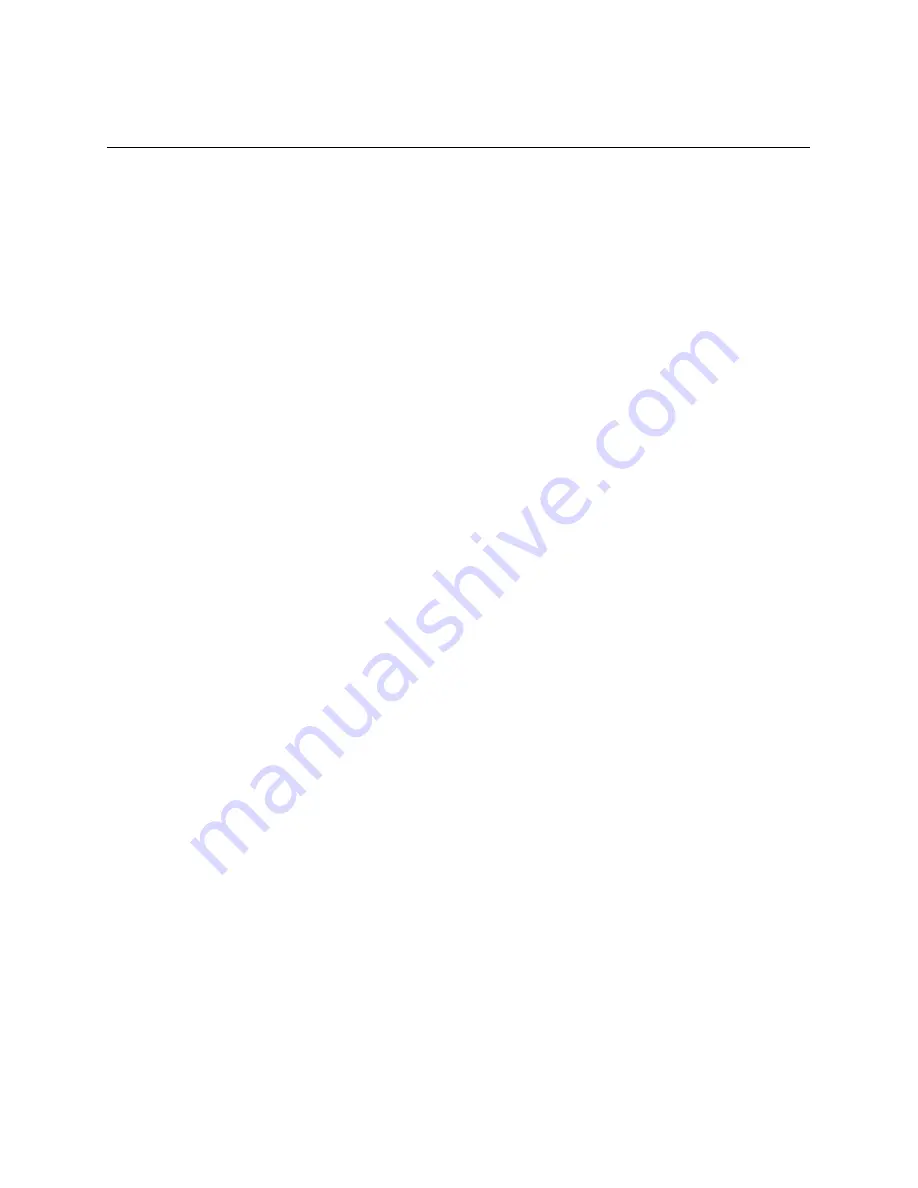
13-10-615 Page 67
SECTION 9
TROUBLESHOOTING
SYMPTOM
POSSIBLE
CAUSE
REMEDY
Compressor fails to start
1.
Wrong lead connections.
1.
Change leads.
2.
Blown fuses in control
box.
2. Replace
fuse.
3. Motor
starter
overload
heaters tripped .
3.
Reset and investigate
cause of overload.
4.
Pressure in reservoir.
4.
Inspect blowdown valve
and muffler.
5.
Read error message on
control panel
5.
Take appropriate action.
See Manual 13-9-653.
6.
Remote Contact is open
(terminals 6 & 9).
6.
Replace switch or jumper.
Compressor starts but
stops after a short time
1. High
discharge
temperature.
1.
See “High Discharge Air
Temperature,” this
section.
2. High
discharge
temperature switch
malfunction.
2. Replace
switch
3.
Blown fuse in starter/
control box.
3. Replace
fuse
(investigate
if fuses continue to blow).
4. Motor
starter
overload
heaters trip.
4.
Reset and investigate
cause of overload.
Compressor does not
unload (or load)
1. Improperly
adjusted
control.
1.
Refer to Manual 13-9-653
and adjust control.
2.
Air leak in control lines.
2.
Determine source of leak
and correct.
3.
Restricted control line.
3.
Clean control lines.
4. Blowdown
valve
malfunction.
4
Repair, clean or replace
valve.
Compressor cycles from
load to unload
excessively
1. Insufficient
receiver
capacity.
1.
Increase receiver size.
2.
Restriction in service
piping
2.
Inspect and clean service
piping.
3.
Restriction in control
tubing.
3.
Inspect and clean control
tubing.
4. Plugged
aftercooler.
4. Inspect
and
clean
aftercooler.
Содержание AUTO SENTRY EAU99P
Страница 13: ...13 10 615 Page 12 Figure 1 6 PACKAGE AIR OIL FLOW DIAGRAM 202EDM797 Ref Drawing ...
Страница 35: ...13 10 615 Page 34 Figure 4 7 CONTROL SCHEMATIC COMPRESSOR AT FULL LOAD 206EAU797 B Ref Drawing ...
Страница 38: ...13 10 615 Page 37 Figure 4 10 WIRING DIAGRAM WYE DELTA ES CONTROLLER AIR COOLED 202EAU546 D Ref Drawing ...
Страница 40: ...13 10 615 Page 39 205EAU546 D Ref Drawing Page 2 of 2 ...
Страница 44: ...13 10 615 Page 43 Figure 5 3 FLOW DIAGRAM 210EAU797 B Ref Drawing ...