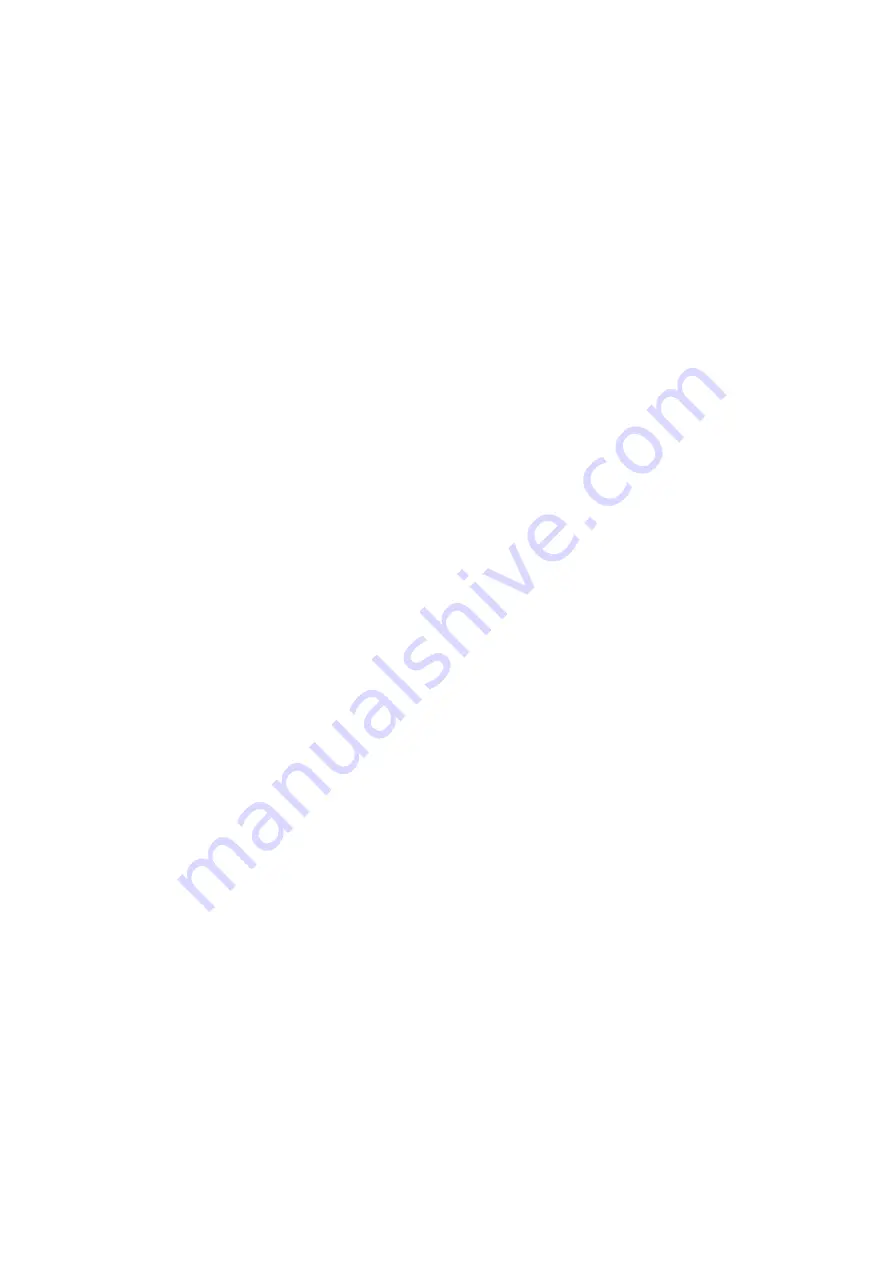
Symbols
INFORMATION
Highlights subject areas that should clarify understanding or provides tips
or hints that should assist users and/or technicians.
WARNING
The associated text highlights a subject area in which damage to equipment
may result if procedures are not carried out correctly.
General Safety Warnings and Precautions
y
Installation must only be carried out by suitably
qualified
and
competent
personnel.
y
Initial electrical power-up and opening of fuel supply lines must only be carried
out after inspection and approval by suitably qualified and competent personnel.
y
No naked flames.
y
All personnel working with Fuel Delivery Systems must be made aware of how, in
an emergency, to turn OFF power to the FDS and any remote fuel storage system.
They must also be briefed on fire fighting and other relevant inflammable liquid
safety procedures.
y
Ensure fuel pipes, flanges etc. are clear of debris before assembling.
y
Fuels present a toxic hazard and suitable precautions should be taken at all times
to prevent ingestion, inhalation and contact with skin and eyes.
y
Only use genuine spare parts. Genuine parts as specified in the original design are
integral to the correct function and safety of the system. Gallagher Fuel Systems
Ltd cannot be held responsible for any consequences of using non-genuine parts
and will not support under warranty any Gallagher FDS where substitution has
occurred. Any replacement parts should be like for like. In addition the repairer
may be legally liable for the consequences of any unauthorised modifications.
y
Do not short out isolation or intrinsic safety barriers.
y
Electronic equipment in the dispenser is susceptible to damage by electro-static
discharge (ESD). Suitable preventative measures should be taken at all times when
working on the electronic system.
y
Ensure air is bled from product lines of remote dispensers before delivering
product.
y
Damage to equipment caused by failure to correctly follow the procedures
described in this manual is not covered under warranty.
2A03229 APOLLO 3000L Installation and Commissioning Manual Issue 1
6
Содержание APOLLO 3000L
Страница 1: ...Part No 2A03229 Issue 1 APOLLO 3000L Installation and Commissioning Manual...
Страница 48: ......