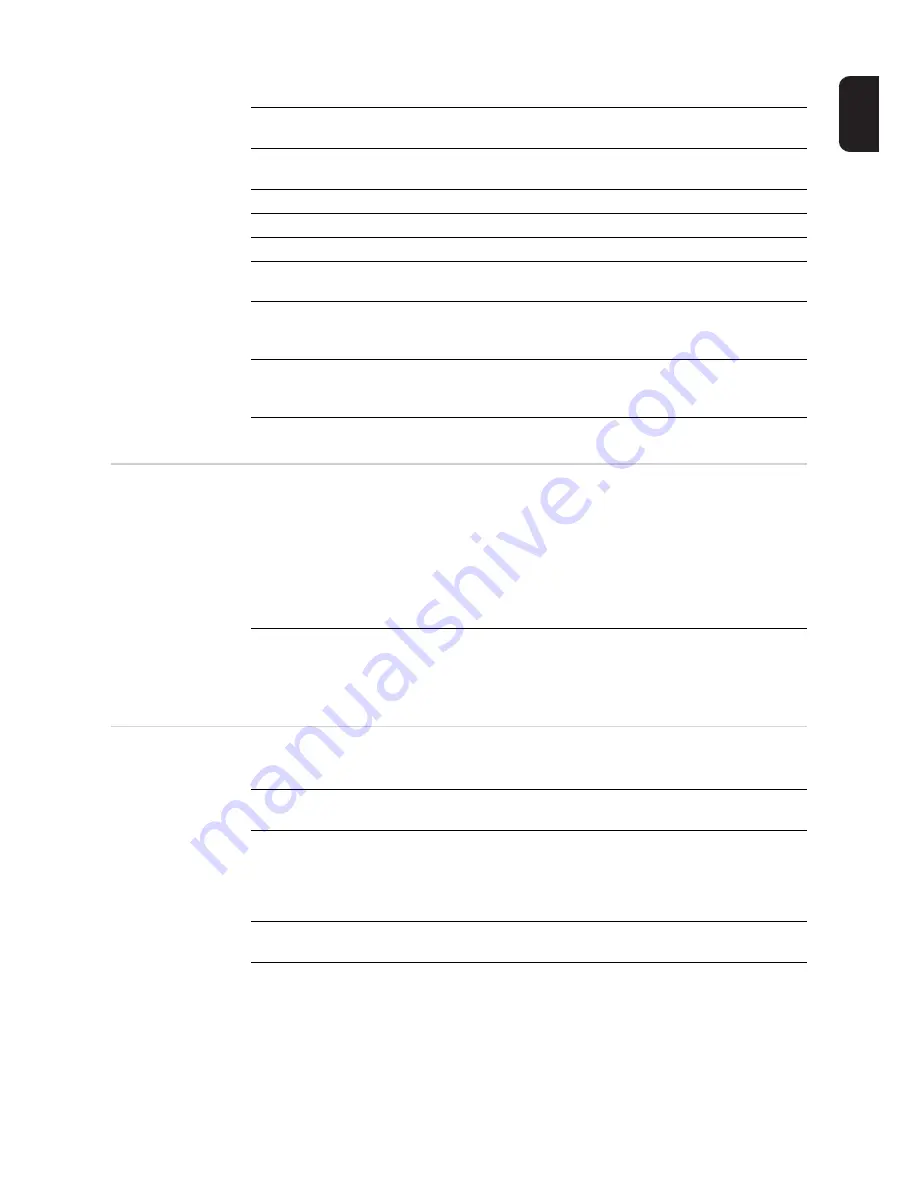
17
EN
Check the device at least once a week for obvious damage and proper functioning of safety
devices.
Always fasten the shielding gas cylinder securely and remove it beforehand if the device
is to be transported by crane.
Only the manufacturer's original coolant is suitable for use with our devices due to its prop-
erties (electrical conductibility, anti-freeze agent, material compatibility, flammability, etc.).
Only use suitable original coolant from the manufacturer.
Do not mix the manufacturer's original coolant with other coolants.
Only connect the manufacturer's system components to the cooling circuit.
The manufacturer accepts no liability for damage resulting from use of other system com-
ponents or a different coolant. In addition, all warranty claims will be forfeited.
Cooling Liquid FCL 10/20 does not ignite. The ethanol-based coolant can ignite under cer-
tain conditions. Transport the coolant only in its original, sealed containers and keep well
away from any sources of ignition.
Used coolant must be disposed of properly in accordance with the relevant national and
international regulations. The coolant safety data sheet may be obtained from your service
centre or downloaded from the manufacturer's website.
Check the coolant level before starting to weld, while the system is still cool.
Commissioning,
maintenance and
repair
It is impossible to guarantee that bought-in parts are designed and manufactured to meet
the demands made of them, or that they satisfy safety requirements.
-
Use only original spare and wearing parts (also applies to standard parts).
-
Do not carry out any modifications, alterations, etc. to the device without the manufac-
turer's consent.
-
Components that are not in perfect condition must be replaced immediately.
-
When ordering, please give the exact designation and part number as shown in the
spare parts list, as well as the serial number of your device.
The housing screws provide the ground conductor connection for earthing the housing
parts.
Only use original housing screws in the correct number and tightened to the specified
torque.
Safety inspection
The manufacturer recommends that a safety inspection of the device is performed at least
once every 12 months.
The manufacturer recommends that the power source be calibrated during the same 12-
month period.
A safety inspection should be carried out by a qualified electrician
-
after any changes are made
-
after any additional parts are installed, or after any conversions
-
after repair, care and maintenance has been carried out
-
at least every twelve months.
For safety inspections, follow the appropriate national and international standards and di-
rectives.
Further details on safety inspection and calibration can be obtained from your service cen-
tre. They will provide you on request with any documents you may require.
Содержание TPS/i Robotics Pull
Страница 2: ...2...
Страница 4: ...4...
Страница 19: ...General information...
Страница 20: ......
Страница 41: ...Controls connections and mechani cal components...
Страница 42: ......
Страница 50: ...50 Side view No Function 11 Cover 12 Implementation 13 Gas test wire threading control panel option...
Страница 57: ...Installation conventional robot...
Страница 58: ......
Страница 60: ...60...
Страница 64: ...64 Fitting the TPSi wire buffer Fitting the TPSi wire buffer 1 Fitting to the robot 1 Fitting to a balancer 1 1...
Страница 70: ...70 3 3 Steel inner liner 1 1 1 1 2 3...
Страница 73: ...73 EN 1 2...
Страница 75: ...75 EN 2 Fitting the inner liner unreeling wirefeeder Split Box SB 500i R 1 2 3 4 2 1 2 3 4...
Страница 76: ...76 Fitting the inner liner SplitBox WF 25i with inter nal inner liner 1 2 3 4 1 2 3 4...
Страница 78: ...78 3 Fitting the inner liner unreeling wirefeeder wire buffer 1 2 3 4 3 1 2 3 4...
Страница 79: ...79 EN 5 Fitting the inner liner unreeling wirefeeder Split Box SB60i 1 2 3 4 5 1 2 3 4...
Страница 84: ...84...
Страница 85: ...Installation PAP...
Страница 86: ......
Страница 88: ...88 Fitting the SplitBox Fitting the SB 500i R PAP 1 2 1 2...
Страница 91: ...91 EN 5 6 Installing the CrashBox i Dum my on the robot 1 2 3 6 7 1 2 3...
Страница 95: ...95 EN 3 3 Steel inner liner 1 1 1 1 2 3...
Страница 98: ...98 1 2...
Страница 101: ...101 EN 2 3 4 Fitting the inner liner unreeling wirefeeder wire buffer 1 2 2 3 4 1 2...
Страница 102: ...102 3 4 5 Fitting the inner liner wire buffer WF Robacta Drive with internal wire feeding hose 1 2 3 4 5 1 2...
Страница 104: ...104...
Страница 105: ...Start up...
Страница 106: ......
Страница 109: ...109 EN Inserting replac ing the WF 25i Ro bacta Drive feed rollers 1 2 3 4 5 6 1 2 3 4 5 6...
Страница 110: ...110 7 8 9 10 11 12 7 8 9 10 11 12...
Страница 111: ...111 EN Inserting replac ing the WF 60i Ro bacta Drive CMT feed rollers 1 2 3 4 5 6 1 2 3 4 5 6...
Страница 112: ...112 7 8 9 10 11 12 7 8 9 10 11 12...
Страница 117: ...Troubleshooting maintenance and disposal...
Страница 118: ......
Страница 126: ...126 Replacing the WF Robacta Drive gas saver nozzle 1 2 3 4 5 6 1 2 3 4 5 6...
Страница 127: ...127 EN 7 Replacing the SB 60i R inner liner Removing the inner liner 1 2 3 4 7 1 2 3 4...
Страница 128: ...128 Inserting the inner liner 1 2 3 4 1 2 3 4...
Страница 132: ...132 Fitting wearing parts to the torch body 1 2 3 Fitting wearing parts to the torch body MTW 700 i 1 2 1 2 3 1 2...
Страница 133: ...133 EN Removing the CrashBox PAP from the robot 1 2 3 4 5 6 1 2 3 4 5 6...
Страница 134: ...134 7 8 9 Disposal Dispose of in accordance with the applicable national and local regulations 7 8 9...
Страница 135: ...Technical data...
Страница 136: ......
Страница 146: ......
Страница 147: ......