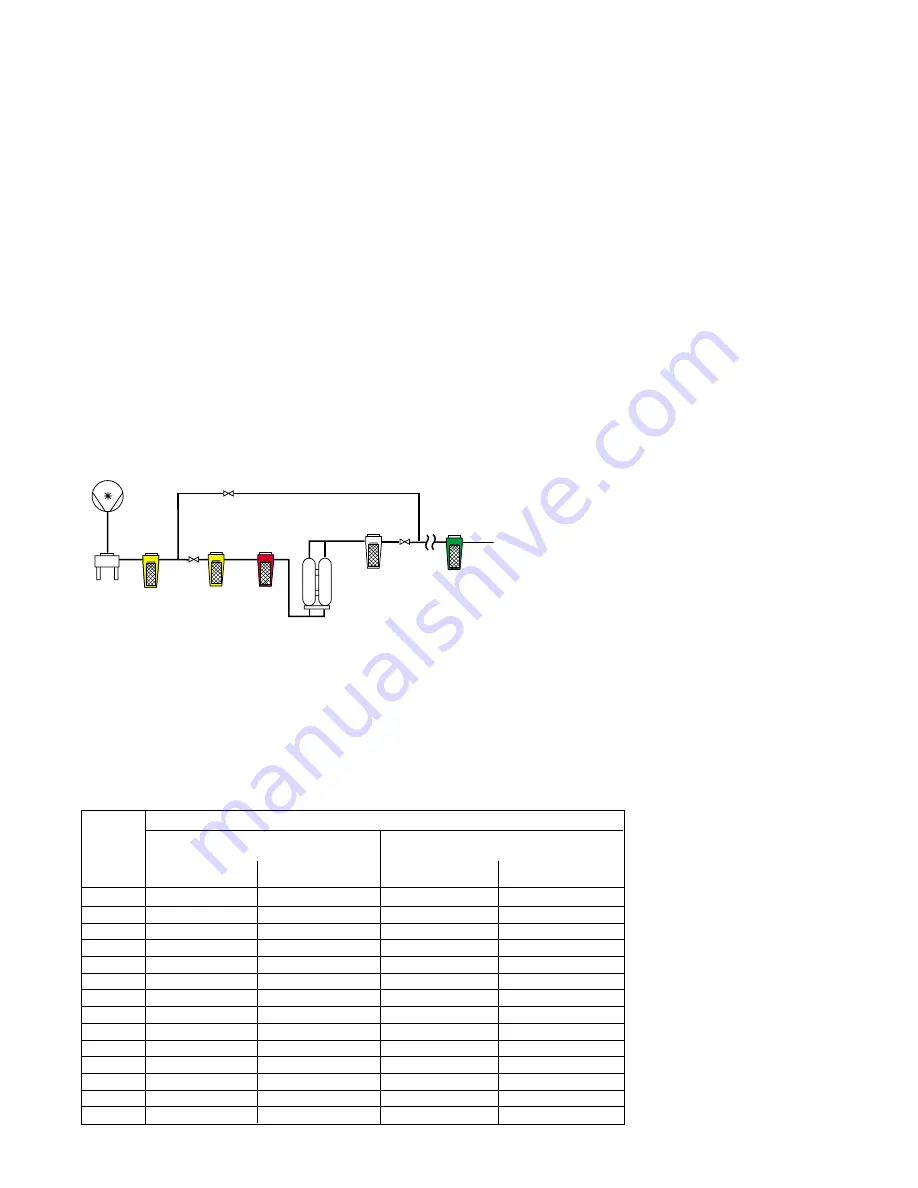
3
Minimum pipe size (IPS)*
Dryers with One Stage Regeneration
Dryers with Two Stage Regeneration
(Standard)
(Optional)
Up to 50 feet of
Up to 100 feet of
Up to 50 feet of
Up to 100 feet of
pipe plus 4 fittings
pipe plus 4 fittings
pipe plus 4 fittings
pipe plus 4 fittings
525
3
4
4
4
775
4
4
4
6
1050
4
6
6
6
1300
6
6
6
6
1575
6
6
6
6
1825
6
6
6
8
2100
6
6
6
8
2625
6
8
8
8
3150
8
8
8
8
3675
8
8
8
10
4200
8
8
10
10
4725
8
10
10
10
5250
10
10
10
10
5800
10
10
10
10
*Exhaust piping configuration - For Models and configurations other than those listed above, contact the factory for assistance.
Dryer
Model
Number
* Use if high liquid loads are present and to protect the oil removal
filter from gross contamination
** Install downstream where air has cooled to at least 150
°
F (66
°
C).
Figure 3.2 - Pipe Sizing Chart for Purge Exhaust Lines
By-Pass Valves
Compressor
Aftercooler
Blower Purge
Dryer
Separator
High
Efficiency
Oil Removal
Filter
Prefilter
(Optional)*
Oil Vapor
Removal Filter
(Optional)**
High Temperature
Afterfilter
Figure 3.1
3.0 Installation
3.1 Location in Compressed Air System
The dryer should be located downstream of an
aftercooler and separator for best performance.
Prefilters are necessary to protect the desiccant beds
from liquid and solid contamination. Locate the
prefilters as close to the dryer inlet as possible. Use
an Air Line Filter in systems supplied by a non-
lubricated (oil free) air compressor. In systems
supplied by a lubricated air compressor, use a High
Efficiency Oil Removal Filter. A coarser filter will be
required upstream of the Oil Removal Filters if heavy
liquid or solid loads are present.
An afterfilter should be used to protect downstream
equipment from desiccant dust. A High Temperature
Afterfilter, typically rated at a 450
°
F (232
°
C) operating
temperature and capable of removing all desiccant
fines 1 micron and larger should be provided.
The use of bypass valves and piping allows servicing
of the filters and/or dryer without interrupting the air
flow.
3.2 Ambient Temperature Limitations
The dryer should not be installed in an area where the
ambient temperature will exceed 120
°
F (49
°
C) or fall
below 40
°
F (4.4
°
C) unless the unit has been equipped
for operation in higher and/or lower ambient condi-
tions.
3.3 Mounting
Locate the dryer on a solid level floor. Ensure the
dryer is level by grouting or shimming as necessary.
Securely anchor the dryer frame to the floor. Provide
a four (4) foot (1.2 m) wide access area on all sides of
the dryer and overhead clearance of four (4) feet (1.2
m) for ease of servicing and visibility of instrumenta-
tion.
3.4 Air Inlet and Outlet Connections
Connect compressed air lines to the dryer inlet and
outlet using pipe of diameter equal to or larger than
the pipe size on the dryer. Be sure to use a flange
gasket suitable for high temperature on the air outlet
flange. The gasket must be able to withstand the
temperature spike that occurs at tower switchover
typically 300-325
°
F (149-163
°
C).
3.5 Electrical Hook-up
WARNING:
These procedures require gaining access
to the dryer’s electrical enclosure(s). All electrical
work must be performed by a qualified electrical
technician.
Connect the proper power supply to the dryer
according to the electrical drawings. Be sure to
follow all applicable electrical codes. After power is
connected to the dryer, manually engage the blower
motor starter to ensure proper blower rotation.
Dry contacts (voltage free) are provided in the main
electrical enclosure for a remote alarm. The contact
ratings are shown on the electrical drawing.
3.6 Purge Exhaust Piping
In some installations, it may be necessary to pipe the
purge exhaust outdoors since condensation may
become a problem. The purge exhaust piping must
be sized according to the chart shown in Figure 3.2.