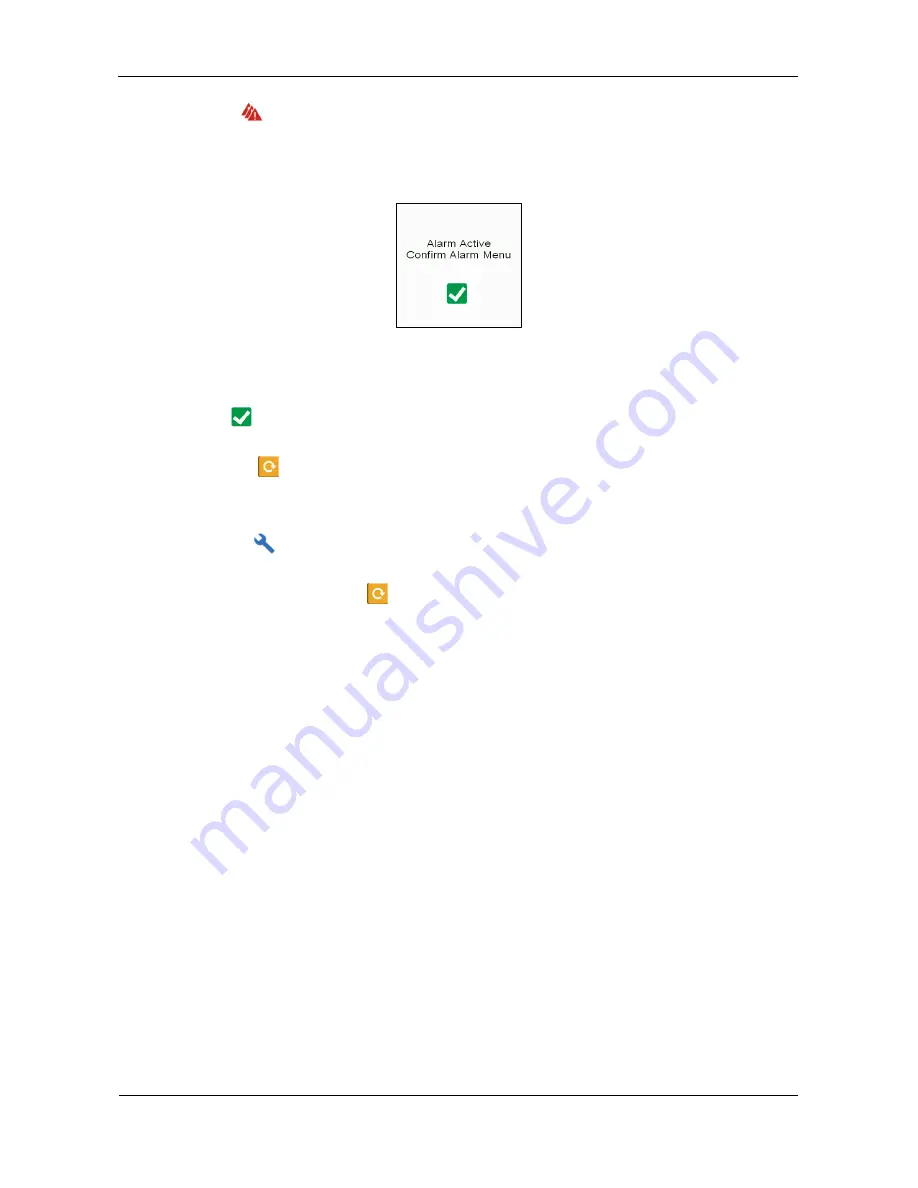
ES08
‐
15
Controller
v1.01.05
2022
‐
02
‐
03
FS
‐
Curtis
Page
36
The alarm symbol (
) will appear at the bottom of the home page screen in the event of an active alarm
and it may be preceded by the appearance of a pop-up message box, an example of which is shown in
Figure 2.19.
Figure 2.19 – Pop-Up Alarm Message
Press on the OK (
) button to acknowledge the message and then proceed to the alarm status screen to
ascertain the details. The alarm condition should be investigated, rectified as appropriate and then cleared
by pressing the reset (
) button for two seconds. If properly resolved, the alarm message will move from
the current (active) list to the historical (cleared) list on the alarm status screen.
The warning symbol (
) will appear at the bottom of the home page screen in the event of an active
operating or maintenance warning. The warning condition should be investigated, rectified as appropriate
and then cleared by pressing the reset (
) button for two seconds. If properly resolved, the warning
message will move from the current (active) list to the historical (cleared) list on the alarm status screen.
The following events will initiate an operating or maintenance alarm:
a) Air-end outlet temperature above warning value (see Table 2.3).
b) Maintenance task overdue (see Table 2.10).
The following events will initiate a shutdown alarm of an individual motor and air-end module:
a) Air-end outlet temperature above shutdown value (see Table 2.3).
b) Air-end drive motor starts per hour above shutdown value (see Table 2.5).
c) Air-end
drive
motor
overload.
Where possible, the automatic shutdown of one or more modules will not prevent any other operable
modules from running.
Содержание ECO Scroll Series
Страница 40: ......