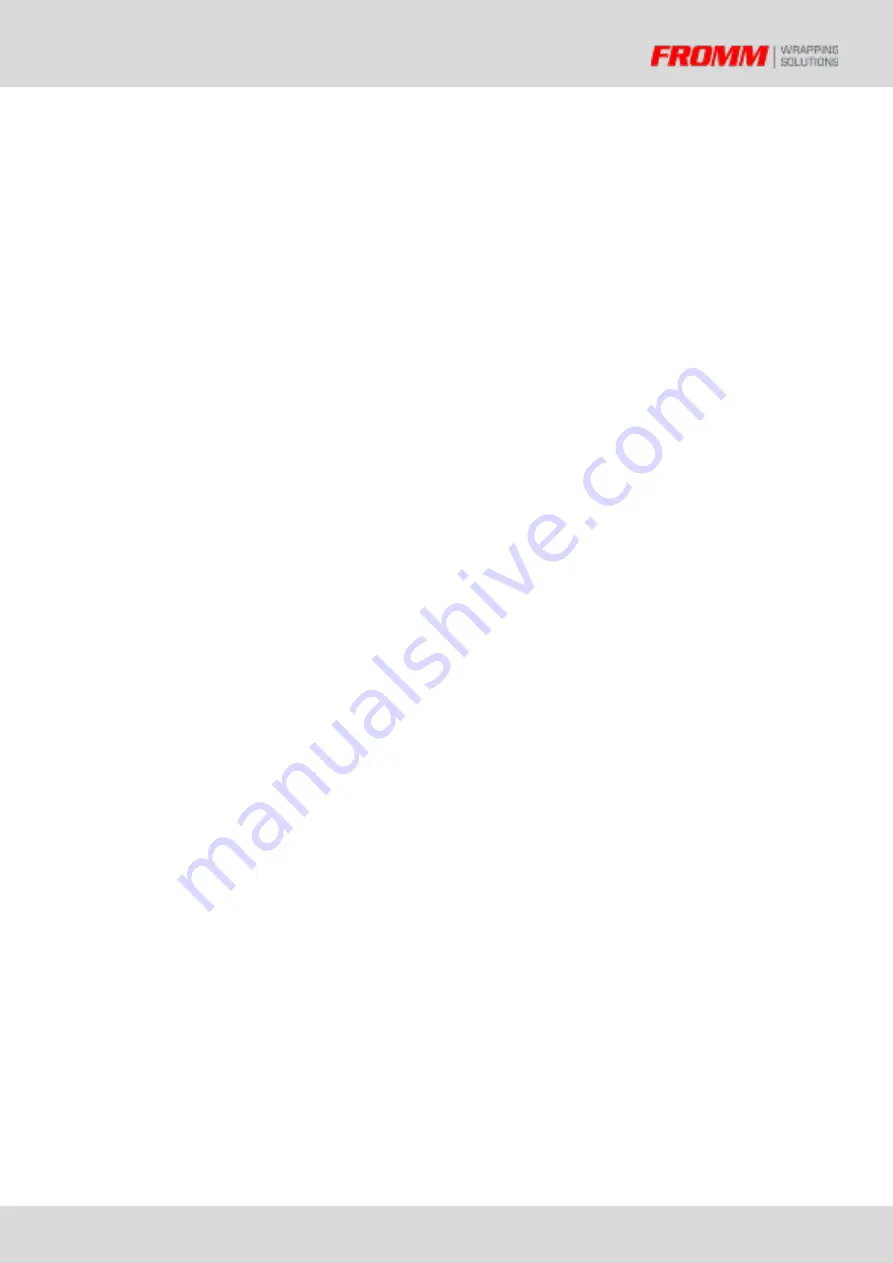
Fromm
SUMMARY
III
6.2 INSTRUCTIONS FOR USE ..................................................................... 82
6.2.1 LOADING A ROLL OF FILM .......................................................... 82
6.2.2 STARTING THE MACHINE ............................................................ 82
6.2.3 CYCLE STOP ................................................................................. 83
6.2.4 STOPPING THE MACHINE AFTER USE ........................................ 83
6.2.5 EMERGENCY STOP ...................................................................... 83
6.2.6 SAFETY SYSTEMS EFFICIENCY CHECK ......................................... 84
6.2.7 EMERGENCY BUTTONS OPERATIONAL CHECK .......................... 84
7.1 GENERAL PRECAUTIONS ..................................................................... 85
7.2 SCHEDULED MAINTENANCE ............................................................... 86
7.2.1 ACTIVE SAFETY DEVICES MAINTENANCE ................................... 87
7.2.2 DAILY MAINTENANCE ................................................................. 88
7.2.3 QUARTERLY MAINTENANCE ....................................................... 88
7.2.4 SIX-MONTHLY MAINTENANCE .................................................... 91
Содержание FS380
Страница 2: ...Rev 2 01 03 2021 SUMMARY 2 ...
Страница 6: ...IV Rev 2 01 03 2021 Use and Maintenance Manual TURNTABLE MAST IV ...
Страница 8: ...2 Rev 2 01 03 2021 Use and Maintenance Manual TURNTABLE MAST 2 ...
Страница 33: ...Fromm 27 MACHINE DESCRIPTION 27 ...
Страница 54: ...48 Rev 2 01 03 2021 Use and Maintenance Manual TURNTABLE MAST 48 ...
Страница 57: ...Fromm 51 MACHINE DESCRIPTION 51 OPTIONAL OPTIONAL H M E I B A D Ø N 0 L G F Picture 31 ...
Страница 65: ...Fromm 59 TRANSPORT HANDLING STORAGE 59 ...
Страница 99: ......
Страница 100: ...Fromm Holding AG Hinterbergstrasse 26 6312 Steinhausen Switzerland ...