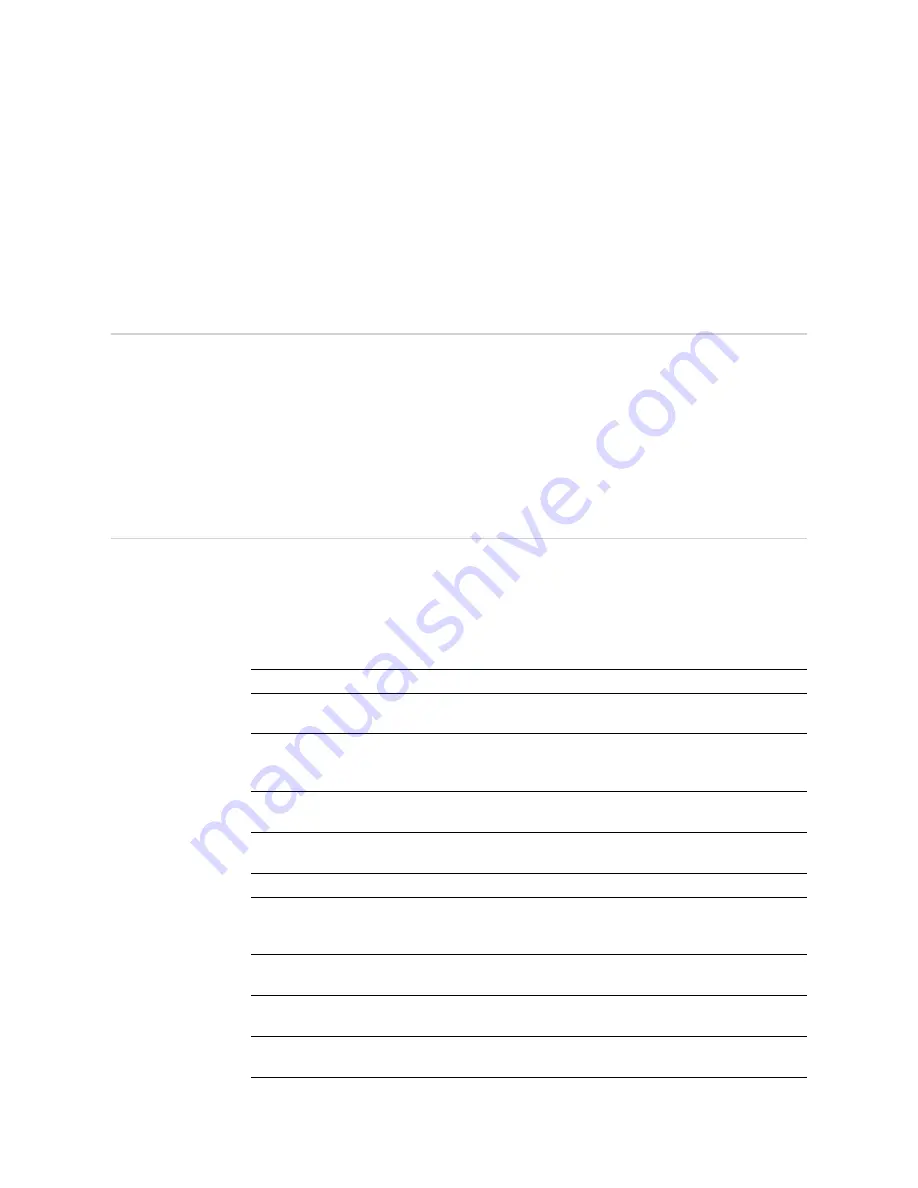
14
Supporting measures for avoidance of EMC problems:
1.
Mains supply
-
If electromagnetic interference arises despite correct mains connection, addition-
al measures are necessary (e.g. use a suitable line filter).
2.
Welding power leads
-
must be kept as short as possible
-
must run close together (to avoid EMF problems)
-
must be kept well apart from other leads
3.
Equipotential bonding
4.
Earthing of the workpiece
-
If necessary, establish an earth connection using suitable capacitors.
5.
Shielding, if necessary
-
Shield off other nearby devices
-
Shield off entire welding installation
EMF measures
Electromagnetic fields may pose as yet unknown risks to health:
-
effects on the health of others in the vicinity, e.g. wearers of pacemakers and hearing
aids
-
wearers of pacemakers must seek advice from their doctor before approaching the de-
vice or any welding that is in progress
-
for safety reasons, keep distances between the welding cables and the welder's head/
torso as large as possible
-
do not carry welding cables and hosepacks over the shoulders or wind them around
any part of the body
Specific hazards
Keep hands, hair, clothing and tools away from moving parts. For example:
-
Fans
-
Cogs
-
Rollers
-
Shafts
-
Wirespools and welding wires
Do not reach into the rotating cogs of the wire drive or into rotating drive components.
Covers and side panels may only be opened/removed while maintenance or repair work is
being carried out.
During operation
-
Ensure that all covers are closed and all side panels are fitted properly.
-
Keep all covers and side panels closed.
The welding wire emerging from the welding torch poses a high risk of injury (piercing of
the hand, injuries to the face and eyes, etc.).
Therefore always keep the welding torch away from the body (devices with wire-feed unit)
and wear suitable protective goggles.
Never touch the workpiece during or after welding - risk of burns.
Slag can jump off cooling workpieces. The specified protective equipment must therefore
also be worn when reworking workpieces, and steps must be taken to ensure that other
people are also adequately protected.
Welding torches and other parts with a high operating temperature must be allowed to cool
down before handling.
Special provisions apply in areas at risk of fire or explosion - observe relevant
national and international regulations.
Power sources for work in areas with increased electric risk (e.g. near boilers) must carry
the "Safety" sign. However, the power source must not be located in such areas.
Содержание TPS/i Robotics Pull
Страница 2: ...2...
Страница 4: ...4...
Страница 19: ...General information...
Страница 20: ......
Страница 41: ...Controls connections and mechani cal components...
Страница 42: ......
Страница 50: ...50 Side view No Function 11 Cover 12 Implementation 13 Gas test wire threading control panel option...
Страница 57: ...Installation conventional robot...
Страница 58: ......
Страница 60: ...60...
Страница 64: ...64 Fitting the TPSi wire buffer Fitting the TPSi wire buffer 1 Fitting to the robot 1 Fitting to a balancer 1 1...
Страница 70: ...70 3 3 Steel inner liner 1 1 1 1 2 3...
Страница 73: ...73 EN 1 2...
Страница 75: ...75 EN 2 Fitting the inner liner unreeling wirefeeder Split Box SB 500i R 1 2 3 4 2 1 2 3 4...
Страница 76: ...76 Fitting the inner liner SplitBox WF 25i with inter nal inner liner 1 2 3 4 1 2 3 4...
Страница 78: ...78 3 Fitting the inner liner unreeling wirefeeder wire buffer 1 2 3 4 3 1 2 3 4...
Страница 79: ...79 EN 5 Fitting the inner liner unreeling wirefeeder Split Box SB60i 1 2 3 4 5 1 2 3 4...
Страница 84: ...84...
Страница 85: ...Installation PAP...
Страница 86: ......
Страница 88: ...88 Fitting the SplitBox Fitting the SB 500i R PAP 1 2 1 2...
Страница 91: ...91 EN 5 6 Installing the CrashBox i Dum my on the robot 1 2 3 6 7 1 2 3...
Страница 95: ...95 EN 3 3 Steel inner liner 1 1 1 1 2 3...
Страница 98: ...98 1 2...
Страница 101: ...101 EN 2 3 4 Fitting the inner liner unreeling wirefeeder wire buffer 1 2 2 3 4 1 2...
Страница 102: ...102 3 4 5 Fitting the inner liner wire buffer WF Robacta Drive with internal wire feeding hose 1 2 3 4 5 1 2...
Страница 104: ...104...
Страница 105: ...Start up...
Страница 106: ......
Страница 109: ...109 EN Inserting replac ing the WF 25i Ro bacta Drive feed rollers 1 2 3 4 5 6 1 2 3 4 5 6...
Страница 110: ...110 7 8 9 10 11 12 7 8 9 10 11 12...
Страница 111: ...111 EN Inserting replac ing the WF 60i Ro bacta Drive CMT feed rollers 1 2 3 4 5 6 1 2 3 4 5 6...
Страница 112: ...112 7 8 9 10 11 12 7 8 9 10 11 12...
Страница 117: ...Troubleshooting maintenance and disposal...
Страница 118: ......
Страница 126: ...126 Replacing the WF Robacta Drive gas saver nozzle 1 2 3 4 5 6 1 2 3 4 5 6...
Страница 127: ...127 EN 7 Replacing the SB 60i R inner liner Removing the inner liner 1 2 3 4 7 1 2 3 4...
Страница 128: ...128 Inserting the inner liner 1 2 3 4 1 2 3 4...
Страница 132: ...132 Fitting wearing parts to the torch body 1 2 3 Fitting wearing parts to the torch body MTW 700 i 1 2 1 2 3 1 2...
Страница 133: ...133 EN Removing the CrashBox PAP from the robot 1 2 3 4 5 6 1 2 3 4 5 6...
Страница 134: ...134 7 8 9 Disposal Dispose of in accordance with the applicable national and local regulations 7 8 9...
Страница 135: ...Technical data...
Страница 136: ......
Страница 146: ......
Страница 147: ......