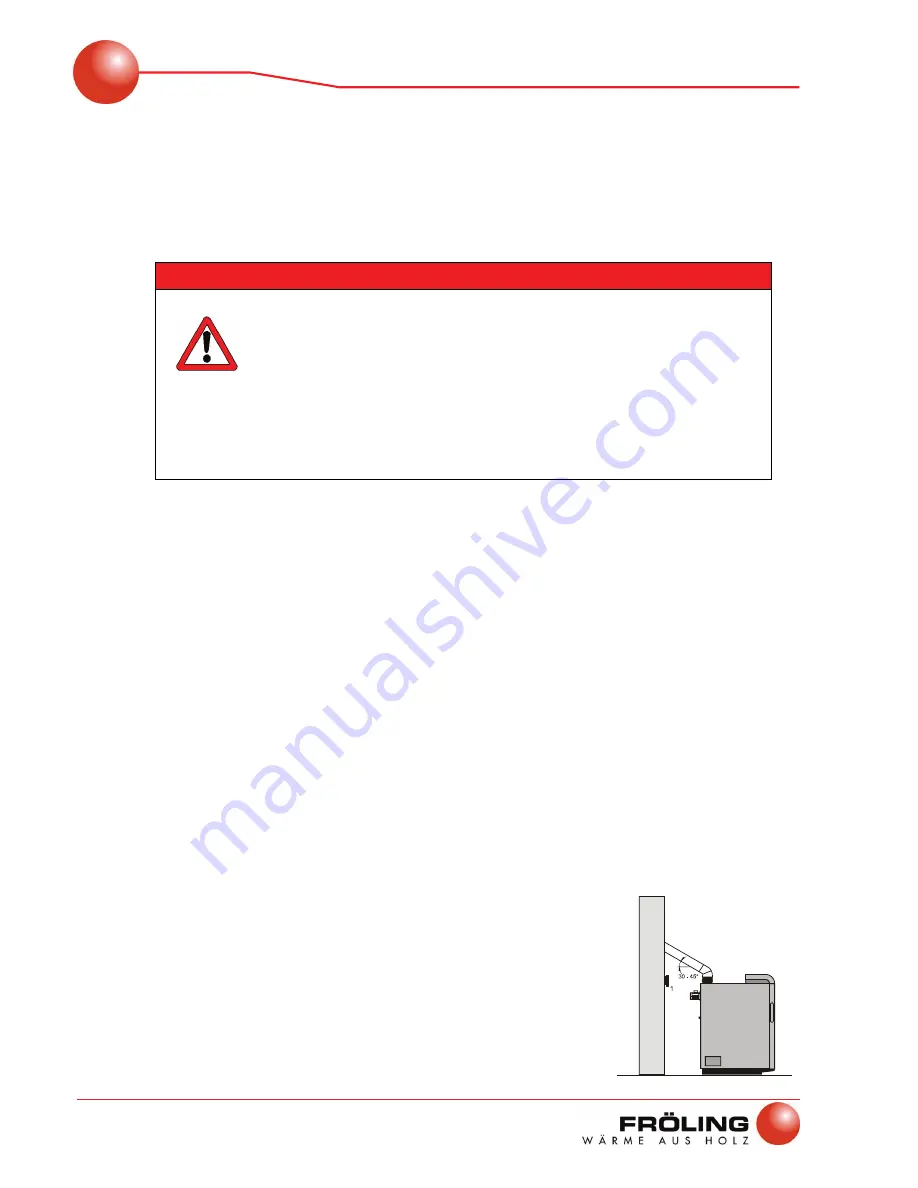
Safety
Safety Information
Page 8
a
B 003 04 05
a
2
2.2.4
Heating System Installation/Standards
ÖNORM/DIN EN 12828 governs the installation of the heating system:
Return feed lift
If the heated water return feed is under the minimum return temperature, a portion of the heated
water outfeed will be mixed in.
IMPORTANT
Operating without return feed lift!
Damage may result from dropping below the dew point or the formation of
condensation!
In combination with combustion residues, the condensation forms a caustic condensate which
shortens the service life of the boiler!
Take the following precautions:
A return feed lift is a regulatory requirement!
2.2.5
Chimney Connection / Chimney System
As per EN 303-5, the entire flue gas system is to be designed in such a way as to prevent
possible seepage damage, insufficient feed pressure, and condensation.
In relation to this, it’s necessary to point out that flue gas temperatures of less than 160 K above
room temperature can occur within the permitted operating range of the boiler.
The flue gas temperatures in the cleaned state as well as additional flue gas values can be
found in the table “
Boiler Data for Configuring the Chimney”
in the assembly instructions.
Design information
Make a connection using the shortest path rising between 30 – 45° to the chimney and insulate
the connecting piece.
The entire flue gas system, the chimney and its connection, must be laid out as per
ÖNORM/DIN EN13384-1.
In addition, local and other lawful regulations apply!
The chimney must be approved by a smoke trap sweeper or chimney sweep!
As per TRVB H 118, an explosion flap must be installed in the flue gas pipe or in the
chimney!
Draught limiter
Recommended: Installing a draught limiter
A
Attaching the draught limiter:
U
Directly under the mouth of the flue gas line, since an under-
pressure condition can always be found there!
A