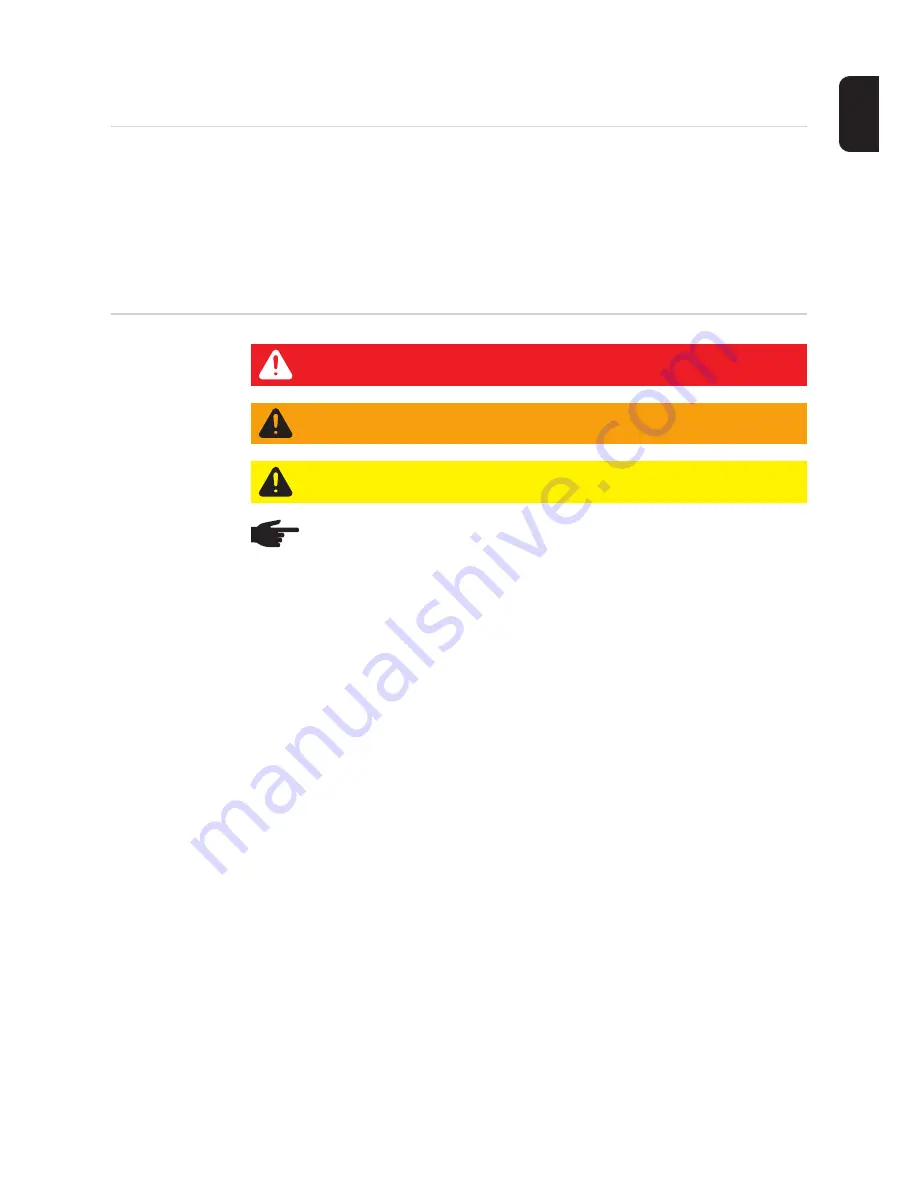
3
EN
Dear reader,
Introduction
Thank you for the trust you have placed in our company and congratulations on buying this
high-quality Fronius product. These instructions will help you familiarise yourself with the
product. Reading the instructions carefully will enable you to learn about the many different
features it has to offer. This will allow you to make full use of its advantages.
Please also note the safety rules to ensure greater safety when using the product. Careful
handling of the product will repay you with years of safe and reliable operation. These are
essential prerequisites for excellent results.
Explanation of
safety symbols
If you see any of the symbols depicted in the "Safety rules" chapter, special care is re-
quired.
DANGER!
Indicates immediate and real danger. If it is not avoided, death or se-
rious injury will result.
WARNING!
Indicates a potentially dangerous situation. Death or serious injury
may result if appropriate precautions are not taken.
CAUTION!
Indicates a situation where damage or injury could occur. If it is not
avoided, minor injury and/or damage to property may result.
NOTE!
Indicates a risk of flawed results and possible damage to the equipment.
IMPORTANT!
Indicates tips for correct operation and other particularly useful information.
It does not indicate a potentially damaging or dangerous situation.
Содержание TPS/i Robotics Pull
Страница 2: ...2...
Страница 4: ...4...
Страница 19: ...General information...
Страница 20: ......
Страница 41: ...Controls connections and mechani cal components...
Страница 42: ......
Страница 50: ...50 Side view No Function 11 Cover 12 Implementation 13 Gas test wire threading control panel option...
Страница 57: ...Installation conventional robot...
Страница 58: ......
Страница 60: ...60...
Страница 64: ...64 Fitting the TPSi wire buffer Fitting the TPSi wire buffer 1 Fitting to the robot 1 Fitting to a balancer 1 1...
Страница 70: ...70 3 3 Steel inner liner 1 1 1 1 2 3...
Страница 73: ...73 EN 1 2...
Страница 75: ...75 EN 2 Fitting the inner liner unreeling wirefeeder Split Box SB 500i R 1 2 3 4 2 1 2 3 4...
Страница 76: ...76 Fitting the inner liner SplitBox WF 25i with inter nal inner liner 1 2 3 4 1 2 3 4...
Страница 78: ...78 3 Fitting the inner liner unreeling wirefeeder wire buffer 1 2 3 4 3 1 2 3 4...
Страница 79: ...79 EN 5 Fitting the inner liner unreeling wirefeeder Split Box SB60i 1 2 3 4 5 1 2 3 4...
Страница 84: ...84...
Страница 85: ...Installation PAP...
Страница 86: ......
Страница 88: ...88 Fitting the SplitBox Fitting the SB 500i R PAP 1 2 1 2...
Страница 91: ...91 EN 5 6 Installing the CrashBox i Dum my on the robot 1 2 3 6 7 1 2 3...
Страница 95: ...95 EN 3 3 Steel inner liner 1 1 1 1 2 3...
Страница 98: ...98 1 2...
Страница 101: ...101 EN 2 3 4 Fitting the inner liner unreeling wirefeeder wire buffer 1 2 2 3 4 1 2...
Страница 102: ...102 3 4 5 Fitting the inner liner wire buffer WF Robacta Drive with internal wire feeding hose 1 2 3 4 5 1 2...
Страница 104: ...104...
Страница 105: ...Start up...
Страница 106: ......
Страница 109: ...109 EN Inserting replac ing the WF 25i Ro bacta Drive feed rollers 1 2 3 4 5 6 1 2 3 4 5 6...
Страница 110: ...110 7 8 9 10 11 12 7 8 9 10 11 12...
Страница 111: ...111 EN Inserting replac ing the WF 60i Ro bacta Drive CMT feed rollers 1 2 3 4 5 6 1 2 3 4 5 6...
Страница 112: ...112 7 8 9 10 11 12 7 8 9 10 11 12...
Страница 117: ...Troubleshooting maintenance and disposal...
Страница 118: ......
Страница 126: ...126 Replacing the WF Robacta Drive gas saver nozzle 1 2 3 4 5 6 1 2 3 4 5 6...
Страница 127: ...127 EN 7 Replacing the SB 60i R inner liner Removing the inner liner 1 2 3 4 7 1 2 3 4...
Страница 128: ...128 Inserting the inner liner 1 2 3 4 1 2 3 4...
Страница 132: ...132 Fitting wearing parts to the torch body 1 2 3 Fitting wearing parts to the torch body MTW 700 i 1 2 1 2 3 1 2...
Страница 133: ...133 EN Removing the CrashBox PAP from the robot 1 2 3 4 5 6 1 2 3 4 5 6...
Страница 134: ...134 7 8 9 Disposal Dispose of in accordance with the applicable national and local regulations 7 8 9...
Страница 135: ...Technical data...
Страница 136: ......
Страница 146: ......
Страница 147: ......