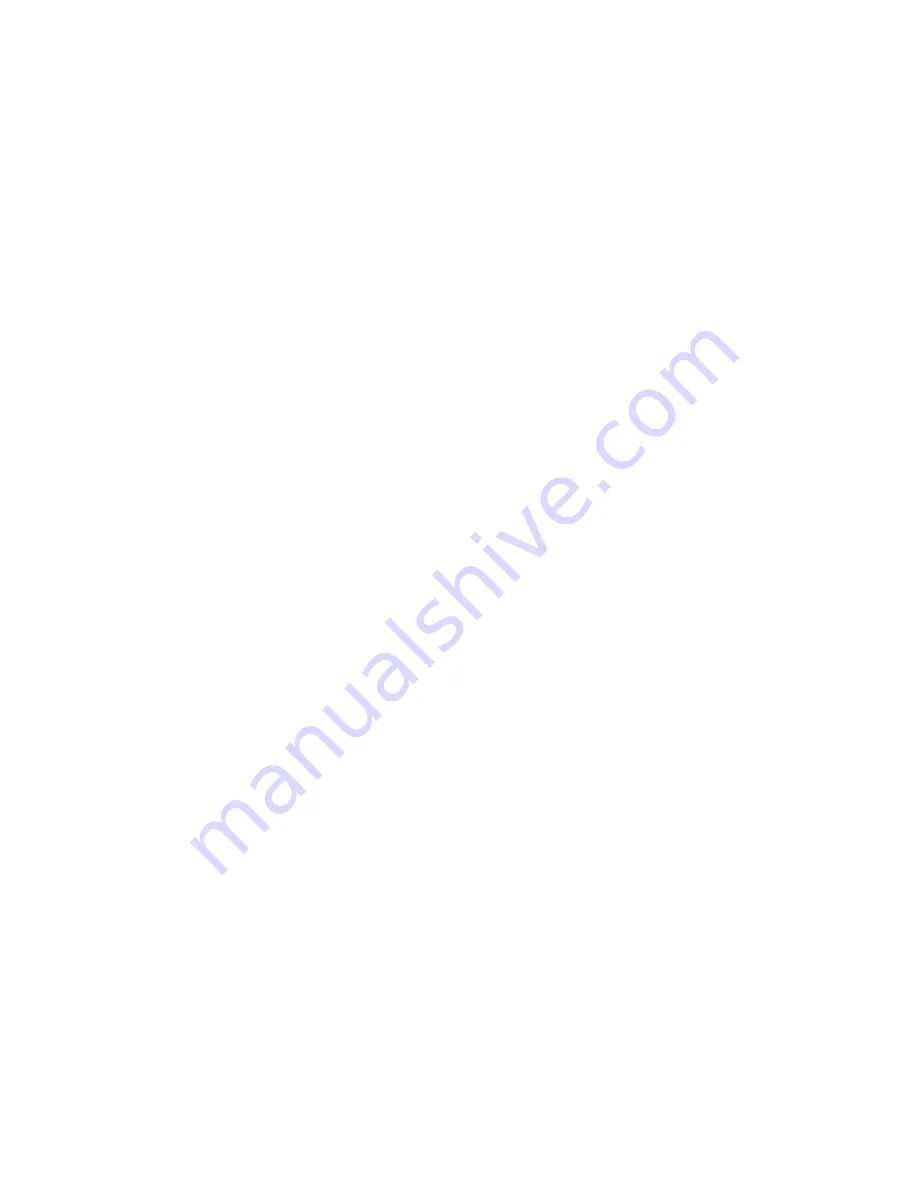
13-8-623 Page 13
Each controller circuit board has two modular jacks which accept RJ-12 telephone plugs. One jack is
vacant, the other has a short pigtail plugged into it. To interconnect two compressors, plug the cable into
the vacant jack on each controller. For installations of more than two units, the pigtail plug must be
disconnected on all controllers except the two at each end of the communications line. The order of
interconnection has no effect on the system operation. The following conditions are necessary and
sufficient for proper operation:
1. Every compressor must have a cable connecting it to another compressor. One less cable than the
number of units sequenced must be used.
2. Each board that has only one cable connected to it must have its pigtail plugged into the unused jack.
All installations will have two such units.
Program all members of the system, as described in the programming procedure on previous pages. All
adjustments should be identical for each member, except for unit number. The sequencing system will
make any necessary adjustments to the setpoints to properly run the compressed air system.
Operation -
Refer to adjustments, and program each unit for sequence operating mode. Press the
[RUN] key on each of the compressors to start operation of the sequenced system. Once this is done,
the member controllers will operate the compressor units as required to maintain the plant pressure
between the programmed Unload and Load Pressures, for average demands from 0 CFM up to the
capacity of the system.
While operating, each controller will display a sequence number. As demand requires, the units will start
and load in order, starting with sequence number 1 (lead unit). As demand falls, the higher sequence
number units (lag units) will modulate, unload, and stop.
If any member of the system is taken out of sequence mode for any reason, other units with higher
sequence numbers will automatically promote as required. Sequence numbers will start with 1, and will
be assigned on other units up to the number of compressors in the system. This feature makes the
system completely tolerant of any manual or protective stopping of any member.
ESTABLISHING THE INITIAL SEQUENCE
The first member compressor placed into sequence mode will become the lead unit. However, since any
controller first placed into sequence has no way of knowing whether or not other members already exist,
it will first assume the highest rotation number available. For example if the number of units to be
sequenced is programmed at four, any compressor will start out in position four when placed in sequence
mode. It will then listen for other units on the communications line.
If there is no member with the next lower sequence number, the controller will automatically promote
itself. This movement is fairly rapid with the controller, and the number will advance to the lowest vacant
position in several seconds.
To establish a desired order of units, press [STOP/RESET] on each compressor to remove it from the
system. Then put the desired lead unit back into sequence. Wait until it promotes one step (or longer),
then put the desired #2 unit into sequence mode and wait until it promotes one step, and so forth until all
units are back into the sequence mode.
During this procedure, the system is not deprived of air. This is due to one of the outstanding features of
the sequencing system: control is always executed locally by each member controller. So while
controllers count down towards the final order, they are also operate their compressor and will deliver air.
Once the sequence order is finally established, setpoints will continue to be adjusted in each member to
provide operation in the preferred order. This may take several minutes after a manual change of
sequence numbers.
Содержание AUTO SENTRY RS2000
Страница 11: ...13 8 623 Page 7 Figure 3 1 FLOW CHART FOR SETUP PROGRAMMING V4 xx 300EBC1255 E Ref Drawing...
Страница 21: ...13 8 623 Page 17 300EFC546 A Ref Drawing Page 1 of 2 Figure 3 2 TYPICAL WIRING DIAGRAM V4 xx...
Страница 22: ...13 8 623 Page 18 WIRING DIAGRAM 300EFC546 A Ref Drawing Pag 2 of 2...
Страница 30: ...13 8 623 Page 26 FIGURE 4 2 TYPICAL WIRING DIAGRAM V6 xx 303EFC546 A Ref Drawing Page 1 of 2...
Страница 31: ...13 8 623 Page 27 303EFC546 A Ref Drawing Page 2 of 2...